Introduction to PCB Component Placement
Printed Circuit Board (PCB) layout is a critical step in the design process of electronic devices. Proper component placement on the PCB can greatly impact the performance, reliability, and manufacturability of the final product. In this comprehensive guide, we will explore the key aspects of PCB component placement and provide valuable insights to help you optimize your PCB layouts.
Understanding the Importance of PCB Component Placement
The Role of Component Placement in PCB Design
Component placement is a fundamental aspect of PCB design that involves strategically positioning electronic components on the board. The primary goals of component placement are to:
– Minimize the overall size of the PCB
– Reduce signal interference and crosstalk
– Improve heat dissipation
– Enhance manufacturability and assembly efficiency
The Impact of Poor Component Placement
Improper component placement can lead to various issues, including:
– Signal integrity problems
– Increased electromagnetic interference (EMI)
– Thermal management challenges
– Difficulties in manufacturing and assembly
– Reduced reliability and longevity of the final product
Key Considerations for PCB Component Placement
Board Size and Shape
The size and shape of the PCB play a significant role in component placement. Consider the following factors:
– Available space for component placement
– Clearance requirements for connectors and mounting holes
– Mechanical constraints of the enclosure or housing
Component Footprint and Package Type
Different components come in various footprints and package types. When placing components, consider:
– Footprint dimensions and pad sizes
– Orientation and alignment of components
– Compatibility with automated assembly processes
Signal Integrity and EMI
Proper component placement is essential for maintaining signal integrity and minimizing electromagnetic interference (EMI). Keep in mind:
– Critical signal paths and their routing requirements
– Separation of analog and digital components
– Placement of decoupling capacitors close to power pins
– Shielding and grounding techniques
Thermal Management
Effective thermal management is crucial for the reliable operation of electronic components. Consider the following:
– Placement of heat-generating components away from temperature-sensitive devices
– Adequate spacing between components for heat dissipation
– Use of thermal vias and heat sinks when necessary
Manufacturing and Assembly
Component placement should also take into account manufacturing and assembly considerations, such as:
– Orientation and alignment of components for automated pick-and-place machines
– Accessibility for manual soldering or rework
– Clearance for testing and inspection points
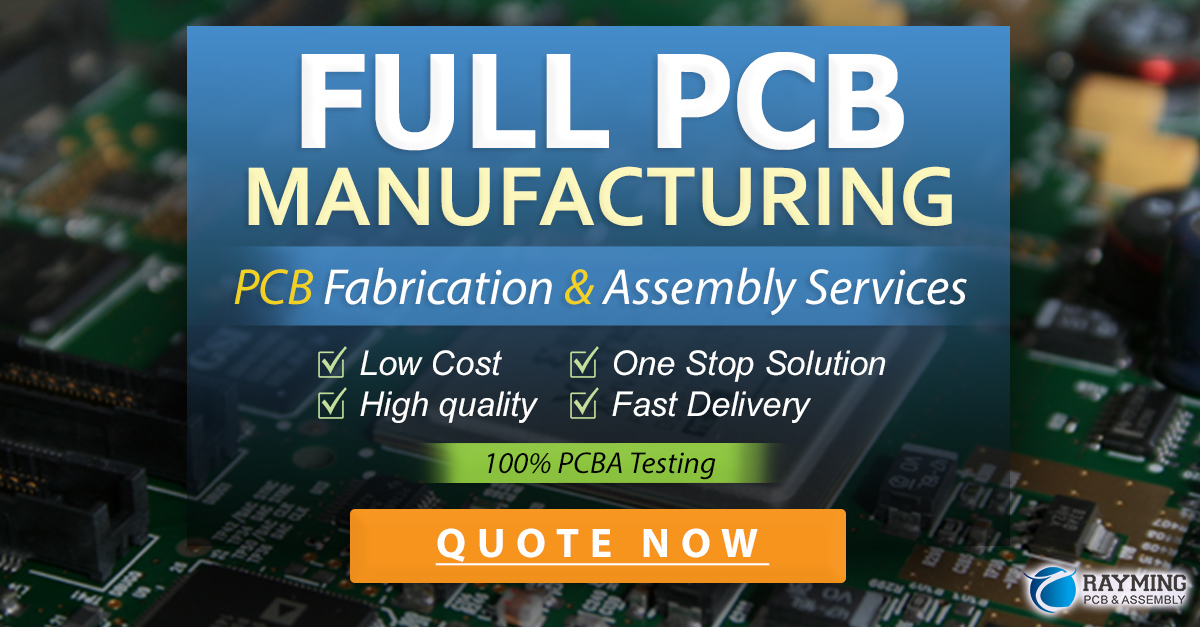
Best Practices for PCB Component Placement
Grouping Related Components
Group related components together based on their functionality or signal paths. This approach helps in:
– Reducing the length of signal traces
– Minimizing crosstalk and signal interference
– Improving the overall organization and readability of the layout
Placing Power and Ground Components
Power and ground components, such as Voltage Regulators and decoupling capacitors, should be placed strategically:
– Place voltage regulators close to the power input
– Locate decoupling capacitors near the power pins of ICs
– Use a star or distributed power and ground network for better noise immunity
Optimizing Component Orientation
Orient components in a way that optimizes routing and minimizes the number of vias. Consider:
– Aligning components in the same direction for easier routing
– Placing components with similar heights on the same side of the board
– Orienting connectors and headers for easy access and cable management
Routing Considerations
When placing components, keep routing considerations in mind:
– Avoid crossing signal traces whenever possible
– Maintain proper trace width and spacing based on signal requirements
– Use vias judiciously to minimize signal integrity issues
– Consider the use of buried or blind vias for dense layouts
Utilizing PCB Design Software
Modern PCB design software tools offer powerful features to aid in component placement:
– Automated component placement algorithms
– Design rule checks (DRC) to ensure compliance with manufacturing constraints
– 3D visualization and collision detection
– Real-time feedback on signal integrity and EMI performance
PCB Component Placement Techniques
Manual Placement
Manual placement involves placing components on the PCB layout by hand. This approach allows for fine-grained control over component positioning but can be time-consuming for complex designs.
Automatic Placement
Automatic placement utilizes algorithms within PCB design software to place components based on predefined rules and constraints. This technique can significantly speed up the placement process, especially for large and complex designs.
Hybrid Placement
Hybrid placement combines manual and automatic placement techniques. Designers can manually place critical components and let the software automatically place the remaining components based on specified rules and constraints.
Common Pitfalls to Avoid in PCB Component Placement
- Overcrowding components, leading to manufacturing and assembly challenges
- Neglecting thermal management considerations
- Ignoring signal integrity and EMI requirements
- Placing components too close to board edges or mounting holes
- Failing to consider the accessibility of test points and debugging interfaces
Conclusion
PCB component placement is a critical aspect of PCB design that directly impacts the performance, reliability, and manufacturability of electronic devices. By understanding the key considerations and best practices outlined in this guide, you can optimize your PCB layouts for success. Remember to prioritize signal integrity, thermal management, and manufacturing feasibility throughout the placement process. Utilize PCB design software tools to streamline your workflow and ensure compliance with design rules and constraints.
At RAYPCB, we understand the importance of proper PCB component placement. Our experienced team of PCB design experts is dedicated to helping you achieve optimal layouts that meet your specific requirements. Whether you need assistance with manual placement, automatic placement, or a hybrid approach, we have the knowledge and tools to support your project.
Don’t let poor component placement compromise the quality and reliability of your electronic devices. Partner with RAYPCB for your PCB design needs and benefit from our expertise in creating high-performance, manufacturable PCB layouts. Contact us today to discuss your project and take your PCB designs to the next level.
Frequently Asked Questions (FAQ)
1. What is PCB component placement?
PCB component placement refers to the process of strategically positioning electronic components on a printed circuit board (PCB) layout. It involves considering factors such as board size, component footprint, signal integrity, thermal management, and manufacturing feasibility to optimize the overall performance and reliability of the PCB.
2. Why is proper component placement important in PCB design?
Proper component placement is crucial in PCB design for several reasons:
– It minimizes the overall size of the PCB, reducing material costs and space requirements.
– It reduces signal interference and crosstalk, ensuring the integrity of the electrical signals.
– It improves heat dissipation, preventing components from overheating and extending their lifespan.
– It enhances manufacturability and assembly efficiency, reducing production time and costs.
3. What are some key considerations for PCB component placement?
When placing components on a PCB, consider the following key factors:
– Board size and shape: Ensure components fit within the available space and meet clearance requirements.
– Component footprint and package type: Select appropriate footprints and consider compatibility with assembly processes.
– Signal integrity and EMI: Separate analog and digital components, place decoupling capacitors close to power pins, and implement shielding and grounding techniques.
– Thermal management: Position heat-generating components away from temperature-sensitive devices and provide adequate spacing for heat dissipation.
– Manufacturing and assembly: Orient components for automated pick-and-place machines and ensure accessibility for manual soldering or rework.
4. What are some best practices for PCB component placement?
Some best practices for PCB component placement include:
– Grouping related components based on functionality or signal paths to reduce trace lengths and minimize crosstalk.
– Placing power and ground components strategically, such as locating voltage regulators close to the power input and decoupling capacitors near IC power pins.
– Optimizing component orientation to simplify routing and minimize the number of vias.
– Considering routing requirements, such as avoiding crossing signal traces and maintaining proper trace width and spacing.
– Utilizing PCB design software tools for automated placement, design rule checks, and 3D visualization.
5. How can RAYPCB assist with PCB component placement?
RAYPCB offers expert PCB design services, including assistance with component placement. Our experienced team can help you:
– Optimize component placement for signal integrity, thermal management, and manufacturability.
– Utilize advanced PCB design software tools for automated placement and design rule checks.
– Provide guidance on best practices and industry standards for component placement.
– Collaborate with you to create high-performance, reliable PCB layouts that meet your specific requirements.
Contact RAYPCB today to leverage our expertise in PCB component placement and take your PCB designs to the next level.
Aspect | Considerations |
---|---|
Board Size and Shape | – Available space for component placement – Clearance requirements for connectors and mounting holes |
Component Footprint | – Footprint dimensions and pad sizes – Orientation and alignment of components |
Signal Integrity | – Critical signal paths and routing requirements – Separation of analog and digital components |
Thermal Management | – Placement of heat-generating components – Adequate spacing for heat dissipation |
Manufacturing | – Orientation and alignment for automated assembly – Accessibility for manual soldering or rework |
Leave a Reply