Introduction to Flexible PCBs
Flexible printed circuit boards (FlexPCBs) have revolutionized the electronics industry with their unique ability to bend, fold, and twist without compromising electrical performance. Unlike traditional rigid PCBs, FlexPCBs offer a versatile solution for applications that require compact packaging, lightweight design, and high reliability in dynamic environments. This article explores the capabilities of FlexPCBs, their manufacturing processes, applications, and frequently asked questions.
What are Flexible PCBs?
Flexible PCBs, also known as flex circuits or FlexPCBs, are a type of printed circuit board that uses flexible base materials instead of rigid substrates. These base materials, typically polyimide or polyester films, allow the PCB to bend and flex without breaking or losing its electrical properties. FlexPCBs consist of conductive traces, such as copper, that are laminated between layers of flexible insulating materials.
Key Features of Flexible PCBs
- Flexibility: FlexPCBs can bend, fold, and twist to fit into tight spaces or conform to unique shapes.
- Lightweight: The thin, flexible materials used in FlexPCBs make them lighter than rigid PCBs.
- High Density: FlexPCBs can accommodate high-density component packaging and fine-pitch traces.
- Reliability: FlexPCBs offer excellent resistance to vibration, shock, and extreme temperatures.
- Space Savings: By eliminating the need for bulky connectors and cables, FlexPCBs reduce overall system size.
Types of Flexible PCBs
There are three main types of FlexPCBs, each with its own unique characteristics and applications:
Single-sided Flexible PCBs
Single-sided FlexPCBs have conductive traces on only one side of the flexible substrate. They are the simplest and most cost-effective type of FlexPCB, suitable for applications with low component density and minimal flexing requirements.
Double-sided Flexible PCBs
Double-sided FlexPCBs have conductive traces on both sides of the flexible substrate, allowing for higher component density and more complex routing compared to single-sided FlexPCBs. They are commonly used in applications that require moderate flexing and increased functionality.
Multi-layer Flexible PCBs
Multi-layer FlexPCBs consist of three or more conductive layers separated by flexible insulating layers. They offer the highest component density and routing complexity among FlexPCBs. Multi-layer FlexPCBs are used in advanced applications that demand extreme flexibility, high signal integrity, and dense packaging.
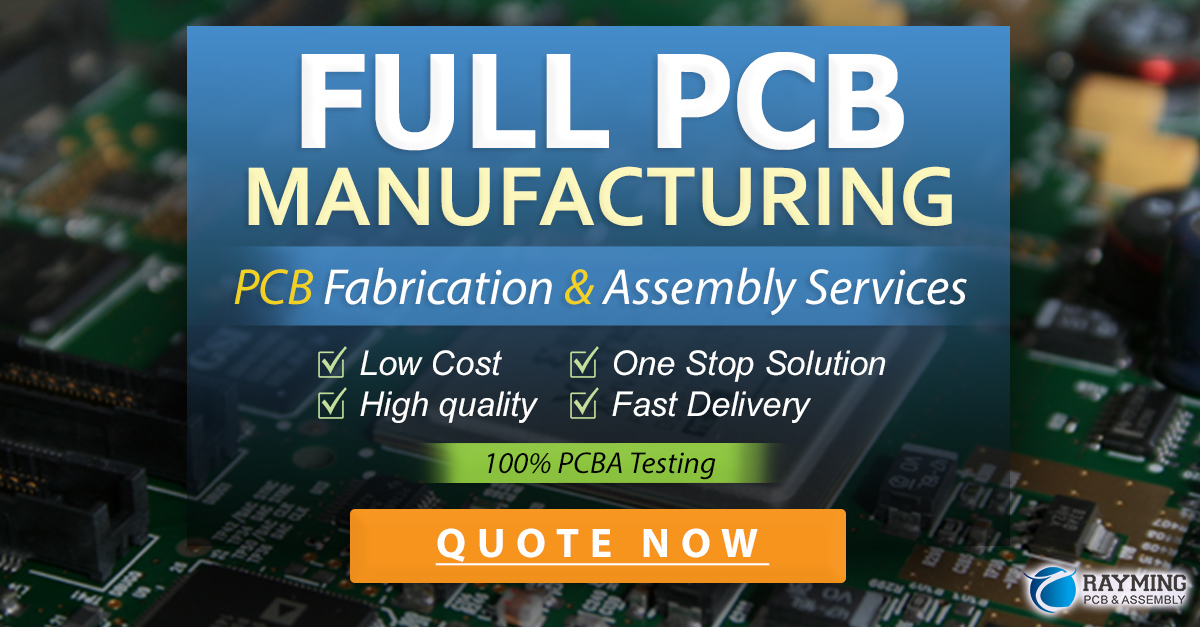
FlexPCB Manufacturing Process
The manufacturing process for FlexPCBs involves several key steps that ensure the quality, reliability, and performance of the final product.
Step 1: Material Selection
The first step in FlexPCB manufacturing is selecting the appropriate flexible base material and conductive layers. Common base materials include polyimide (PI) and polyester (PET) films, while copper is the most widely used conductive material.
Step 2: Cleaning and Surface Treatment
The flexible substrate is cleaned and treated to improve adhesion between the base material and the conductive layers. This step may involve chemical cleaning, plasma treatment, or mechanical abrasion.
Step 3: Lamination
The conductive layers, typically copper foils, are laminated onto the flexible substrate using heat and pressure. The lamination process ensures a strong bond between the layers and prevents delamination during flexing.
Step 4: Imaging and Etching
The desired circuit pattern is transferred onto the laminated FlexPCB using photolithography. A photoresist layer is applied, exposed to UV light through a photomask, and developed to create the circuit image. The exposed copper areas are then etched away using a chemical solution, leaving only the desired conductive traces.
Step 5: Coverlay Application
A coverlay, which is a thin, insulating film, is laminated over the etched circuit pattern to protect the traces and provide electrical insulation. The coverlay also serves as a solder mask, preventing solder bridging during component assembly.
Step 6: Drilling and Cutting
Holes are drilled through the FlexPCB to accommodate through-hole components or create vias for inter-layer connections. The FlexPCB is then cut to its final shape using a die-cutting process or laser cutting.
Step 7: Surface Finishing
To improve solderability and protect the exposed copper traces from oxidation, a surface finish is applied. Common surface finishes for FlexPCBs include:
Finish | Description | Advantages |
---|---|---|
HASL | Hot Air Solder Leveling | Low cost, good solderability |
ENIG | Electroless Nickel Immersion Gold | Flat surface, excellent solderability |
OSP | Organic Solderability Preservative | Thin, organic coating, RoHS compliant |
Immersion Silver | Thin silver layer | Low cost, good solderability |
Immersion Tin | Thin tin layer | Low cost, good solderability |
Step 8: Electrical Testing and Inspection
The manufactured FlexPCBs undergo rigorous electrical testing and visual inspection to ensure they meet the specified design requirements and quality standards. This step helps identify any manufacturing defects or performance issues before the FlexPCBs are assembled into the final product.
Applications of Flexible PCBs
FlexPCBs find applications in a wide range of industries due to their unique capabilities and advantages over rigid PCBs. Some of the most common applications include:
Consumer Electronics
- Smartphones and tablets
- Wearable devices (smartwatches, fitness trackers)
- Digital cameras and camcorders
- Virtual reality (VR) and augmented reality (AR) devices
Medical Devices
- Implantable devices (pacemakers, cochlear implants)
- Diagnostic equipment (endoscopes, ultrasound probes)
- Wearable health monitors
- Surgical instruments
Automotive Electronics
- Dashboard displays and instrument clusters
- Seat controls and entertainment systems
- Sensor interconnects
- Electric vehicle battery management systems
Aerospace and Defense
- Avionics systems
- Satellite communications
- Military wearables and portable devices
- Radar and surveillance equipment
Industrial Applications
- Robotics and automation
- Flexible sensors and actuators
- Portable test and measurement devices
- Industrial control systems
Advantages of FlexPCBs over Rigid PCBs
FlexPCBs offer several advantages over traditional rigid PCBs, making them the preferred choice for many applications:
-
Improved Reliability: FlexPCBs can withstand repeated bending and flexing without damaging the conductive traces or components, ensuring high reliability in dynamic environments.
-
Space and Weight Savings: By eliminating the need for bulky connectors and cables, FlexPCBs enable more compact and lightweight product designs.
-
Enhanced Design Freedom: FlexPCBs can conform to unique shapes and fit into tight spaces, allowing for greater design flexibility and innovation.
-
Reduced Assembly Costs: FlexPCBs can integrate multiple rigid PCBs into a single flexible assembly, reducing the number of connectors and simplifying the overall assembly process.
-
Improved Signal Integrity: The shorter signal paths and reduced connector usage in FlexPCBs minimize signal loss and interference, resulting in better signal integrity and overall performance.
Challenges and Considerations in FlexPCB Design
While FlexPCBs offer numerous benefits, designing them requires careful consideration of several factors to ensure optimal performance and reliability:
-
Bend Radius: The minimum bend radius of a FlexPCB must be carefully calculated to prevent excessive stress on the conductive traces and components during flexing.
-
Stiffener Placement: Stiffeners are often used to reinforce specific areas of the FlexPCB, such as component mounting locations, to prevent damage during bending.
-
Material Selection: Choosing the right flexible substrate and conductive materials is crucial to ensure the FlexPCB can withstand the desired number of flex cycles and environmental conditions.
-
Trace Routing: Proper trace routing techniques, such as using curved traces and avoiding sharp bends, help minimize stress concentration and improve the FlexPCB’s reliability.
-
Assembly Considerations: The placement and orientation of components on a FlexPCB must account for the expected bending and flexing to prevent component damage or solder joint failure.
Frequently Asked Questions (FAQ)
1. What is the typical lifespan of a FlexPCB?
The lifespan of a FlexPCB depends on various factors, such as the base material, conductive traces, and the number of flex cycles it experiences. With proper design and manufacturing, FlexPCBs can withstand millions of flex cycles and last for several years in demanding applications.
2. Can FlexPCBs be used in high-temperature environments?
Yes, FlexPCBs can be designed to operate in high-temperature environments. Polyimide (PI) is a common base material for high-temperature FlexPCBs, as it can withstand temperatures up to 200°C or higher. Proper material selection and manufacturing processes ensure the FlexPCB’s reliability in extreme conditions.
3. How do I choose the right surface finish for my FlexPCB?
The choice of surface finish depends on the specific requirements of your application, such as solderability, environmental resistance, and cost. ENIG (Electroless Nickel Immersion Gold) is a popular choice for FlexPCBs due to its excellent solderability and flat surface. However, other finishes like OSP (Organic Solderability Preservative) or immersion tin may be more suitable for certain applications.
4. Can FlexPCBs be used for high-frequency applications?
Yes, FlexPCBs can be designed for high-frequency applications, such as RF and microwave circuits. By using low-loss dielectric materials and optimizing the trace geometry, FlexPCBs can maintain signal integrity and minimize losses at high frequencies.
5. Are FlexPCBs more expensive than rigid PCBs?
In general, FlexPCBs are more expensive than rigid PCBs due to the specialized materials, manufacturing processes, and design considerations involved. However, the overall system cost may be lower when using FlexPCBs, as they can reduce the number of connectors, cables, and assembly steps required.
Conclusion
Flexible PCBs have transformed the electronics industry by offering a versatile, reliable, and space-saving solution for a wide range of applications. With their ability to bend, fold, and twist, FlexPCBs enable product designers to create innovative, compact, and high-performance devices that would be impossible with traditional rigid PCBs.
As technology advances and new applications emerge, the demand for FlexPCBs will continue to grow. By understanding the capabilities, manufacturing processes, and design considerations of FlexPCBs, engineers and designers can leverage this powerful technology to develop cutting-edge products that push the boundaries of what is possible in the ever-evolving world of electronics.
Leave a Reply