Introduction to PCB Imaging
Printed Circuit Board (PCB) imaging is a crucial step in the manufacturing process of electronic devices. It involves transferring the designed circuit pattern onto the copper-clad laminate, which serves as the foundation for the PCB. Various methods are employed for PCB imaging, with dry film imaging being one of the most widely used techniques in the industry.
Dry film imaging offers several advantages over other imaging methods, such as liquid photoresist and screen printing. It provides high resolution, excellent uniformity, and improved adhesion to the copper surface. Additionally, dry film imaging is a cost-effective and efficient process, making it suitable for high-volume production.
In this article, we will delve into the details of dry film imaging for PCBs, covering its process, advantages, and best practices. We will also discuss the role of PCB imaging in the overall manufacturing process and its significance in ensuring the quality and reliability of the final product.
The Dry Film Imaging Process
Step 1: Surface Preparation
Before applying the dry film, the copper-clad laminate must undergo surface preparation to ensure proper adhesion and minimize defects. The surface is cleaned using a chemical solution to remove any contaminants, such as oils, dust, or oxidation. This step is critical for achieving a uniform and defect-free image.
Step 2: Lamination
The dry film, which consists of a photosensitive polymer layer sandwiched between a polyester cover sheet and a protective polyethylene sheet, is laminated onto the copper surface using a laminator. The lamination process involves applying heat and pressure to ensure that the dry film adheres firmly to the copper.
The lamination temperature, pressure, and speed must be carefully controlled to achieve optimal results. Typical lamination conditions for dry film are:
Parameter | Value |
---|---|
Temperature | 100-120°C |
Pressure | 2-4 kg/cm² |
Speed | 1-3 m/min |
Step 3: Exposure
After lamination, the PCB is exposed to ultraviolet (UV) light through a photomask, which contains the desired circuit pattern. The UV light causes the exposed areas of the dry film to undergo a chemical change, making them insoluble in the developer solution.
The exposure time and intensity must be carefully controlled to ensure proper polymerization of the exposed areas. Overexposure can lead to loss of fine features, while underexposure can result in incomplete polymerization and poor adhesion.
Step 4: Development
Following exposure, the PCB is immersed in a developer solution, which dissolves the unexposed areas of the dry film, revealing the desired circuit pattern on the copper surface. The development process is typically carried out in a conveyor-type developer machine, which ensures uniform development across the entire PCB surface.
The development time and temperature must be optimized to achieve complete removal of the unexposed areas without damaging the polymerized image. Typical development conditions for dry film are:
Parameter | Value |
---|---|
Temperature | 25-35°C |
Time | 1-3 minutes |
Step 5: Etching
After development, the PCB undergoes etching to remove the unwanted copper areas, leaving behind the desired circuit pattern. The dry film acts as an etch resist, protecting the copper underneath from the etching solution.
The etching process can be carried out using various methods, such as:
- Cupric chloride etching
- Ammoniacal etching
- Alkaline etching
The choice of etching method depends on factors such as the copper thickness, circuit complexity, and environmental considerations.
Step 6: Stripping
Once etching is complete, the remaining dry film is stripped off the PCB surface using a stripping solution. This step reveals the final circuit pattern on the copper surface, ready for subsequent processing steps, such as drilling, plating, and solder mask application.
Advantages of Dry Film Imaging
Dry film imaging offers several advantages over other PCB imaging methods:
-
High Resolution: Dry film imaging can achieve feature sizes as small as 50 microns, making it suitable for high-density PCB designs.
-
Excellent Uniformity: The dry film provides a uniform coating thickness across the entire PCB surface, ensuring consistent imaging quality.
-
Improved Adhesion: The lamination process ensures strong adhesion between the dry film and the copper surface, minimizing the risk of defects during subsequent processing steps.
-
Cost-Effective: Dry film imaging is a cost-effective process, especially for high-volume production, as it minimizes material waste and reduces labor costs compared to liquid photoresist methods.
-
Environmental Friendliness: Dry film imaging generates less chemical waste compared to liquid photoresist methods, making it a more environmentally friendly option.
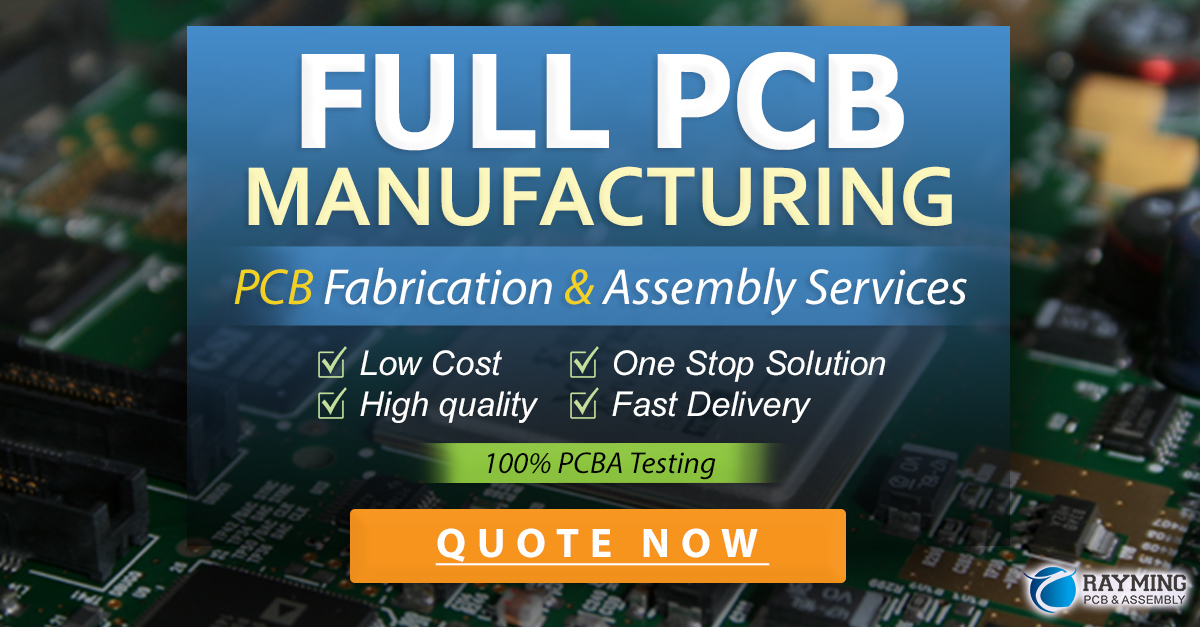
Best Practices for Dry Film Imaging
To ensure optimal results and minimize defects, consider the following best practices when using dry film imaging for PCBs:
-
Maintain a Clean Environment: Conduct the imaging process in a clean room environment to minimize the risk of contamination and ensure consistent results.
-
Control Lamination Parameters: Optimize the lamination temperature, pressure, and speed to achieve proper adhesion and minimize the risk of defects, such as air bubbles or wrinkles.
-
Monitor Exposure Conditions: Regularly monitor and calibrate the exposure equipment to ensure consistent exposure intensity and time, minimizing the risk of overexposure or underexposure.
-
Optimize Development Parameters: Fine-tune the development time and temperature to achieve complete removal of the unexposed areas without damaging the polymerized image.
-
Implement Quality Control Measures: Conduct regular quality inspections throughout the imaging process to identify and correct any issues promptly, ensuring the production of high-quality PCBs.
FAQ
-
What is dry film imaging, and how does it differ from other PCB imaging methods?
Dry film imaging is a method of transferring the desired circuit pattern onto the copper-clad laminate using a photosensitive dry film. It differs from other methods, such as liquid photoresist and screen printing, in terms of its high resolution, excellent uniformity, and improved adhesion to the copper surface. -
What are the main steps involved in the dry film imaging process?
The main steps in the dry film imaging process are: - Surface preparation
- Lamination
- Exposure
- Development
- Etching
-
Stripping
-
What are the advantages of using dry film imaging for PCBs?
The advantages of dry film imaging include high resolution, excellent uniformity, improved adhesion, cost-effectiveness, and environmental friendliness compared to other imaging methods. -
What are the typical feature sizes that can be achieved with dry film imaging?
Dry film imaging can achieve feature sizes as small as 50 microns, making it suitable for high-density PCB designs. -
What are some best practices for ensuring optimal results with dry film imaging?
Some best practices for dry film imaging include maintaining a clean environment, controlling lamination parameters, monitoring exposure conditions, optimizing development parameters, and implementing quality control measures throughout the process.
Conclusion
Dry film imaging is a widely used and reliable method for transferring the desired circuit pattern onto PCBs. By understanding the process, advantages, and best practices associated with dry film imaging, manufacturers can ensure the production of high-quality PCBs with consistent results.
As the electronics industry continues to evolve, with increasing demands for smaller, more complex, and high-performance devices, the importance of accurate and efficient PCB imaging methods will only grow. Dry film imaging, with its numerous benefits, is well-positioned to meet these challenges and contribute to the advancement of PCB manufacturing technology.
Leave a Reply