The United States was once home to a thriving printed circuit board (PCB) manufacturing industry. However, like many electronics sectors, economic factors led to extensive offshoring of production to Asia from the 1990s onwards. This article examines whether any PCB fabrication still exists on American soil.
The Rise and Fall of US PCB Manufacturing
The origins of printed circuit boards can be traced back to the USA in the 1930s. Early PCB pioneers developed the techniques of plating and etching conductor patterns on insulating boards. This allowed complex wiring between components to be pre-assembled into a single unit.
PCB fabrication began growing rapidly from the 1950s to serve booming post-war electronics demand. Major corporations like GE, IBM and Bell Labs funded extensive PCB manufacturing capability domestically. The new technology allowed radical miniaturization and reliability improvements in products like radios, televisions and missile guidance systems.
For over 30 years America dominated the printed circuit board industry. At its peak around 1980, there were over 3000 PCB companies based in the USA. California and New England were major hubs of PCB production and innovation.
However, fundamental economics were about to change. The lower labor costs and aggressive industrialization policies of Taiwan and China enabled them to manufacture PCBs at much cheaper unit costs. Improved global shipping and communication allowed American companies to readily offshore manufacturing with little downside. Capital investment flowed out of US facilities which struggled to compete on price with Asian operations.
Most domestic PCB suppliers went bankrupt or closed down in the 1980s and early 90s. Some outsourced part of their production activities abroad while shrinking their US footprint. The electronics manufacturing base hollowed out across the whole nation apart from pockets of defense and aerospace demand.
Current State of US Based PCB Production
It’s estimated over 98% of all printed circuit boards used by American companies today are imported from Asia. Globalization and offshoring have completely reshaped the supply chains and economics for electronics hardware.
However, there remains a small niche industry serving domestic needs in low volumes or highly complex work. The US PCB market had an estimated value of $2.5 billion in 2021. Exact figures are hard to obtain as many providers service a mix of local and global demand.
There are now less than 50 PCB manufacturers still operating in the USA to serve this shrunken market. They have restructured with lean operations, niche focus and technology investments to find profitability without mass volume. Some examples of the diverse surviving specialist PCB makers include:<div align=”center”>
Company | Specialization | Location |
---|---|---|
AT&S | High density interconnect (HDI) PCBs | California and Oregon |
TTM Technologies | Aerospace and Defense | CA, WI, OR |
San Diego PCB | Quickturn prototype PCB boards | California |
Advance Circuits | Small batch PCB production | Colorado |
Lenthor Engineering | Flexible flex-PCBs | Florida |
Their capabilities cover the full range from rapid 24 hour prototyping services to highly sophisticated boards for military platforms. Innovation around quickturn fabrication and via-in-pad HDI technology caters well to local needs.
Most surviving companies adapted or exist to service one of these three main end markets:
- Aerospace & Defense – highly regulated with domestic preferences
- Prototype engineering services – rapid turnaround needs
- Complex niche products – high mix / low volume production
A scattered geographic footprint remains. Important regional hubs of American PCB production include the defense contractors in New England, high tech manufacturers around California and Silicon Valley, and various smaller companies across the Central and Mountain states.
Reasons for Onshoring PCB Production Back to the USA
There are some expanding niches and new tailwinds where local PCB fabrication provides advantages over importing from Asia:
Reduced Shipping Times
For highly iterative product development or quickturn requirements, a US facility can deliver in days while Asia takes weeks. Faster shipping reduces lead times.
IP Protection
Concerns exist around IP theft or spying with offshore PCBA manufacturing, especially for defense customers. US production ensures full control and security over sensitive technology.
Simplified Communication
Dealing with local suppliers eliminates communication barriers and makes collaboration faster. Technical questions, custom requests or engineering changes can be resolved quicker working in the same time zone.
Improved Sustainability
More companies are trying to shrink their carbon footprint. Sourcing locally avoids major air/ocean shipping emissions across the Pacific. It also makes environmental audits of PCB suppliers easier.
Agile Supply Chain
Rather than yearly contracts, small US shops allow orders for exactly what is needed each month. This supports agile inventory management for volatile or low volume components.
While still extremely niche, these factors contribute to a modest reshoring tailwind in PCB manufacturing. High mix specialized demand seems set to be served domestically for the foreseeable future.
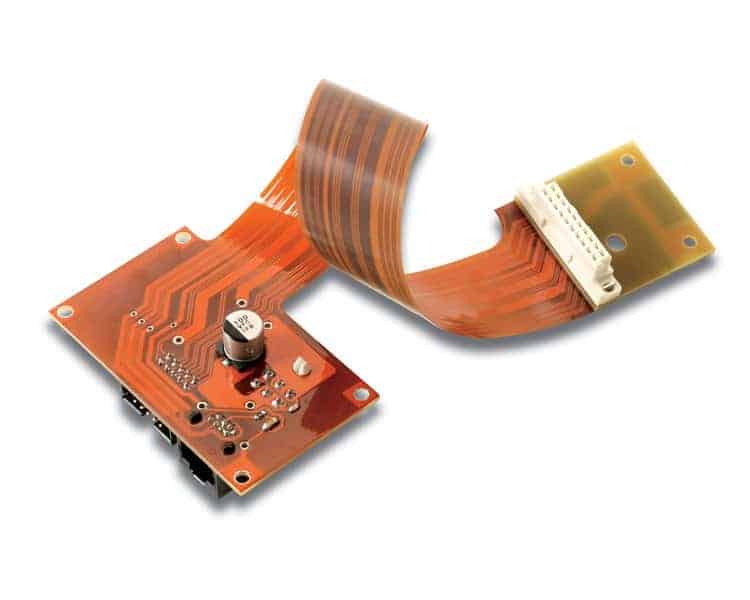
Challenges Around Building More US PCB Production
Unfortunately, large scale re-establishment of printed circuit board fabrication across the whole electronics supply chain seems unlikely. The loss of domestic volume manufacturing stemmed from structural factors which remain challenging to overcome:
No Labor Cost Advantage
Low cost labor was decisive in offshoring PCB manufacturing. Hourly wages in China and Taiwan remain below US pay rates, especially for manufacturing roles. Only highly skilled technical contributions seem valued to justify American salaries.
Lack of Scale
The drastic shrinking of volume demand left few companies with enough scale for profitability. Building massive factories to compete globally proves capital intensive and risky for uncertain local demand. Startups struggle to fund the large upfront equipment costs.
Established Asian Supply Networks
After decades developing production capacity, regions like Shenzhen in China now offer unbeatable convenience. Huge infrastructures exist around PCB manufacturing with thousands of vendors bidding aggressively. American alternatives lack this competition intensity.
Environmental Burdens
PCB production requires many hazardous chemicals like etchants, plating baths and solvents. Strict EPA rules raise compliance costs for domestic fabrication. Foreign jurisdictions regulate less stringently or enforce laxly allowing lower costs.
Without major policy shifts, these economic realities hamper any revival of commodity PCB manufacturing on American shores.
Niche onshore capacity serving fast-turn prototyping, defense electronics, small scale manufacturing and other specialty applications seems set to persist. But for volume production, the economics argue overwhelmingly for Asian supply chains. This situation seems unlikely to change in the foreseeable future.
Frequently Asked Questions
Here are answers to some common questions about US PCB manufacturing capability:
Does the military or other sensitive industries still make their own PCBs?
Yes. A few select defense and aerospace contractors still maintain internal PCB fabrication capabilities to serve proprietary needs. Sensitive programs around missile guidance, radars and communications hardware require total supply chain control and assurance over component quality. Small production lines exist inside larger system assembly plants focused entirely on internal use only.
Are there any PCB manufacturers left in Silicon Valley?
Yes. TTM Technologies still operate two domestic PCB facilities in Silicon Valley:
- One site in San Jose focuses on very dense state-of-the-art designs needing tight localized engineering collaboration.
- A facility in Stafford manufactures complex high layer count boards as well as more cost driven medium volume products. They also provide specialized RF/microwave boards supporting defense primes based in the region.
Could a startup realistically make PCBs in America today?
It’s tough but not impossible if you identify a profitable niche. The barriers to large scale commodity PCB manufacturing are just too high now without major capital. But opportunities still exist to bootstrap innovative domestic production through targeting areas like:
- Rapid turn prototyping services
- Specialized technology variants like metal-backed PCBs
- Leveraging local University equipment or small business grants
- Partnering with a larger manufacturer needing overflow capacity or technical development
Several niche startups have managed to slowly grow US-based PCB fabrication capability in recent years through clever business approaches and reliance on technology/innovation advantages over cost.
What percentage of PCBs used in the USA are manufactured domestically vs. imported?
Less than 2% of PCBs sold to US customers now originate from domestic manufacturing. The remaining 98%+ are imported fully assembled from Asia. The tiny fragment still produced in America tends to focus on highly complex, low volume or quickturn boards that justify onshore processes for technology or lead time reasons.
Could new automated production technologies like additive manufacturing boost American PCB production?
Potentially yes over the next 5-10 years if equipment costs fall. Additive techniques like inkjet printing show promise for economical small scale PCB production without the waste and chemicals of etching. As the printers improve in precision and reliability they could make local micro-factories feasible.
Formula ink companies like Nano Dimension are leading this drive to put easy PCB production onto the shopfloor with desktop equipment. But it remains early days with many engineering obstacles around alignment, features sizes and material properties still to overcome before such disruptive technologies impact mainstream manufacturing.
Leave a Reply