Why is PCB Edge Plating Important?
PCB edge plating is crucial for several reasons:
-
Durability: The exposed edges of a PCB are susceptible to damage from handling, vibration, and environmental factors such as moisture and contaminants. Edge plating creates a protective barrier that helps prevent chipping, cracking, and delamination of the board’s layers.
-
Electrical Connectivity: In some PCB Designs, the edge of the board may be used as a connector or contact point. Edge plating ensures reliable electrical connectivity by providing a conductive surface for mating with other components or connectors.
-
Aesthetics: A well-plated edge gives the PCB a polished, professional appearance. This is particularly important for boards that are visible in the final product or used in high-end applications.
-
Compliance with Industry Standards: Many industry standards, such as IPC-6012, have specific requirements for edge plating to ensure the quality and reliability of the PCB.
The PCB Edge Plating Process
The PCB edge plating process typically involves the following steps:
-
Edge Preparation: Before plating, the edges of the PCB are prepared by either routing or cutting. Routing uses a specialized machine to remove excess material and create a smooth, even edge. Cutting involves using a saw or blade to trim the board to the desired size.
-
Cleaning: The edges of the board are thoroughly cleaned to remove any debris, oils, or contaminants that may interfere with the plating process. This step is critical to ensure proper adhesion of the plating material.
-
Activation: The edges of the board are chemically treated to create a surface that is receptive to the plating material. This typically involves a series of dips in various solutions, such as acid cleaners and conditioners.
-
Plating: The activated edges of the board are then exposed to the plating solution, which contains ions of the desired metal (e.g., copper, gold, or nickel). An electric current is applied, causing the metal ions to bond to the edge of the board, creating a thin, even layer of plating.
-
Inspection and Quality Control: After plating, the board undergoes a thorough inspection to ensure that the plating is of the desired thickness, uniformity, and adherence. Any defects or inconsistencies are addressed before the board moves on to the next stage of production.
Types of PCB Edge Plating
There are several types of edge plating used in PCB manufacturing, each with its own unique properties and advantages:
-
Copper Edge Plating: Copper is the most common material used for edge plating due to its excellent electrical conductivity, durability, and low cost. Copper plating is often used as a base layer for other plating materials, such as gold or nickel.
-
Gold Edge Plating: Gold is an excellent choice for edge plating when high reliability, corrosion resistance, and superior electrical conductivity are required. Gold plating is often used in high-end applications, such as aerospace, medical devices, and military equipment.
-
Nickel Edge Plating: Nickel is known for its hardness, durability, and resistance to wear and corrosion. Nickel plating is often used as an undercoat for gold plating, providing a barrier layer that prevents the diffusion of copper into the gold layer.
-
Tin Edge Plating: Tin is a soft, ductile metal that is often used for edge plating in applications where solderability is important. Tin plating provides a surface that is easy to solder and helps prevent the formation of copper oxide, which can interfere with the soldering process.
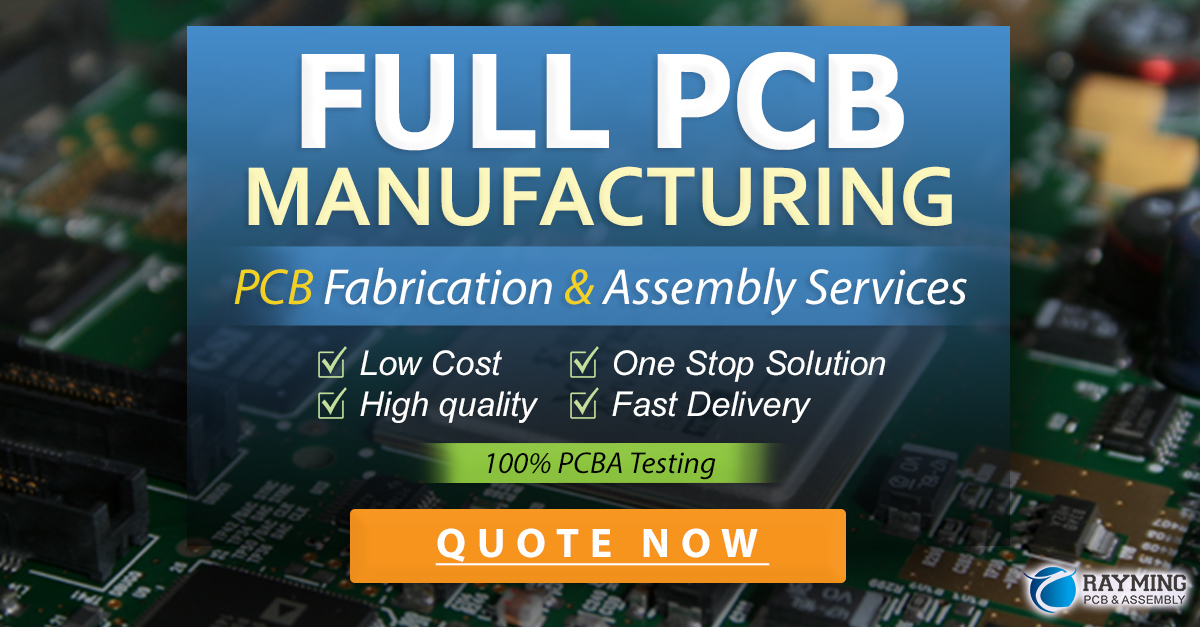
Advantages of PCB Edge Plating
PCB edge plating offers several benefits, including:
-
Enhanced Durability: Edge plating protects the board from damage caused by handling, vibration, and environmental factors, extending the lifespan of the PCB.
-
Improved Electrical Connectivity: Plated edges provide a reliable, conductive surface for connecting the PCB to other components or connectors.
-
Better Aesthetics: A well-plated edge gives the PCB a professional, polished appearance, which is important for high-end applications or products where the board is visible.
-
Compliance with Industry Standards: Edge plating helps ensure that the PCB meets the requirements of various industry standards, such as IPC-6012, which specify minimum plating thicknesses and other quality criteria.
-
Cost-Effective: Edge plating is a relatively inexpensive process that can significantly improve the overall quality and reliability of the PCB.
Challenges and Considerations
While PCB edge plating offers many benefits, there are also some challenges and considerations to keep in mind:
-
Design Considerations: The design of the PCB must take into account the specific requirements for edge plating, such as the desired plating thickness, material, and any special geometries or features.
-
Manufacturing Complexity: Edge plating adds an additional step to the PCB manufacturing process, which can increase complexity and lead time.
-
Cost: While edge plating is generally cost-effective, it does add to the overall cost of the PCB. The specific cost will depend on factors such as the plating material, thickness, and the size and complexity of the board.
-
Environmental Concerns: Some plating processes involve the use of hazardous chemicals and generate waste that must be properly managed and disposed of to minimize environmental impact.
FAQ
-
Q: Is edge plating necessary for all PCBs?
A: No, not all PCBs require edge plating. The decision to use edge plating depends on the specific requirements of the application, such as the need for enhanced durability, improved electrical connectivity, or compliance with industry standards. -
Q: What is the most common material used for PCB edge plating?
A: Copper is the most common material used for PCB edge plating due to its excellent electrical conductivity, durability, and low cost. Other materials, such as gold, nickel, and tin, are used in specific applications that require their unique properties. -
Q: How thick is the plating layer on a PCB edge?
A: The thickness of the plating layer can vary depending on the specific requirements of the application and the industry standards being followed. Typical plating thicknesses range from a few microns to several tens of microns. -
Q: Can edge plating be applied to any type of PCB?
A: Edge plating can be applied to most types of PCBs, including rigid, flexible, and rigid-flex boards. However, the specific plating process and materials used may need to be adapted to the unique characteristics of each board type. -
Q: How does edge plating affect the manufacturing lead time for a PCB?
A: Edge plating adds an additional step to the PCB manufacturing process, which can increase the overall lead time. The specific impact on lead time will depend on factors such as the complexity of the board, the plating materials and thicknesses required, and the capacity of the manufacturing facility.
Plating Material | Advantages | Disadvantages |
---|---|---|
Copper | – Excellent electrical conductivity – Good durability – Low cost |
– Prone to oxidation – May require additional finishing for some applications |
Gold | – High reliability – Superior corrosion resistance – Excellent electrical conductivity |
– Higher cost compared to other materials – Soft and prone to wear |
Nickel | – Hard and durable – Resistant to wear and corrosion – Provides a barrier layer for gold plating |
– Lower electrical conductivity compared to copper and gold – May require additional finishing for some applications |
Tin | – Good solderability – Prevents copper oxidation – Ductile and easy to work with |
– Soft and prone to wear – Lower electrical conductivity compared to copper and gold |
In conclusion, PCB edge plating is a critical process in the manufacturing of high-quality, reliable printed circuit boards. By applying a thin layer of conductive material to the edges of the board, edge plating enhances durability, improves electrical connectivity, and provides a professional appearance. With a range of plating materials available, each with its own unique properties and advantages, PCB designers and manufacturers can select the best option for their specific application requirements. While edge plating does add some complexity and cost to the manufacturing process, the benefits it provides in terms of board performance and longevity make it a worthwhile investment for many PCB Applications.
Leave a Reply