Introduction to Axial Flux BLDC Motors
Axial flux permanent magnet brushless DC (BLDC) motors have gained significant attention in recent years due to their high power density, efficiency, and compact design. Unlike traditional radial flux motors, axial flux motors have their magnetic flux flowing parallel to the rotational axis, resulting in a disc-shaped structure. This unique configuration offers several advantages, making axial flux BLDC motors suitable for various applications, including electric vehicles, robotics, and industrial automation.
Advantages of Axial Flux BLDC Motors
- High power density: The disc-shaped structure of axial flux motors allows for a larger air gap surface area, enabling them to generate higher torque and power output compared to radial flux motors of similar size.
- Compact design: Axial flux motors have a shorter axial length, making them ideal for applications with limited space requirements.
- Efficiency: The use of permanent magnets and optimized magnetic circuits in axial flux motors contributes to their high efficiency, reducing energy losses and improving overall system performance.
- Reduced cogging torque: Axial flux motors typically exhibit lower cogging torque, resulting in smoother operation and better low-speed performance.
Stator Design in Axial Flux BLDC Motors
The stator is a critical component in axial flux BLDC motors, as it plays a crucial role in determining the motor’s performance, efficiency, and reliability. The stator consists of a set of coils or windings arranged in a specific pattern to generate the required magnetic field when energized. In this section, we will discuss the key aspects of stator design in axial flux BLDC motors.
Stator Configurations
There are several stator configurations commonly used in axial flux BLDC motors:
- Single-sided stator: In this configuration, the stator is located on one side of the rotor disc. It is the simplest and most cost-effective design but may suffer from axial forces and reduced power density compared to other configurations.
- Double-sided stator: This configuration features two stators sandwiching the rotor disc. It offers better torque density and balanced axial forces but requires more complex assembly and increased manufacturing costs.
- Multi-stator: Some axial flux motors employ multiple stators and rotors in a stack, further increasing the power density and torque output. However, this configuration adds complexity to the design and assembly process.
Configuration | Advantages | Disadvantages |
---|---|---|
Single-sided stator | Simple, cost-effective | Reduced power density, axial forces |
Double-sided stator | High torque density, balanced axial forces | Complex assembly, increased cost |
Multi-stator | Very high power density | High complexity, difficult assembly |
Winding Arrangements
The winding arrangement in the stator of an axial flux BLDC motor plays a significant role in determining the motor’s performance characteristics. The most common winding arrangements are:
- Concentrated windings: In this arrangement, each coil is wound around a single stator tooth. Concentrated windings offer high torque density, reduced end-winding length, and simplified manufacturing. However, they may exhibit higher torque ripple and increased eddy current losses in the magnets.
- Distributed windings: Distributed windings have coils spanning multiple stator teeth, resulting in a more sinusoidal back-EMF waveform and reduced torque ripple. However, they have longer end-windings and increased copper losses compared to concentrated windings.
The choice between concentrated and distributed windings depends on the specific application requirements, such as torque ripple, efficiency, and manufacturing considerations.
Stator Core Materials
The stator core in axial flux BLDC motors is typically made of soft magnetic materials to provide a low-reluctance path for the magnetic flux. The most common materials used for stator cores are:
- Electrical steel: Laminated electrical steel is widely used due to its high permeability, low core losses, and cost-effectiveness. The laminations are stacked and bonded together to form the stator core.
- Soft magnetic composites (SMCs): SMCs are made of iron powder particles coated with an insulating layer and pressed into a solid core. SMCs offer several advantages, such as isotropic magnetic properties, reduced eddy current losses, and the ability to create complex geometries. However, they have lower permeability and higher cost compared to electrical steel.
- Amorphous and nanocrystalline materials: These advanced materials exhibit excellent magnetic properties, such as high permeability, low core losses, and high saturation flux density. However, their high cost and limited availability currently restrict their widespread use in axial flux motors.
Stator Cooling
Effective cooling of the stator is essential to maintain the motor’s performance and reliability, especially in high-power applications. Several cooling methods can be employed in axial flux BLDC motors:
- Air cooling: Natural or forced air convection can be used to dissipate heat from the stator surface. Fins or heat sinks can be added to enhance heat transfer.
- Liquid cooling: In more demanding applications, liquid cooling can be implemented by circulating a coolant through channels or jackets in the stator housing. This provides more efficient heat removal and allows for higher power densities.
- Direct winding cooling: In some cases, the windings themselves can be directly cooled by passing a coolant through hollow conductors or by immersing the windings in a cooling fluid.
The choice of cooling method depends on the specific application, power level, and operating environment of the axial flux BLDC motor.
Stator Manufacturing and Assembly
The manufacturing and assembly processes for Axial Flux BLDC Stators involve several key steps to ensure high quality and performance. These steps include:
- Lamination stamping: For stators made of electrical steel, the laminations are punched or laser-cut from steel sheets to the desired shape and size.
- Stacking and bonding: The laminations are stacked and bonded together using adhesives or welding techniques to form the stator core.
- Winding: The coils are wound around the stator teeth or slots using manual or automated winding machines. The winding process must ensure proper insulation, tight packing, and minimal end-winding length.
- Insulation and impregnation: The wound stator is insulated using materials such as enamel, resin, or varnish to provide electrical insulation and mechanical protection. Vacuum impregnation can be used to fill the voids and improve heat transfer.
- Assembly: The stator is assembled with the rotor and other motor components, such as bearings and housing, to form the complete axial flux BLDC motor.
Advanced manufacturing techniques, such as 3D printing and additive manufacturing, are being explored for the production of axial flux motor components, including stators. These techniques offer the potential for rapid prototyping, customization, and the creation of complex geometries.
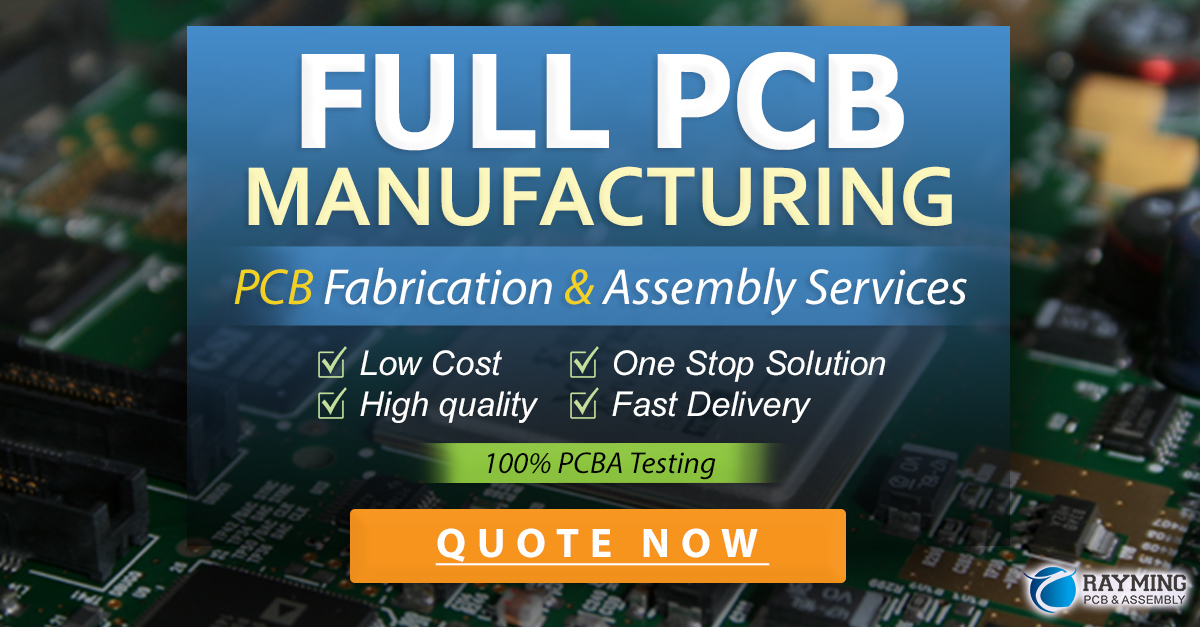
Stator Optimization Techniques
Optimizing the stator design is crucial for achieving high performance, efficiency, and cost-effectiveness in axial flux BLDC motors. Several optimization techniques can be applied to enhance the stator’s performance:
- Finite element analysis (FEA): FEA is a powerful tool for simulating and analyzing the electromagnetic, thermal, and mechanical behavior of the stator. It allows designers to evaluate different stator configurations, winding arrangements, and materials to optimize the motor’s performance.
- Topology optimization: Topology optimization involves modifying the shape and distribution of the stator core material to minimize weight, reduce losses, and improve magnetic flux paths. This technique can lead to novel stator designs with improved performance characteristics.
- Multi-objective optimization: In many cases, stator design involves trade-offs between multiple objectives, such as torque density, efficiency, and cost. Multi-objective optimization algorithms can be used to find the best compromise solution that satisfies the desired performance criteria.
- Design of experiments (DOE): DOE is a systematic approach to investigating the relationship between design parameters and motor performance. By conducting a series of experiments with different parameter combinations, designers can identify the most influential factors and optimize the stator design accordingly.
These optimization techniques, combined with advanced materials and manufacturing processes, enable the development of high-performance axial flux BLDC stators that meet the demanding requirements of modern applications.
Challenges and Future Trends
Despite the numerous advantages of axial flux BLDC motors, there are still challenges and opportunities for further development in stator design and manufacturing. Some of the key challenges include:
- High-speed operation: Axial flux motors designed for high-speed applications face challenges related to mechanical stress, rotor dynamics, and losses. Advanced materials and optimized stator designs are required to address these issues.
- Thermal management: As power densities increase, effective thermal management becomes critical. Novel cooling techniques and materials with high thermal conductivity need to be developed to ensure reliable operation.
- Manufacturing complexity: The disc-shaped structure and unique geometry of axial flux stators can pose manufacturing challenges, especially for large-scale production. Advancements in manufacturing processes and automation are necessary to improve efficiency and reduce costs.
Future trends in axial flux BLDC stator design and manufacturing include:
- Advanced materials: The development of new soft magnetic materials, such as amorphous and nanocrystalline alloys, and high-temperature insulation materials will enable higher power densities and improved efficiency.
- Additive manufacturing: 3D printing and other additive manufacturing techniques have the potential to revolutionize stator production, allowing for complex geometries, customization, and reduced material waste.
- Integrated cooling: The integration of cooling channels or heat pipes directly into the stator structure can enhance heat dissipation and enable higher power densities.
- Multiphysics optimization: The simultaneous optimization of electromagnetic, thermal, and mechanical aspects of the stator design using advanced simulation tools will lead to more efficient and reliable motors.
As research and development in these areas continue, axial flux BLDC motors are poised to become increasingly competitive and widely adopted in various industries, driving innovation and performance improvements in electric propulsion and automation systems.
Frequently Asked Questions (FAQ)
- What is the main difference between axial flux and radial flux BLDC motors?
-
The main difference lies in the direction of the magnetic flux. In axial flux motors, the magnetic flux flows parallel to the rotational axis, resulting in a disc-shaped structure. In radial flux motors, the magnetic flux flows radially, perpendicular to the rotational axis, resulting in a cylindrical structure.
-
What are the advantages of axial flux BLDC motors over radial flux motors?
-
Axial flux BLDC motors offer several advantages, including high power density, compact design, high efficiency, and reduced cogging torque. They are particularly suitable for applications with limited space requirements and high torque demands.
-
What are the most common stator configurations in axial flux BLDC motors?
-
The most common stator configurations are single-sided stator, double-sided stator, and multi-stator. Single-sided stators are simple and cost-effective, double-sided stators offer high torque density and balanced axial forces, and multi-stator configurations provide very high power density.
-
What are the differences between concentrated and distributed windings in axial flux BLDC stators?
-
Concentrated windings have each coil wound around a single stator tooth, offering high torque density and simplified manufacturing. Distributed windings have coils spanning multiple stator teeth, resulting in a more sinusoidal back-EMF waveform and reduced torque ripple.
-
What are the challenges and future trends in axial flux BLDC stator design and manufacturing?
- Challenges include high-speed operation, thermal management, and manufacturing complexity. Future trends involve the development of advanced materials, additive manufacturing techniques, integrated cooling solutions, and multiphysics optimization approaches to enhance the performance and reliability of axial flux BLDC motors.
Leave a Reply