Introduction to Wave-Reflow Distinction
In the world of Electronics Manufacturing, soldering is a crucial process that ensures the proper connection and stability of components on a printed circuit board (PCB). Two of the most commonly used soldering techniques are Wave Soldering and reflow soldering. While both methods aim to achieve the same goal, they differ in their processes, applications, and the types of components they can handle. Understanding the distinction between wave soldering and reflow soldering is essential for manufacturers to choose the most suitable method for their specific requirements.
What is Wave Soldering?
Wave soldering is a process that involves passing a PCB over a molten solder bath. The components are first placed on the PCB, and then the board is moved over a wave of molten solder. The solder adheres to the exposed metal surfaces, creating a strong electrical and mechanical connection between the components and the PCB.
Advantages of Wave Soldering
- High-speed process suitable for large-scale production
- Can handle through-hole components effectively
- Provides a strong mechanical bond
- Suitable for Double-sided PCBs
Disadvantages of Wave Soldering
- Not suitable for surface mount components (SMDs)
- Requires precise control of solder wave height and temperature
- Can cause thermal stress on components due to high temperatures
- Difficult to control the amount of solder applied to each joint
What is Reflow Soldering?
Reflow soldering is a process that involves applying solder paste to the PCB pads, placing the components on the paste, and then heating the entire assembly in a controlled manner. The solder paste melts and forms a strong bond between the components and the PCB pads as it cools down.
Advantages of Reflow Soldering
- Ideal for surface mount components (SMDs)
- Precise control over the amount of solder applied to each joint
- Consistent and reliable solder joints
- Suitable for high-density PCBs
Disadvantages of Reflow Soldering
- Not suitable for through-hole components
- Requires specialized equipment, such as a reflow oven
- Sensitive to moisture and humidity
- Can cause tombstoning of small components if not properly controlled
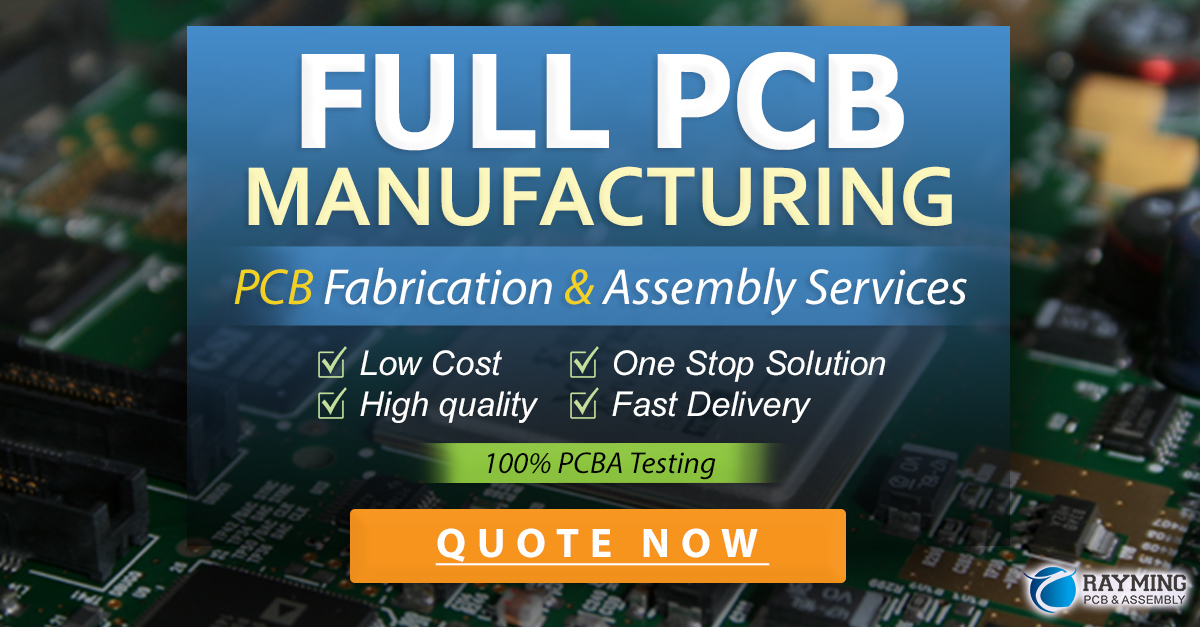
Comparison between Wave Soldering and Reflow Soldering
Factor | Wave Soldering | Reflow Soldering |
---|---|---|
Component Types | Through-hole | Surface mount |
PCB Density | Low to medium | High |
Process Speed | High | Medium |
Solder Joint Consistency | Variable | High |
Thermal Stress on Components | High | Low |
Equipment Cost | Low to medium | High |
Skill Level Required | Medium | High |
Choosing the Right Soldering Method
When deciding between wave soldering and reflow soldering, consider the following factors:
-
Component types: If your PCB primarily uses through-hole components, wave soldering is the preferred method. For surface mount components, reflow soldering is the way to go.
-
PCB density: Reflow soldering is better suited for high-density PCBs with closely spaced components, while wave soldering can handle lower-density boards.
-
Production volume: Wave soldering is ideal for large-scale production due to its high speed, while reflow soldering is more suitable for smaller batches or prototypes.
-
Budget: Wave Soldering Equipment is generally less expensive than reflow soldering equipment, which may influence your decision based on your budget constraints.
Frequently Asked Questions (FAQ)
-
Q: Can wave soldering and reflow soldering be used on the same PCB?
A: Yes, it is possible to use both methods on the same PCB, especially if the board contains a mix of through-hole and surface mount components. This is known as a mixed-technology PCB. -
Q: Is it necessary to use flux in both wave soldering and reflow soldering?
A: Yes, flux is essential in both processes to remove oxides from the metal surfaces and promote proper solder wetting and adhesion. -
Q: Can reflow soldering be used for double-sided PCBs?
A: Yes, reflow soldering can be used for double-sided PCBs, but it requires a more complex process involving multiple solder paste applications and heating cycles. -
Q: What is Selective Soldering, and how does it relate to wave and reflow soldering?
A: Selective soldering is a specialized process that combines aspects of both wave and reflow soldering. It involves applying solder to specific areas of a PCB using a precisely controlled solder fountain or mini-wave. Selective soldering is often used for mixed-technology PCBs or boards with components that are sensitive to high temperatures. -
Q: Are there any environmental concerns associated with wave and reflow soldering?
A: Yes, both processes involve the use of lead-based solder alloys, which can have negative environmental and health impacts if not handled properly. Many manufacturers are now switching to lead-free solder alloys to comply with regulations and reduce their environmental footprint.
Conclusion
Understanding the distinction between wave soldering and reflow soldering is crucial for electronics manufacturers to make informed decisions about their production processes. While both methods have their advantages and disadvantages, the choice ultimately depends on the specific requirements of the PCB, including component types, board density, production volume, and budget constraints. By carefully considering these factors and the unique characteristics of each soldering method, manufacturers can ensure that their PCBs are produced with the highest quality and reliability.
Leave a Reply