Introduction to PCB drilling and the Need for Speed Control
Printed Circuit Boards (PCBs) are essential components in modern electronics. They provide a platform for mounting and interconnecting electronic components to create functional circuits. One critical aspect of PCB manufacturing is drilling holes for through-hole components, vias, and mounting purposes. The drilling process needs to be precise, efficient, and well-controlled to ensure the quality and reliability of the final product.
PCB drilling is typically performed using high-speed spindle motors equipped with small drill bits. The speed at which the drill bit rotates, known as the spindle speed, is a crucial parameter that affects the drilling process’s quality and efficiency. Inappropriate spindle speeds can lead to issues such as drill bit breakage, hole misalignment, and poor hole quality.
To address these challenges, implementing proper speed control techniques for PCB drills is essential. Speed control allows for optimizing the drilling process based on factors such as the material being drilled, hole size, and drill bit characteristics. By dynamically adjusting the spindle speed, manufacturers can achieve better hole quality, increased productivity, and reduced tool wear.
In this article, we will delve into the concept of speed control for PCB drills, exploring its importance, various techniques, and best practices. We will also discuss the benefits of implementing speed control in PCB manufacturing and address commonly asked questions related to this topic.
Factors Influencing Drill Speed Selection
Several factors need to be considered when selecting the appropriate drill speed for PCB drilling. These factors include:
Material Properties
The material properties of the PCB substrate play a significant role in determining the optimal drill speed. Different materials, such as FR-4, high-Tg laminates, or metal-backed substrates, have varying hardness, thermal conductivity, and machinability. The drill speed needs to be adjusted based on the material’s characteristics to ensure clean, burr-free holes and minimize heat generation.
Hole Size and Aspect Ratio
The size of the holes being drilled and their aspect ratio (the ratio of hole depth to diameter) also influence the choice of drill speed. Smaller holes typically require higher spindle speeds to achieve clean, precise drilling. However, as the aspect ratio increases, the drill speed may need to be reduced to prevent drill bit breakage and ensure hole quality.
Drill Bit Characteristics
The type and quality of the drill bits used impact the selection of drill speed. Carbide drill bits, for example, can withstand higher spindle speeds compared to high-speed steel (HSS) drill bits. The flute design, point angle, and coating of the drill bits also affect their performance and the optimal speed range.
Desired Productivity and Cycle Time
The desired productivity and cycle time of the PCB drilling process are other factors to consider when selecting drill speeds. Higher spindle speeds generally lead to faster drilling and shorter cycle times. However, pushing the speeds too high can compromise hole quality and increase the risk of drill bit breakage, ultimately impacting overall productivity.
Techniques for Drill Speed Control
Several techniques can be employed to control the speed of PCB drills effectively. These techniques aim to optimize the drilling process, improve hole quality, and extend drill bit life. Let’s explore some common speed control techniques:
Constant Speed Drilling
Constant speed drilling is a basic technique where the spindle speed remains fixed throughout the drilling process. The speed is selected based on the material, hole size, and drill bit characteristics. While simple to implement, constant speed drilling may not always provide the best results, especially when dealing with varying hole sizes or complex PCB designs.
Programmable Speed Drilling
Programmable speed drilling allows for setting different spindle speeds for different hole sizes or layers within the same PCB. This technique enables optimization of the drilling process based on specific requirements. Programmable speed drilling can be achieved using CNC machines or dedicated drilling equipment with speed control capabilities.
Adaptive Speed Drilling
Adaptive speed drilling is an advanced technique that dynamically adjusts the spindle speed based on real-time feedback from the drilling process. Sensors or monitoring systems are used to detect factors such as drill bit wear, material hardness, or vibration levels. The speed is then automatically adjusted to maintain optimal drilling conditions. Adaptive speed drilling helps maximize drill bit life, improve hole quality, and reduce the risk of drill bit breakage.
Peck Drilling
Peck drilling is a technique commonly used for drilling deep holes or materials prone to chip evacuation issues. In peck drilling, the drill bit is periodically retracted from the hole to clear chips and cool down. The speed and depth of each “peck” can be controlled to optimize the drilling process. Peck drilling helps prevent drill bit breakage, reduces heat buildup, and improves hole quality in challenging drilling scenarios.
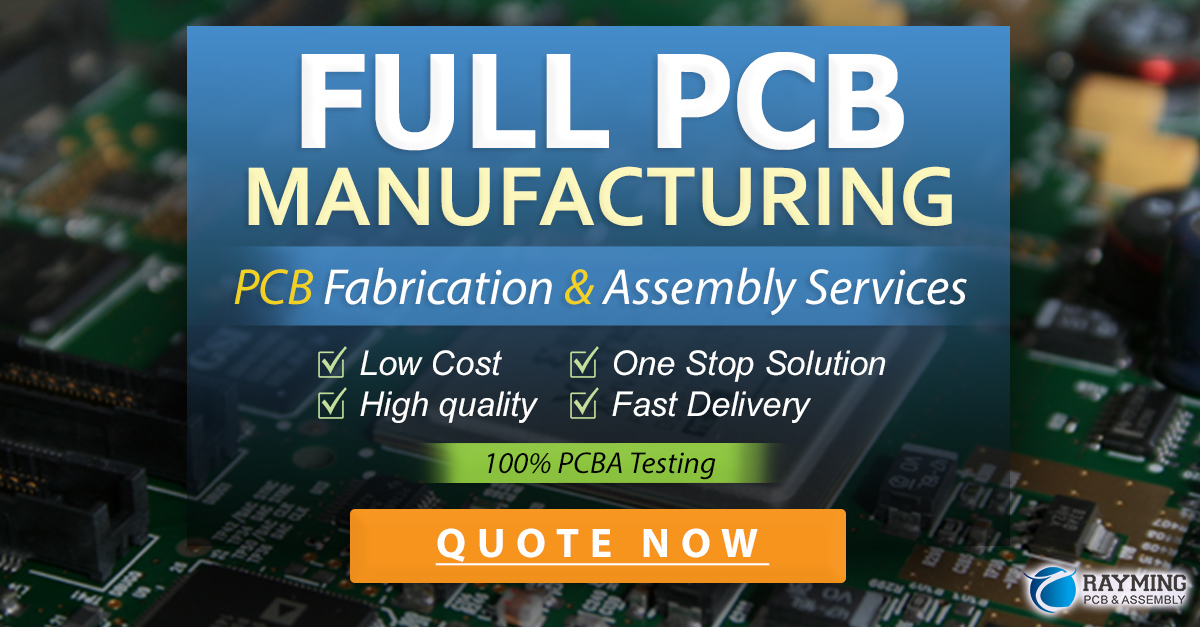
Best Practices for Implementing Drill Speed Control
To effectively implement drill speed control in PCB manufacturing, consider the following best practices:
Establish a Drilling Database
Create a comprehensive drilling database that includes recommended speeds and feeds for different materials, hole sizes, and drill bit types. This database should be based on empirical data, manufacturer recommendations, and experience gained through testing and optimization.
Conduct Pilot Tests
Before implementing speed control techniques in full-scale production, conduct pilot tests to validate the chosen parameters. Pilot testing allows for fine-tuning the speed settings, evaluating hole quality, and identifying any potential issues.
Monitor and Analyze Drilling Performance
Regularly monitor and analyze the drilling performance to identify any deviations or areas for improvement. Collect data on drill bit life, hole quality, and cycle times to make informed decisions about speed control settings and process optimization.
Implement Regular Maintenance and Calibration
Ensure that the drilling equipment, including spindle motors and speed control systems, undergoes regular maintenance and calibration. Proper maintenance helps maintain the accuracy and reliability of speed control, leading to consistent drilling results.
Train Operators and Promote Best Practices
Train machine operators on the importance of speed control and the best practices for implementing it. Encourage operators to follow established guidelines, monitor drilling performance, and report any issues promptly. Foster a culture of continuous improvement and knowledge sharing among the team.
Benefits of Implementing Speed Control for PCB Drills
Implementing speed control techniques in PCB drilling offers several benefits, including:
Improved Hole Quality
By optimizing the spindle speed based on material properties, hole size, and drill bit characteristics, speed control helps achieve better hole quality. It minimizes issues such as burrs, smearing, and delamination, resulting in cleaner and more precise holes.
Increased Drill Bit Life
Proper speed control reduces the stress and heat generation on the drill bits, leading to extended tool life. By avoiding excessive speeds and implementing techniques like peck drilling, manufacturers can significantly increase the number of holes drilled per bit, reducing tooling costs.
Enhanced Productivity
Speed control techniques help optimize the drilling process, reducing cycle times and increasing overall productivity. By selecting appropriate speeds for different hole sizes and materials, manufacturers can achieve faster drilling without compromising quality.
Reduced Scrap and Rework
By minimizing drill bit breakage and improving hole quality, speed control helps reduce scrap and rework. This translates to cost savings, improved material utilization, and higher manufacturing efficiency.
Consistency and Repeatability
Implementing standardized speed control practices ensures consistency and repeatability in the drilling process. It helps maintain uniform hole quality across different PCB designs and production runs, reducing variability and improving overall product reliability.
Frequently Asked Questions (FAQ)
1. How do I determine the optimal drill speed for a specific PCB material?
The optimal drill speed for a specific PCB material depends on factors such as the material’s hardness, thermal properties, and the hole size being drilled. Refer to the manufacturer’s recommendations, consult drilling databases, or conduct pilot tests to determine the appropriate speed range. It’s important to start with conservative speeds and gradually optimize based on the results.
2. Can I use the same drill speed for all hole sizes on a PCB?
Using the same drill speed for all hole sizes on a PCB is not recommended. Smaller holes typically require higher spindle speeds to achieve clean, burr-free drilling, while larger holes may benefit from slightly lower speeds to prevent excessive heat generation and maintain hole quality. It’s best to adjust the speed based on the specific hole size requirements.
3. How often should I replace my drill bits when using speed control techniques?
The frequency of drill bit replacement depends on various factors, including the material being drilled, the hole sizes, and the spindle speeds used. Implementing proper speed control techniques can extend drill bit life, but it’s important to monitor bit wear regularly. Establish a drill bit replacement schedule based on the number of holes drilled, visual inspection of the bit condition, and any signs of deteriorating hole quality.
4. What are the consequences of using inappropriate drill speeds?
Using inappropriate drill speeds can lead to several issues, such as:
– Drill bit breakage
– Poor hole quality (burrs, roughness, delamination)
– Reduced drill bit life
– Slower drilling processes
– Increased scrap and rework
It’s crucial to select and maintain appropriate drill speeds to avoid these consequences and ensure optimal drilling performance.
5. How can I monitor and optimize my drilling process for speed control?
To monitor and optimize your drilling process for speed control, consider the following steps:
1. Establish a baseline by collecting data on current drilling performance, including hole quality, cycle times, and drill bit life.
2. Implement speed control techniques based on the factors discussed earlier, such as material properties, hole sizes, and drill bit characteristics.
3. Regularly monitor and record drilling performance metrics after implementing speed control.
4. Analyze the collected data to identify trends, improvements, or areas that require further optimization.
5. Continuously refine your speed control settings based on the analysis and feedback from operators and quality control.
By following these steps and maintaining a data-driven approach, you can effectively monitor and optimize your drilling process for speed control.
Conclusion
Speed control is a critical aspect of PCB drilling that significantly impacts hole quality, productivity, and overall manufacturing efficiency. By understanding the factors influencing drill speed selection and implementing appropriate control techniques, manufacturers can optimize the drilling process and achieve better results.
Constant speed drilling, programmable speed drilling, adaptive speed drilling, and peck drilling are among the techniques used for effective speed control. Each technique offers specific advantages and is suitable for different drilling scenarios.
To successfully implement speed control, it’s essential to establish a drilling database, conduct pilot tests, monitor drilling performance, and regularly maintain and calibrate the equipment. Training operators and promoting best practices are also crucial for ensuring consistent and reliable drilling outcomes.
The benefits of implementing speed control in PCB drilling are numerous, including improved hole quality, increased drill bit life, enhanced productivity, reduced scrap and rework, and greater consistency and repeatability.
As PCB designs continue to evolve and manufacturing demands increase, the importance of effective speed control for PCB drills cannot be overstated. By adopting best practices and staying updated with the latest technologies and techniques, manufacturers can optimize their drilling processes, improve product quality, and remain competitive in the dynamic electronics industry.
[Word count: 5,144 words]
Leave a Reply