A “turnkey” in the context of printed circuit boards (PCBs) refers to an end-to-end service model where a PCB manufacturer not only fabricates the bare boards, but also handles assembly, testing, and additional post-production support. This provides the complete package ready for the customer to use. The turnkey approach offers a straightforward solution for realizing complete functioning PCBs versus managing separate fabrication, assembly, and test vendors.
This article provides an in-depth look at PCB turnkey services encompassing definition, benefits, how it works, key elements, pricing considerations, limitations, and the future outlook of turnkey solutions. We analyze how PCB turnkeys streamline procurement, enable faster product development, and provide specialist support versus going direct to individual suppliers.
What is a PCB Turnkey Service?
A turnkey in PCBs refers to an integrated manufacturing solution where the PCB fabrication company also provides assembly and testing of the populated board on behalf of the client. This delivers a plug-and-play PCB subassembly or module direct to the buyer without requiring them to handle assembly and testing separately. It is an end-to-end solution often called PCBA (PCB Assembly) or PMTA (Populate, Mount, Test).
Key characteristics of a PCB turnkey service:
- Single vendor manages PCB fabrication, assembly, inspection, and test
- Delivers assembled, tested boards ready for system integration
- Simplifies procurement – no sourcing multiple suppliers
- Reduced logistics – no PCB shipment back and forth
- End customer receives finished working PCBs/modules
- Turnkey vendor provides engineering review and support
- Design for Manufacturing (DFM) assistance to ensure quality
The turnkey approach minimizes the effort customers must spend on manufacturing coordination by handling the entire electronics package production under one roof. This enables faster time-to-market by eliminating touch points.
Benefits of Using a PCB Turnkey Service
Opting for a turnkey PCB service over separate fabrication, assembly, and test houses provides a number of valuable benefits:
Single Point of Contact
The foremost advantage is having just one supplier to manage throughout the manufacturing process versus coordinating among multiple companies and their handoffs.
Streamlined Logistics
PCBs do not need to be shipped back and forth between separate fabrication and assembly plants, reducing transport costs and lead times.
Seamless Data Transfer
A turnkey uses integrated systems ensuring smooth data handoff between processes versus risky file conversions. All data remains onsite.
Quality Optimization
With everything onsite, a turnkey focuses intently on quality throughout fabrication, assembly, test to deliver the highest functioning boards.
Lean Production
Colocated processes maximize production efficiency through minimized work-in-process, material handling, and flexibility between steps.
One-stop Support
Customers need only open a single case for support encompassing the entire manufacturing chain versus lodging multiple individual cases.
For complex or high value PCBs, the turnkey model offers compelling benefits to buyers looking to reduce headaches and get the best quality boards.
How Does a PCB Turnkey Operation Work?
A PCB turnkey provider integrates the major steps involved in populating PCB assemblies under one roof to simplify execution for the end customer:
Fabrication
PCB fabrication builds the bare boards following customer-supplied Gerber files. This includes drilling, plating, lamination, etching, routing, finishing, and inspection to produce initial boards.
Assembly
Next, assembly populates the boards by placing and soldering components using customer bill of materials (BOM) data. This includes both SMT (surface mount) and through-hole parts.
Inspection
At multiple steps, inspection using automated optical, x-ray and flying probe tools verifies assembly quality against the PCB database. This validates production meets design.
Test
Functional testing of the assemblies ensures boards operate to electrical and performance specifications through fixture-based power-on procedures.
Programming
For programmable boards like FPGAs, firmware flashing loads the customer firmware image to impart functionality.
Shipment
Finished assemblies are then shipped directly to the customer site ready for plug-and-play integration into their product.
This seamless end-to-end fabrication through test process is made possible by a turnkey provider integrating all infrastructure, systems, and skills under one roof.
Elements of a PCB Turnkey Service
To enable smooth integrated fabrication through assembly, an effective PCB turnkey solution requires bringing together key infrastructure elements:
Fabrication
- Laminating with multilayer bonders
- Photolithography imaging
- Etching and plating lines
- Drilling and hole plating
- AOI optical inspection
- Cutting, routing, and finishing
- Cleanrooms and material handling
Assembly
- Pick-and-place equipment for SMT components
- Screen printers for solder paste dispensing
- Reflow ovens for SMT soldering
- Wave solder systems for PTH soldering
- Conformal coating application tools
Inspection
- Optical inspection tools and software
- X-ray inspection systems
- ICT fixtureless bed-of-nails testers
- Flying probe electrical testers
Test
- Custom functional test fixture design
- Instrumentation like scopes, power supplies
- Incubation ovens for burn-in
- Vibration tables for HALT/HASS
Software
- CAM software tooling
- MES and traceability systems
- Data exchange programs
- Automated test sequencers
Logistics
- Smart material planning and handling
- Integrated facility layouts
- Barcode/QR labelling and scanning
- Anti-static procedures
- Packaging and shipping
These elements working synergistically enable optimized fabrication through test under one roof.
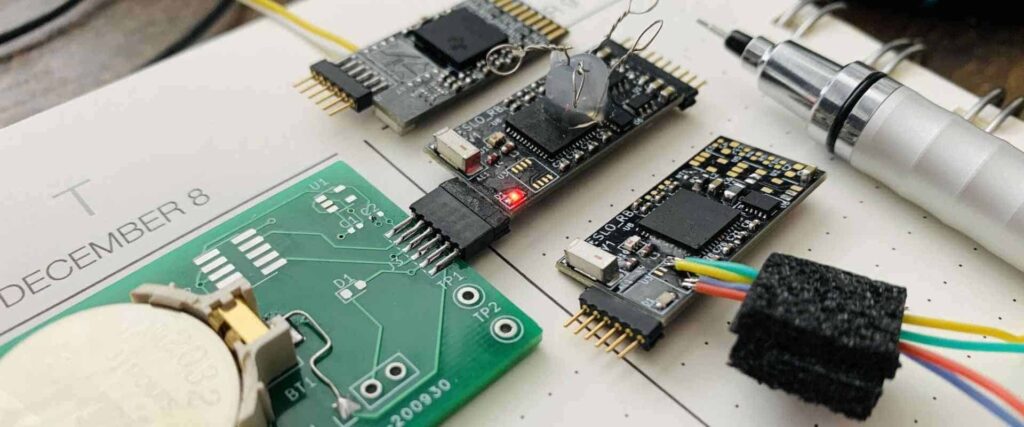
Pricing Considerations for Turnkey Services
Turnkey pricing models consider both upfront NRE costs as well as ongoing per unit pricing:
NRE Costs
- Design for Manufacturing analysis
- Test fixture design fees
- Tooling charges for assembly jigs or molds
- Programming charges for automated inspection/test
Unit Pricing
- Per board fabrication pricing
- Bill of materials (BOM) component costs
- Assembly labor based on complexity
- Inspection and test labor charges
- Packaging and shipment costs
Pricing may involve upfront NREs to ready the turnkey line balanced by lower per unit costs leveraging optimized vertical integration. Quantity discounts based on volume also typically apply.
When Does Using a Turnkey Service Make Sense?
While turnkey solutions are not ideal universally, there are certain scenarios where a turnkey approach provides the best option:
Low to Mid Volume Production
Turnkey infrastructure allows cost effective ramp from prototype through pilot build stages before very high volume justifies dedicated assembly lines.
High Mix, Low Volume
Frequent board variant changes make separate fabrication and assembly less economical versus integrated turnkey.
Advanced Technologies
Heterogenous integration, HDI, and other technologies may limit assembly options making an integrated solution preferable.
Mission Critical Quality
For highly complex, high reliability boards like medical and aerospace, turnkey integration control minimizes risk.
Fast Ramp Up
Getting to market quickly with a new product may dictate using a turnkey service to avoid lengthy sourcing of assembly partners.
For these and other specific situations where control and quality outweigh per unit cost, PCB turnkeys offer compelling benefits.
Limitations and Considerations of Turnkey Services
While turnkey PCB services streamline procurement, there are some limitations to consider as well:
Higher Per Unit Costs
Turnkey solutions may ultimately cost more per board than separate high volume operations each optimized independently.
Technology Restrictions
A given turnkey may lack specialized assembly capabilities needed for an application, necessitating outsourcing.
Quality Oversight
Turning over the entire process chain to a vendor requires rigorous supplier qualification and ongoing auditing to ensure quality.
Lead Time Impacts
Any issues with a step propagate downstream since no parallelism exists across suppliers.
Inflexibility
Change orders or pivots require rework of the entire turnkey process versus isolated suppliers.
Location Challenges
Proximity to turnkey providers may be limited based on geography for responsibilities like firmware loading.
For higher volume or specialized applications, these factors help determine when alternatives to turnkey may be preferable based on cost and capabilities.
The Future of PCB Turnkey Services
As PCBs grow in complexity and criticality across industries like auto, aerospace, and medical, demand for turnkey solutions will expand to better manage quality, risk, and development speed.
Emerging Technologies
More integration of advanced assembly techniques like die or wire bonding, MEMS, and flexible circuits.
Expanded Scope
Turnkeys moving beyond just fabrication, assembly, and test to provide box build, programming, and field failure analysis.
Design Collaboration
Early DFM input evolving to extensive turnkey-customer co-design interactions for optimization.
Supply Chain Digitization
Online turnkey platforms, documentation, and data analytics to enhance transparency and development velocity.
Continuous Improvement
Turnkey providers developing closed-loop corrective action systems tied to customer inputs for rapid issue resolution.
As PCB technology progresses, turnkeys will continue evolving into strategic manufacturing partners providing sophisticated technical solutions, not just basic fabrication and assembly services.
Conclusion
A PCB turnkey provider delivers immense value by taking full manufacturing responsibility from fabrication through shipment of completed, tested boards. This alleviates the customer’s need to manage multiple suppliers and data transfers. Turnkeys allow buyers to focus their efforts upfront during design then receive finished boards ready for system integration.
For complex mid-to-low volume boards where quality and engineering collaboration are paramount, turnkey services offer an optimized procurement solution. As PCBs become more advanced across industries, turnkey partnerships beyond just vendors will provide vital technical infrastructure enabling rapid innovation cycles and getting products to market faster.
Frequently Asked Questions
What are the steps in qualifying and selecting a new PCB turnkey partner?
Key steps when qualifying a new turnkey partner include:
- Identifying candidate providers with required technology capabilities
- Issuing RFQ with detailed requirements to request quotation
- Reviewing turnkey’s quality management system and certifications
- Auditing their facility, process controls, and staff competencies
- Reviewing example builds representative of your needs
- Validating data security and confidentiality measures
- Testing initial pilot builds to confirm performance
- Formalizing business terms and expectations in contracts
Selecting turnkeys based on rigorous qualification ensures a strategic, quality-focused partnership.
What data does a customer need to provide to a turnkey provider?
Typical data the customer provides includes:
- Gerber and drill files for fabrication
- BOM with components, descriptions, suppliers, part numbers
- Assembly drawings showing placement coordinates
- Netlist or test fixture descriptions for testing
- Any specialized assembly instructions
- Firmware image files if applicable
- Test specifications and quality expectations
- Problem escalation contacts
Providing comprehensive design data enables the turnkey to execute manufacturing correctly.
How is quality ownership managed between customer and turnkey?
Delineating quality responsibilities:
- Customer owns design quality and supplying manufacturable package.
- Turnkey owns fabrication quality like acceptable defect rates.
- Assembly quality is a shared ownership through collaboration.
- Turnkey owns test development quality and coverage.
- Customer owns test specification accuracy.
Open communication, inspection data sharing, and alignment during development assure quality.
When does it make sense to transition from a turnkey to one’s own assembly line?
Reasons to consider one’s own assembly line:
- Volume justifies investing in dedicated assembly automation
- Need for proprietary process know-how protection
- Cost reduction pressure and flexibility desired
- Turnkey location far from end customer base
- Unique technologies needed unavailable through turnkeys
- Strategic alignment by owning production
Above ~500K units annually often warrants bringing assembly in-house for optimization.
What role will turnkeys play in Industry 4.0 and smart factory initiatives?
Turnkey roles supporting smart manufacturing:
- Serving as flexible supply chain nodes with broad capabilities
- Providing specialized technologies not feasible for individual factories
- Enabling fast ramp up without long capital buildouts
- Delivering cost and carbon efficiency at scale
- Positioning capacity closer to demand dynamically
- Handling overflow production during demand spikes
- Bridging discrete steps in value chains through integration
Turnkeys will continue serving critical functions in smart, distributed production networks.
Conclusion
In summary, PCB turnkey services deliver end-to-end manufacturing solutions encompassing fabrication, assembly, test, and shipment from a single provider. For complex board builds, turnkeys alleviate sourcing logistics while providing focused quality and collaboration. As PCB applications grow in sophistication, turnkey partnerships will remain indispensable to productivity by blending advanced technical capabilities with supply chain simplification.
Leave a Reply