Introduction to Production Holes
In the oil and gas industry, a production hole refers to the drilled wellbore that is used to extract hydrocarbons (oil and gas) from underground reservoirs to the surface. The diameter of the production hole is a critical factor that impacts the well’s productivity, efficiency, and overall performance.
Key Factors Influencing Production Hole Diameter
Several factors influence the selection of the appropriate production hole diameter:
-
Reservoir characteristics: The properties of the reservoir rock, such as permeability, porosity, and fluid saturation, play a significant role in determining the optimal production hole diameter. For example, reservoirs with high permeability may require larger hole diameters to maximize flow rates.
-
Well depth: The depth of the well is another crucial factor in selecting the production hole diameter. Deeper wells generally require smaller hole diameters due to the increased cost and technical challenges associated with drilling and completing deep wells.
-
Production targets: The desired production rates and the expected life of the well also influence the choice of production hole diameter. Wells with higher production targets may require larger hole diameters to accommodate higher flow rates and reduce pressure losses.
-
Completion design: The type of completion (cased hole or open hole) and the number and size of production tubing strings also impact the selection of the production hole diameter. The hole diameter must be large enough to accommodate the completion equipment while minimizing the annular space between the tubing and the wellbore.
Typical Production Hole Diameters
Production hole diameters can vary significantly depending on the specific requirements of each well. However, there are some common hole sizes used in the industry:
Hole Size (inches) | Typical Application |
---|---|
6 1/8 | Shallow wells, low production rates |
8 1/2 | Medium-depth wells, moderate production rates |
9 7/8 | Deep wells, high production rates |
12 1/4 | Ultra-deep wells, very high production rates |
These hole sizes are not exhaustive, and there are many other diameters used based on specific well requirements.
Advantages of Larger Production Hole Diameters
Larger production hole diameters offer several advantages:
-
Increased flow rates: Larger hole diameters allow for higher flow rates, as they reduce the pressure losses associated with fluid flow through the wellbore. This can lead to higher production rates and improved well productivity.
-
Improved well accessibility: Larger hole diameters provide better access to the wellbore for intervention and workover operations. This can simplify well maintenance and reduce downtime.
-
Enhanced reservoir drainage: Larger hole diameters can improve reservoir drainage by exposing more of the reservoir rock to the wellbore. This can lead to better resource recovery and increased ultimate recovery.
Disadvantages of Larger Production Hole Diameters
Despite the advantages, larger production hole diameters also have some drawbacks:
-
Higher drilling costs: Drilling larger hole diameters requires more powerful and expensive drilling rigs, as well as increased consumption of drilling fluids and other consumables. This can significantly increase the overall drilling costs.
-
Increased completion costs: Larger hole diameters also require larger and more expensive completion equipment, such as casing, tubing, and packers. This can increase the overall completion costs.
-
Potential for wellbore instability: In some cases, larger hole diameters may increase the risk of wellbore instability, particularly in weak or unconsolidated formations. This can lead to hole collapse, lost circulation, and other drilling problems.
Selecting the Optimal Production Hole Diameter
Selecting the optimal production hole diameter requires careful consideration of various factors, including reservoir characteristics, well depth, production targets, and completion design. The goal is to balance the benefits of larger hole diameters (increased flow rates, improved well accessibility, and enhanced reservoir drainage) with the associated costs and risks (higher drilling and completion costs, potential for wellbore instability).
Simulation and Modeling
One approach to selecting the optimal production hole diameter is through the use of simulation and modeling techniques. Reservoir simulators and wellbore flow models can be used to predict the performance of different hole diameters under various scenarios. These tools allow engineers to evaluate the impact of hole size on production rates, pressure losses, and ultimate recovery, helping them make informed decisions.
Field Experience and Best Practices
In addition to simulation and modeling, field experience and best practices also play a crucial role in selecting the appropriate production hole diameter. Companies often rely on their past experiences and lessons learned from similar wells in the same field or region to guide their decision-making process. Industry best practices, such as those developed by professional organizations like the Society of Petroleum Engineers (SPE), can also provide valuable guidance.
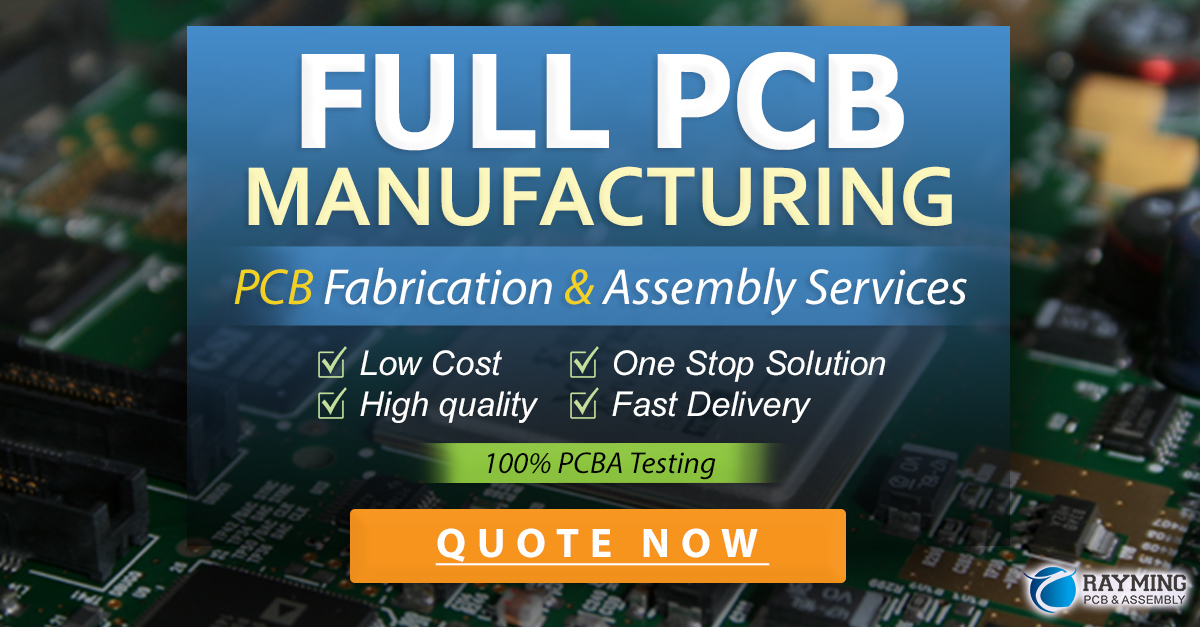
Case Studies
To illustrate the importance of selecting the appropriate production hole diameter, let’s consider a few case studies from the oil and gas industry.
Case Study 1: Shallow Gas Well in the Permian Basin
In this case study, an operator drilled a shallow gas well in the Permian Basin using a 6 1/8-inch production hole diameter. The well had a total depth of 5,000 feet and targeted a conventional sandstone reservoir with moderate permeability.
The 6 1/8-inch hole diameter was selected based on the shallow depth of the well and the moderate production targets. The smaller hole size allowed for faster drilling and reduced overall drilling costs. The well was completed with a single production tubing string and achieved a stable flow rate of 2 million cubic feet per day (MMCFD) of natural gas.
This case study demonstrates how a smaller production hole diameter can be effectively used in shallow wells with moderate production targets to optimize drilling costs and achieve the desired production rates.
Case Study 2: Deep Oil Well in the Gulf of Mexico
In this case study, an operator drilled a deep oil well in the Gulf of Mexico using a 9 7/8-inch production hole diameter. The well had a total depth of 15,000 feet and targeted a high-permeability carbonate reservoir.
The 9 7/8-inch hole diameter was selected based on the deep depth of the well and the high production targets. The larger hole size allowed for higher flow rates and reduced pressure losses, which was critical for achieving the desired production rates in the deep, high-pressure reservoir. The well was completed with dual production tubing strings and achieved a stable flow rate of 10,000 barrels of oil per day (BOPD).
This case study illustrates how a larger production hole diameter can be used in deep wells with high production targets to optimize well productivity and overcome the challenges associated with deep, high-pressure reservoirs.
Frequently Asked Questions (FAQ)
-
What is a production hole?
A production hole is the drilled wellbore that is used to extract hydrocarbons (oil and gas) from underground reservoirs to the surface. -
What factors influence the selection of the production hole diameter?
Several factors influence the selection of the production hole diameter, including reservoir characteristics, well depth, production targets, and completion design. -
What are the advantages of larger production hole diameters?
Larger production hole diameters offer several advantages, such as increased flow rates, improved well accessibility, and enhanced reservoir drainage. -
What are the disadvantages of larger production hole diameters?
Larger production hole diameters also have some drawbacks, including higher drilling and completion costs and the potential for wellbore instability. -
How can operators select the optimal production hole diameter?
Operators can select the optimal production hole diameter through the use of simulation and modeling techniques, as well as by relying on field experience and industry best practices.
Conclusion
The production hole diameter is a critical factor that impacts the productivity, efficiency, and overall performance of oil and gas wells. Selecting the appropriate hole size requires careful consideration of various factors, including reservoir characteristics, well depth, production targets, and completion design.
Larger production hole diameters offer several advantages, such as increased flow rates and improved well accessibility, but also come with higher costs and potential risks. Smaller hole diameters can be effective in shallow wells with moderate production targets, while larger diameters are often necessary for deep, high-pressure reservoirs.
Ultimately, the optimal production hole diameter is one that balances the benefits of larger hole sizes with the associated costs and risks. By using simulation and modeling techniques, relying on field experience, and following industry best practices, operators can make informed decisions that maximize well productivity and profitability.
Leave a Reply