Introduction to Desoldering
Desoldering is the process of removing solder and components from a printed circuit board (PCB). It is an essential skill for anyone involved in electronics repair, modification, or prototyping. One of the most common desoldering tasks is removing solder from a circuit board hole, also known as desoldering a hole.
Why Desolder a Hole?
There are several reasons why you might need to desolder a hole on a PCB:
- To replace a damaged or faulty component
- To modify the circuit by removing or adding components
- To clean up excess solder that may be causing short circuits
- To repair damaged or lifted PCB pads
Tools and Equipment Required for Desoldering
Before you start desoldering, it’s essential to have the right tools and equipment. Here’s what you’ll need:
Tool | Description |
---|---|
Soldering Iron | A tool that heats up and melts solder. Choose a soldering iron with adjustable temperature control and a fine tip for precision work. |
Desoldering Pump (Solder Sucker) | A manual tool that uses suction to remove molten solder from a hole or joint. |
Desoldering Braid (Solder Wick) | A braided wire coated with flux that absorbs molten solder when heated with a soldering iron. |
Flux | A chemical that helps solder flow and adhere to surfaces. Use a no-clean, rosin-based flux for electronics work. |
Tweezers | Used for handling small components and cleaning up debris. |
Safety Glasses | Protects your eyes from solder splashes and debris. |
Ventilation | Solder fumes can be harmful, so work in a well-ventilated area or use a fume extractor. |
Step-by-Step Guide to Desoldering a Hole
Step 1: Prepare Your Workspace
- Clear your workspace and lay out all the necessary tools and equipment.
- Ensure that your work area is well-lit and ventilated.
- Put on your safety glasses.
Step 2: Clean the PCB
- Before desoldering, clean the PCB to remove any dirt, dust, or grease that may hinder the process.
- Use isopropyl alcohol and a soft brush or lint-free cloth to clean the area around the hole.
- Let the PCB dry completely before proceeding.
Step 3: Apply Flux
- Apply a small amount of flux to the solder joint using a flux pen or brush.
- Flux helps the solder melt and flow more easily, making it easier to remove.
Step 4: Heat the Solder
- Turn on your soldering iron and let it heat up to the appropriate temperature (around 600-700°F or 315-370°C for lead-based solder, or 700-800°F or 370-425°C for lead-free solder).
- Touch the tip of the soldering iron to the solder joint and let it melt the solder.
- Keep the soldering iron in place for a few seconds to ensure that the solder is fully molten.
Step 5: Remove the Solder with a Desoldering Pump
- While keeping the soldering iron in place, position the nozzle of the desoldering pump close to the molten solder.
- Press the release button on the desoldering pump to create suction and remove the solder.
- Repeat this process until most of the solder is removed from the hole.
Step 6: Remove Remaining Solder with Desoldering Braid
- If there is still some solder remaining in the hole, use desoldering braid to remove it.
- Cut a piece of desoldering braid and place it over the hole.
- Press the tip of the soldering iron onto the braid, allowing it to heat up and absorb the solder.
- Move the braid around the hole to ensure that all the solder is absorbed.
- Repeat this process until the hole is free of solder.
Step 7: Clean the PCB
- After desoldering, clean the PCB again with isopropyl alcohol to remove any flux residue or debris.
- Inspect the hole to ensure that it is clean and free of solder.
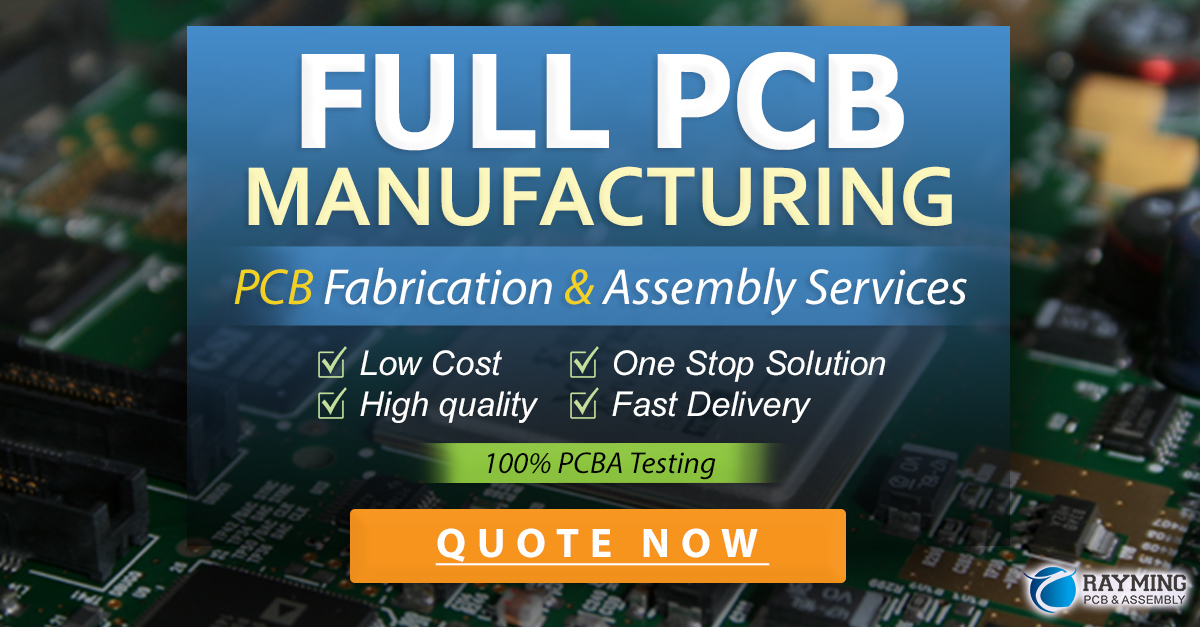
Tips and Tricks for Successful Desoldering
-
Use the right tools: Invest in high-quality desoldering tools, such as a good soldering iron, desoldering pump, and desoldering braid.
-
Adjust the soldering iron temperature: Different types of solder require different temperatures to melt. Ensure that your soldering iron is set to the appropriate temperature for the type of solder you are working with.
-
Apply flux: Flux helps the solder melt and flow more easily, making it easier to remove. Always apply flux before desoldering.
-
Work quickly: Molten solder can damage the PCB if left in contact for too long. Work quickly and efficiently to minimize the risk of damage.
-
Practice: Desoldering is a skill that requires practice to master. Start with simple projects and work your way up to more complex ones as your skills improve.
Common Mistakes to Avoid
-
Overheating the PCB: Applying too much heat for too long can damage the PCB and surrounding components. Work quickly and efficiently to minimize heat exposure.
-
Using the wrong tools: Using the wrong tools, such as a soldering iron with a tip that is too large or a desoldering pump that is not powerful enough, can make the desoldering process more difficult and increase the risk of damage.
-
Not applying enough flux: Without enough flux, the solder may not melt and flow properly, making it harder to remove.
-
Not cleaning the PCB: Flux residue and debris left on the PCB can cause corrosion and other issues over time. Always clean the PCB after desoldering.
Conclusion
Desoldering a hole on a PCB is a crucial skill for anyone involved in electronics repair or modification. By following the steps outlined in this guide and using the right tools and techniques, you can successfully remove solder from a circuit board hole without damaging the PCB or surrounding components. Remember to work quickly, apply flux, and clean the PCB after desoldering to ensure the best results.
Frequently Asked Questions (FAQ)
1. What is the best type of soldering iron for desoldering?
A: The best type of soldering iron for desoldering is one with adjustable temperature control and a fine tip for precision work. Look for a soldering iron with a power rating of at least 30 watts.
2. Can I use a regular soldering iron for desoldering?
A: While it is possible to use a regular soldering iron for desoldering, it is not recommended. Desoldering requires more heat and precision than regular soldering, so it is best to use a dedicated desoldering tool, such as a desoldering pump or desoldering braid.
3. What is the difference between a desoldering pump and desoldering braid?
A: A desoldering pump, also known as a solder sucker, is a manual tool that uses suction to remove molten solder from a hole or joint. Desoldering braid, also known as solder wick, is a braided wire coated with flux that absorbs molten solder when heated with a soldering iron. Both tools are used for desoldering, but desoldering braid is better for removing small amounts of solder or cleaning up residue.
4. Can I desolder a surface-mounted component?
A: Yes, you can desolder a surface-mounted component, but it requires a different technique than desoldering a through-hole component. To desolder a surface-mounted component, you will need to use a hot air rework station or a specialized desoldering iron with a flat tip.
5. How do I know when the solder is fully molten?
A: When the solder is fully molten, it will appear shiny and liquid. You should also be able to easily move the component or desoldering tool through the molten solder. If the solder appears dull or solid, it is not fully molten and will be difficult to remove.
Leave a Reply