Introduction to Layout and Schematic Design
When it comes to designing electronic circuits, the schematic and layout are two essential components that work hand in hand. The schematic represents the logical connections and components of the circuit, while the layout is the physical representation of how those components will be arranged on a printed circuit board (PCB). In this article, we will explore the process of creating a layout from a schematic, including best practices, tools, and techniques to ensure a successful PCB design.
The Importance of a Well-Designed Layout
A well-designed layout is crucial for several reasons:
- Functionality: A proper layout ensures that the circuit functions as intended, with minimal signal integrity issues, crosstalk, and electromagnetic interference (EMI).
- Manufacturability: A layout that adheres to manufacturing guidelines and constraints can be easily fabricated, assembled, and tested, reducing the likelihood of production delays and costs.
- Reliability: A well-designed layout can enhance the reliability and longevity of the circuit by minimizing stress on components, ensuring proper heat dissipation, and protecting against environmental factors.
The Layout Design Process
Step 1: Preparing the Schematic
Before starting the layout design, it is essential to have a complete and accurate schematic. The schematic should include all the necessary components, their values, and their interconnections. It is also important to assign unique reference designators to each component, which will be used to identify them in the layout.
Step 2: Defining the Board Outline and Constraints
The next step is to define the board outline and any mechanical constraints, such as mounting holes, connectors, and heat sinks. This information is typically provided by the mechanical engineer or the product designer. The layout designer should also consider any electrical constraints, such as the required clearance between components, the minimum trace width and spacing, and the maximum allowable voltage and current.
Step 3: Placing the Components
With the board outline and constraints defined, the layout designer can begin placing the components on the board. The placement should be guided by the schematic, with components grouped logically and placed in a way that minimizes the length of the traces between them. Critical components, such as processors, memory, and power regulators, should be placed first, followed by the rest of the components.
Step 4: Routing the Traces
Once the components are placed, the layout designer can start routing the traces between them. The routing should follow the schematic, with each connection represented by a trace on the board. The traces should be as short and direct as possible to minimize signal integrity issues and reduce the overall board size. The layout designer should also consider the width and spacing of the traces, as well as any special requirements, such as matched lengths for differential pairs or controlled impedance for high-speed signals.
Step 5: Adding Power and Ground Planes
Power and ground planes are essential for providing a low-impedance path for the power and ground signals, as well as for shielding the signals from EMI. The layout designer should add power and ground planes to the appropriate layers of the board, ensuring that they are properly connected to the power and ground pins of the components. The planes should also be split into separate regions for different power domains, such as analog and digital, to minimize noise coupling.
Step 6: Checking the Layout
Before finalizing the layout, the designer should perform a thorough check to ensure that all the connections are correct, the traces are properly routed, and the manufacturability and reliability requirements are met. This can be done using a design rule check (DRC) tool, which automatically verifies the layout against a set of predefined rules. The designer should also perform a visual inspection of the layout to catch any issues that may have been missed by the DRC.
Best Practices for Layout Design
To ensure a successful layout design, there are several best practices that should be followed:
Keep the Schematic and Layout in Sync
As the layout progresses, it is important to keep the schematic and layout in sync. Any changes made to the schematic should be reflected in the layout, and vice versa. This can be achieved using a schematic capture tool that automatically updates the layout when changes are made to the schematic.
Use a Consistent Naming Convention
Using a consistent naming convention for the components, nets, and layers can help to avoid confusion and errors during the layout process. The naming convention should be based on the functionality of the components and the purpose of the nets and layers.
Follow the Manufacturer’s Guidelines
Each component manufacturer provides guidelines for the placement and routing of their components. These guidelines should be followed to ensure proper functionality and reliability of the circuit. The guidelines may include recommendations for the pad size and shape, the spacing between components, and the routing of critical signals.
Use a Grid and Snap Settings
Using a grid and snap settings can help to ensure that the components and traces are aligned properly and spaced evenly. This can improve the overall appearance of the layout and make it easier to route the traces.
Minimize the Number of Vias
Vias are holes drilled through the PCB to connect traces on different layers. While vias are necessary for multi-layer boards, they can add cost and complexity to the manufacturing process. The layout designer should minimize the number of vias by routing the traces on the same layer whenever possible.
Consider the Assembly Process
The layout should be designed with the assembly process in mind. The components should be placed in a way that allows for easy and efficient assembly, with sufficient space for the pick-and-place machine and the soldering process. The layout designer should also consider the orientation of the components, as some components may require a specific orientation for proper assembly.
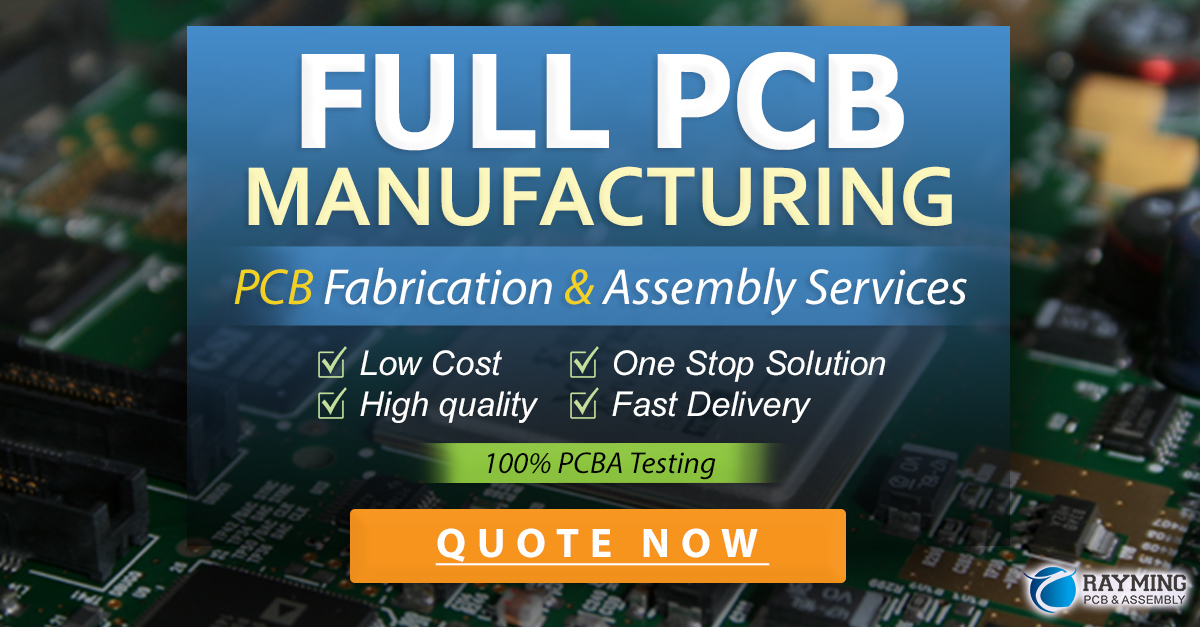
Tools for Layout Design
There are several tools available for layout design, ranging from simple PCB editors to complex electronic design automation (EDA) software. Some of the most popular tools include:
Tool | Description |
---|---|
Altium Designer | A comprehensive EDA software suite that includes schematic capture, layout design, and simulation tools |
Cadence Allegro | A high-end EDA software suite that is widely used in the aerospace and defense industries |
KiCad | A free and open-source EDA software suite that includes schematic capture, layout design, and simulation tools |
Eagle | A popular PCB design software that is owned by Autodesk and is widely used by hobbyists and small businesses |
Frequently Asked Questions (FAQ)
1. What is the difference between a schematic and a layout?
A schematic is a logical representation of a circuit, showing the components and their interconnections. A layout, on the other hand, is a physical representation of the circuit, showing how the components will be arranged on a PCB.
2. Can I create a layout without a schematic?
While it is possible to create a layout without a schematic, it is not recommended. A schematic provides a clear and organized representation of the circuit, which can help to avoid errors and inconsistencies in the layout.
3. How do I choose the right PCB manufacturer for my layout?
When choosing a PCB manufacturer, there are several factors to consider, such as the manufacturer’s capabilities, quality, turnaround time, and cost. It is important to select a manufacturer that can meet your specific requirements and has a proven track record of delivering high-quality PCBs.
4. What is the difference between a single-layer and a multi-layer PCB?
A Single-Layer PCB has all the components and traces on one side of the board, while a multi-layer PCB has multiple layers of traces and planes sandwiched between insulating layers. Multi-layer PCBs are typically used for more complex circuits that require a higher density of components and traces.
5. How can I ensure the reliability of my PCB layout?
To ensure the reliability of your PCB layout, it is important to follow best practices such as minimizing the number of vias, using a consistent naming convention, following the manufacturer’s guidelines, and considering the assembly process. It is also important to perform thorough testing and validation of the layout before proceeding to manufacturing.
Conclusion
Creating a layout from a schematic is a critical step in the PCB design process. By following best practices, using the right tools, and considering the manufacturability and reliability requirements, designers can create layouts that are functional, efficient, and cost-effective. With the increasing complexity of modern electronic circuits, the importance of a well-designed layout cannot be overstated. By understanding the principles and techniques of layout design, engineers and designers can create PCBs that meet the highest standards of quality and performance.
Leave a Reply