Introduction
Printed circuit board (PCB) assembly is the process of soldering electronic components to a PCB board. It involves placing components in their correct positions on the board and soldering their leads or terminals to the board’s conductive pads.
Prototype PCB assembly refers specifically to assembling prototype boards in small quantities for testing and development purposes. Prototypes allow engineers to evaluate the design and functionality of a new electronic product before committing to full-scale manufacturing. Prototyping is crucial for catching errors early and minimizing costs and delays down the road.
This article provides an in-depth look at prototype PCB assembly. It covers the prototyping process step-by-step, the different assembly methods, and key considerations when having prototype boards assembled.
Overview of the Prototype PCB Assembly Process
Prototype PCB assembly follows the same general workflow as production PCB assembly, but on a smaller scale. The main steps are:
1. Obtaining PCB Prototypes
The first step is acquiring bare PCBs in the quantities needed for testing. For prototypes, PCBs are usually produced in small batches by specialized quick-turn PCB manufacturers. Common quantities for prototype runs are 10, 25, 50 or 100 boards.
The PCB designer sends Gerber files to the PCB manufacturer. The manufacturer creates the bare boards and ships them to the assembly company or in-house assembly team. Lead times for prototype PCB production can be as fast as 24 hours.
2. Sourcing Components
The next step is procuring all the required electronic components for the build. Components may include:
- Integrated circuits (ICs)
- Resistors, capacitors, inductors
- Transistors, diodes
- Connectors, switches, buttons
- Light emitting diodes (LEDs)
- Oscillators, crystals
- Any other active or passive parts required
For prototypes, only small quantities of each component are needed. Components can be ordered in reels from distributors.
3. Kitting
Kitting or kit preparation involves organizing the PCBs and separate components into kits to feed the assembly lines. The components required for each board are placed in bins or trays and clearly labeled. This makes the assembly process more efficient.
4. Solder Paste Application
Solder paste is applied to the pads on the PCBs where components will be placed. It is usually applied by stenciling – a stencil with cutouts matching the pads is aligned over the board, and solder paste is squeegeed over the stencil. The solder paste deposits get transferred to the pads.
For prototypes, solder paste can be applied manually with a syringe for greater control. Stencils may not be cost effective for small runs.
5. Pick and Place Assembly
Components are precisely placed on the solder paste pads either manually or using a pick and place machine. Pick and place uses vacuum nozzles to pick components from feeders and position them on the board.
For prototyping, manual placement may be preferred for flexibility and lower equipment costs. But pick and place, even small desktop versions, improves efficiency and accuracy, especially for boards with many tiny components like 0201 or 01005 sized passives.
6. Soldering
The assembly is soldered using a reflow oven or manually with an iron. Reflow heats the entire board to melt the solder paste and permanently attach the components. Manual soldering can be useful for reworking errors found during testing.
For prototypes, batch style reflow ovens are commonly used rather than inline conveyor ovens. Some companies even use toaster ovens, but this does not yield the most consistent results.
7. Post Solder Cleaning
Any flux residue is cleaned off the boards after soldering, usually by washing with cleaners or solvents. This step may be skipped for prototypes.
8. Programming/Configuration
If the board includes programmable devices like microcontrollers, they are programmed with their firmware at this stage. Any necessary configuration or testing setup is also performed.
9. Testing and Inspection
Each populated PCB is visually inspected and electrically tested to verify the board and components are functioning correctly. If any errors or bugs are found, rework and modifications may be needed.
10. Box Build
For complete prototype units, the tested boards are integrated into cases or enclosures with additional hardware like displays, connectors and cables.
Once the process is completed, the fully assembled and tested prototype boards are ready for practical use and evaluation. Feedback from prototyping is used to refine the design before full production.
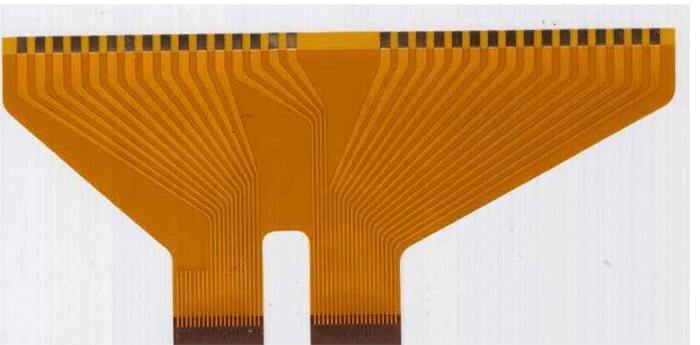
Common Prototype Assembly Methods
There are several assembly techniques used for PCB prototyping depending on production volumes, complexity, budget and other factors.
Low Volume Manual Assembly
For assembling just a few prototypes, every step can be performed manually. The small number of boards can be populated by hand without much specialized equipment. This allows great flexibility but lacks efficiency and repeatability.
Manual board stuffing with an iron is suitable for simple boards with larger component packages. For boards with hundred of tiny SMT components, manual assembly becomes challenging.
Hybrid Manual + Automated Assembly
This method combines manual board handling and placement with automated soldering.
A benchtop SMT pick-and-place machine is used to accurately place tiny surface mount components. A small batch reflow oven then solders the placements.
Additional through-hole components may be inserted manually and hand soldered. This improves efficiency while keeping equipment costs down.
Partial Automation
For higher volumes like 50-100 prototypes, more automated equipment can be utilized.
Dedicated pick-and-place machines can populate most components. A solder paste printer applies solder paste precisely using a stencil. A benchtop reflow oven solders the boards.
Operators perform supplemental tasks like loading boards, doing touch up and manual insertion work, inspection and testing.
This achieves good repeatability with moderate equipment expenses. The process mimics larger production SMT assembly lines.
Full Automation
Fully automated assembly lines contain conveyors to move boards between machines and robotic arms to handle boards.
They utilize full-sized stencil printers, high speed/high accuracy pick-and-place machines, and industrial in-line reflow ovens. Automated optical inspection (AOI) and testing can also be integrated.
This advanced equipment can assemble boards of any complexity. It requires significant capital investment but minimizes labor and maximizes throughput. Short prototype runs can be mixed in with larger production batches.
Key Considerations for Prototype PCB Assembly
Here are some important factors to weigh when assembling prototype printed circuit boards:
Number of Boards
The quantity of boards influences the methods, equipment, stencil requirements, and component purchasing. Manual assembly tends to be better for very low quantities under 10-25 boards. Around 50 boards is a good breakpoint for transitioning to more automated assembly.
Type of Components
The types of parts on the board also affect the process selection. Boards with mostly large through-hole parts are easier to hand assemble. Dense SMT boards with 01005 passives and BGAs call for precision pick-and-place and reflow.
Lead Time
How quickly assembled prototypes are needed determines options. Manual assembly can be done on demand. Automated assembly generally involves some lead time for programming, setup, stencil fabrication or procurement of components.
Assembly Partner
Prototypes can be assembled in-house or outsourced to a contract manufacturer. Large EMS companies often have high minimums. Specialized prototype assembly services offer lower quantities with quicker turnaround.
Quality
The repeatability and workmanship requirements for prototypes should align with their purpose. Lo-fi prototypes may only need functional boards. Hi-fi prototypes for demos require higher standards. Automation gives more consistent, reliable results.
Cost
Budget is always a concern. Manual methods have lower labor and equipment costs but scale poorly to higher volumes. Automated assembly has higher setup costs but cheaper per-board costs at volume. A hybrid approach can balance these tradeoffs.
By selecting suitable assembly methods and partners, companies can cost-effectively build prototypes tailored to their testing needs, timeline, and budget. Prototyping is a vital phase of product development and intelligent PCB assembly choices make the process smooth and successful.
Frequently Asked Questions
Here are some common questions about prototype PCB assembly:
What are the key benefits of prototyping before full production?
The main benefits of prototyping include:
- Evaluating the functionality and performance of the design
- Identifying any bugs or issues to improve the design
- Validating manufacturing processes and assembly methods
- Reducing risks and preventing costly mistakes before large scale production
- Allowing testing, feedback and refinements to the product
- Building initial units for demos or pilot deployments
Overall, prototyping improves design quality, saves time and money, and reduces risks further down the development timeline.
How many prototype boards should be assembled initially?
For the first version, 10-25 boards is usually a good starting point. This allows distributing boards to the design, software, testing, and field engineering teams for evaluation. For subsequent design revisions, higher quantities around 25-50 may be useful as more areas need to test the fixes and changes made.
What are some key factors when choosing a PCB assembly partner for prototypes?
Important selection criteria include:
- Ability to handle low to medium volumes
- Flexible and fast turnaround times
- Experience with prototyping specifically
- Quality standards and workmanship expertise
- Range of assembly capabilities and services
- Competitive pricing and minimum order quantities
- Good design support and engineering collaboration
How can prototyping assembly costs be reduced?
Cost reduction techniques include:
- Minimizing component types and standardizing parts
- Using more manually assembly for low volumes
- Eliminating unnecessary precision steps like solder paste printing
- Reusing programming fixtures and setups where possible
- Validating designs before assembly to reduce rework
- Grouping multiple versions/revisions into panelized boards
How are assembled prototypes tested?
Common testing methods include:
- Visual inspection of solder joints, components placement, etc
- Flying probe electrical testing of nodes, traces, and connections
- Boundary scan testing for digital components and ICs
- Functional testing of key circuits and overall operation
- Power-on testing to validate basic functionality
- Programming validation for microcontrollers, FPGAs, etc
Thorough testing at the prototype stage helps catch issues early before committing to full production.
Leave a Reply