What is Automated Optical Inspection?
Automated Optical Inspection is a non-contact, visual inspection method that uses cameras, lighting systems, and image processing software to automatically detect and classify defects in manufactured products. AOI systems capture high-resolution images of the product and compare them to a predefined set of criteria or a “golden sample” to identify any deviations or anomalies.
AOI is commonly used in the electronics industry for inspecting printed circuit boards (PCBs), semiconductor wafers, and other electronic components. However, its applications extend to various other industries, such as automotive, pharmaceutical, and packaging.
Key Components of an AOI System
A typical AOI system consists of the following key components:
-
Cameras: High-resolution digital cameras capture images of the product being inspected. The number and type of cameras used depend on the application and the level of detail required.
-
Lighting: Proper lighting is essential for capturing clear and consistent images. AOI systems often employ multiple lighting techniques, such as diffuse, directional, or structured lighting, to highlight specific features or defects.
-
Image Processing Software: Sophisticated software algorithms analyze the captured images, comparing them to a reference model or a set of predefined rules. The software identifies and classifies defects based on various parameters, such as size, shape, color, and location.
-
Conveyor System: A conveyor system moves the products through the AOI machine, ensuring consistent positioning and orientation for accurate inspection.
-
User Interface: A user-friendly interface allows operators to set up inspection parameters, monitor the process, and review the results.
Benefits of Automated Optical Inspection
Implementing AOI in manufacturing processes offers several significant benefits:
-
Improved Quality: AOI systems can detect defects that are difficult or impossible to identify with manual inspection methods, resulting in higher product quality and fewer customer returns.
-
Increased Efficiency: Automated Inspection is much faster than manual inspection, allowing for higher throughput and reduced production time.
-
Cost Reduction: By identifying defects early in the manufacturing process, AOI helps reduce scrap, rework, and warranty costs.
-
Consistency: AOI systems provide consistent and objective inspection results, eliminating human error and subjectivity.
-
Traceability: AOI data can be stored and analyzed to identify trends, root causes of defects, and opportunities for process improvement.
Applications of Automated Optical Inspection
AOI is used in various industries and applications, including:
Electronics Industry
In the electronics industry, AOI is primarily used for inspecting PCBs at different stages of the manufacturing process, such as:
- Bare Board inspection: Checking for defects in the PCB substrate, such as shorts, opens, and incorrect trace widths.
- Solder paste inspection (SPI): Verifying the proper application of solder paste before component placement.
- Pre-reflow inspection: Checking component placement accuracy and orientation before soldering.
- Post-reflow inspection: Detecting soldering defects, such as bridges, insufficient solder, and tombstoning.
AOI is also used for inspecting semiconductor wafers, detecting defects such as particles, scratches, and pattern irregularities.
Automotive Industry
In the automotive industry, AOI is used for inspecting various components and assemblies, such as:
- Connectors and wiring harnesses
- Printed circuit boards for electronic control units (ECUs)
- Surface finish and coating quality
- Dimensional accuracy of machined parts
Pharmaceutical Industry
AOI is used in the pharmaceutical industry for:
- Inspecting the quality and integrity of packaging, such as blister packs and vials
- Verifying the presence and correctness of labels and printed information
- Checking the color, shape, and size of tablets and capsules
Packaging Industry
In the packaging industry, AOI is used for:
- Inspecting the quality of printed materials, such as labels and cartons
- Verifying the proper placement and alignment of packaging components
- Checking for seal integrity and leaks in flexible packaging
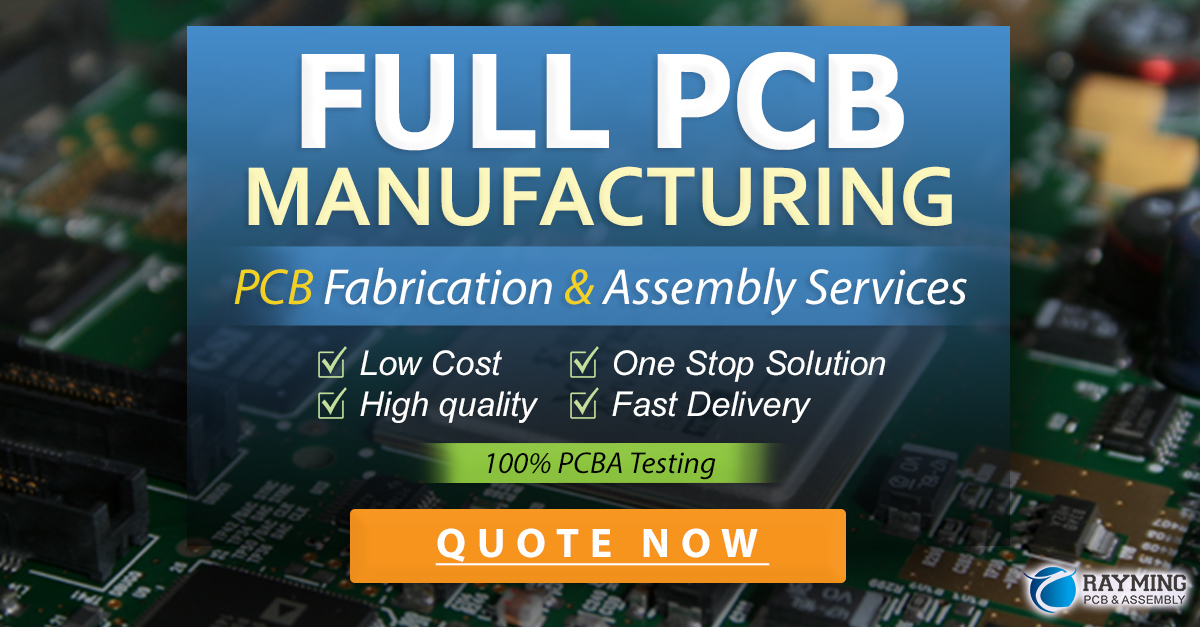
Advantages of AOI over Manual Inspection
Automated Optical Inspection offers several advantages over traditional manual inspection methods:
-
Speed: AOI systems can inspect products at a much higher rate than human inspectors, enabling faster production times and higher throughput.
-
Accuracy: AOI systems can detect defects that are too small or subtle for human inspectors to identify consistently, resulting in higher inspection accuracy.
-
Consistency: AOI provides consistent and objective inspection results, eliminating the variability inherent in manual inspection due to factors such as fatigue, distraction, and subjectivity.
-
Scalability: AOI systems can be easily scaled up to accommodate higher production volumes or multiple product lines, without the need for additional human inspectors.
-
Data Collection: AOI systems generate valuable data that can be used for process analysis, quality control, and continuous improvement initiatives.
Challenges and Limitations of AOI
Despite its many benefits, AOI also has some challenges and limitations:
-
Initial Investment: Implementing an AOI system can require a significant upfront investment in equipment, software, and training.
-
Programming Complexity: Developing and maintaining inspection programs for complex products can be time-consuming and require specialized expertise.
-
False Positives and False Negatives: AOI systems can sometimes generate false alarms (false positives) or miss actual defects (false negatives), requiring manual verification and fine-tuning of inspection parameters.
-
Limited Depth Perception: Most AOI systems rely on 2D imaging, which can limit their ability to detect certain types of defects, such as those related to component height or solder joint volume.
Future Trends in Automated Optical Inspection
As technology advances, AOI systems are becoming more sophisticated and capable. Some of the key trends shaping the future of AOI include:
-
3D AOI: The integration of 3D imaging technologies, such as structured light or laser scanning, allows AOI systems to capture height and volume information, enabling the detection of a wider range of defects.
-
AI and Machine Learning: The application of artificial intelligence (AI) and machine learning algorithms can enhance the accuracy and adaptability of AOI systems, enabling them to learn from past data and improve their defect detection capabilities over time.
-
Inline AOI: Integrating AOI systems directly into the production line, rather than using them as standalone stations, allows for real-time inspection and feedback, enabling faster identification and correction of defects.
-
Multi-modal Inspection: Combining AOI with other inspection technologies, such as X-ray or thermal imaging, can provide a more comprehensive view of the product and help detect defects that may be invisible to optical inspection alone.
-
Cloud-based AOI: The development of cloud-based AOI solutions allows for centralized data storage, remote access, and collaborative analysis, enabling better data utilization and knowledge sharing across multiple production sites.
Frequently Asked Questions (FAQ)
-
What is the difference between AOI and visual inspection?
AOI is an automated process that uses cameras, lighting, and image processing software to detect defects, while visual inspection relies on human inspectors to manually examine products for defects. -
Can AOI completely replace manual inspection?
While AOI can significantly reduce the need for manual inspection, it may not completely replace it in all cases. Some products may require additional manual inspection to verify certain aspects or to confirm the results of the AOI system. -
How does AOI handle reflective or transparent surfaces?
Inspecting reflective or transparent surfaces can be challenging for AOI systems. Special lighting techniques, such as polarized or diffuse lighting, can be used to minimize reflections and glare. Alternatively, advanced image processing algorithms can be employed to compensate for these effects. -
What factors influence the accuracy of an AOI system?
The accuracy of an AOI system depends on several factors, including the quality and resolution of the cameras, the effectiveness of the lighting setup, the robustness of the image processing algorithms, and the proper calibration and programming of the system for the specific product being inspected. -
How often should an AOI system be recalibrated?
The frequency of recalibration depends on the specific application and the stability of the production environment. In general, AOI systems should be recalibrated whenever there are significant changes in the product design, manufacturing process, or environmental conditions. Regular preventive maintenance and calibration checks can help ensure consistent performance over time.
Conclusion
Automated Optical Inspection has become an indispensable tool in modern manufacturing, enabling companies to achieve higher product quality, efficiency, and cost-effectiveness. As industries continue to embrace automation and digitalization, the adoption of AOI is expected to grow further, driven by advancements in imaging technology, artificial intelligence, and data analytics.
By understanding the principles, applications, and benefits of AOI, manufacturers can make informed decisions on how to implement this technology in their processes and harness its potential for continuous improvement and competitive advantage.
Industry | AOI Applications |
---|---|
Electronics | PCB Inspection (bare board, SPI, pre-reflow, post-reflow), semiconductor wafer inspection |
Automotive | Connector and wiring harness inspection, PCB inspection for ECUs, surface finish and coating inspection, dimensional accuracy of machined parts |
Pharmaceutical | Packaging quality and integrity inspection, label and print verification, tablet and capsule inspection |
Packaging | Print quality inspection, packaging component placement and alignment, seal integrity and leak detection |
As AOI technology continues to evolve, it is crucial for manufacturers to stay up-to-date with the latest developments and best practices in order to fully leverage the benefits of automated inspection and maintain a competitive edge in their respective industries.
Leave a Reply