Introduction
Soldering is a crucial process in the creation of electronic devices, and choosing the right solder is essential for ensuring the quality and longevity of your circuit boards. With so many different types of solder available, it can be challenging to know which one is best suited for your project. In this article, we will explore nine key factors to consider when selecting the best solder for your circuit board needs.
Understanding Solder Alloys
Lead-based vs. Lead-free Solder
Traditionally, most solders contained lead due to its low melting point and excellent wetting properties. However, due to environmental and health concerns, lead-free solders have become increasingly popular. Lead-free solders typically contain a combination of tin, silver, and copper (SAC alloys).
Solder Type | Composition | Melting Point | Advantages | Disadvantages |
---|---|---|---|---|
Lead-based | Tin-Lead (Sn-Pb) | 183-190°C | Easy to use, low cost | Toxic, environmental concerns |
Lead-free | Tin-Silver-Copper (SAC) | 217-220°C | Environmentally friendly, strong joints | Higher melting point, more expensive |
Eutectic vs. Non-eutectic Solder
Eutectic solders have a specific composition that allows them to melt and solidify at a single temperature, resulting in a more uniform and consistent joint. Non-eutectic solders have a temperature range in which they transition from solid to liquid, which can lead to uneven joints if not properly controlled.
Solder Type | Melting Behavior | Advantages | Disadvantages |
---|---|---|---|
Eutectic | Melts and solidifies at a single temperature | Consistent joints, easier to work with | Limited alloy options |
Non-eutectic | Melts and solidifies over a temperature range | More alloy options, can be tailored for specific applications | Potential for uneven joints |
Factors to Consider When Choosing Solder
1. Melting Temperature
The melting temperature of the solder is a critical factor to consider, as it determines the processing temperature required for your soldering equipment. Choose a solder with a melting temperature that is compatible with your components and PCB materials to avoid damage during the soldering process.
2. Wetting Ability
Wetting ability refers to how well the molten solder spreads and adheres to the surfaces being joined. Good wetting is essential for creating strong, reliable solder joints. Factors that affect wetting ability include the alloy composition, flux type, and surface cleanliness.
3. Mechanical Strength
The mechanical strength of the solder joint is crucial for the long-term reliability of your circuit board. Solder alloys with higher tensile strength and shear strength can withstand greater mechanical stresses and vibrations, reducing the risk of joint failure.
4. Electrical Conductivity
Solder joints not only provide mechanical connections but also facilitate electrical conductivity between components. Choose a solder alloy with high electrical conductivity to ensure optimal signal integrity and minimize resistance in your circuit.
5. Thermal Conductivity
Thermal conductivity is important for applications where heat dissipation is critical, such as power electronics or high-performance computing. Solders with higher thermal conductivity can help transfer heat away from components more efficiently, improving overall system performance and reliability.
6. Flux Compatibility
Flux is a chemical compound that helps remove oxides and improve wetting during the soldering process. Different types of flux are available, such as rosin, water-soluble, and no-clean. Ensure that the solder you choose is compatible with the flux you intend to use for optimal results.
7. Environmental Considerations
As mentioned earlier, lead-free solders have become the preferred choice due to environmental and health concerns. When selecting a solder, consider the environmental impact and any regulations or standards that may apply to your industry or application.
8. Cost and Availability
While performance is a top priority, cost and availability should also be taken into account when choosing a solder. Some specialty alloys may offer superior performance but come at a higher price point or have limited availability. Strike a balance between performance, cost, and accessibility based on your project requirements and budget.
9. Application-Specific Requirements
Different applications may have specific requirements that influence solder selection. For example, aerospace and military applications may require solders with higher melting points and greater mechanical strength to withstand extreme conditions. Medical devices may need solders that are biocompatible and meet stringent cleanliness standards. Consider the unique demands of your application when making your solder choice.
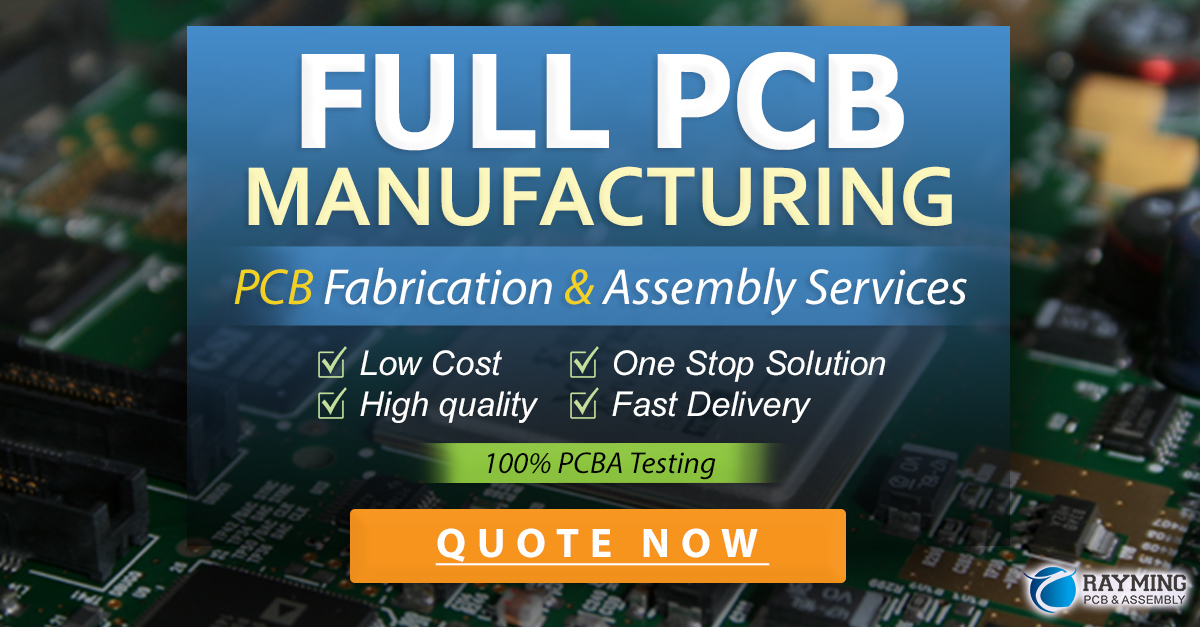
FAQ
1. What is the difference between lead-based and lead-free solder?
Lead-based solder contains a combination of tin and lead, while lead-free solder is typically composed of tin, silver, and copper. Lead-free solders have become more popular due to environmental and health concerns associated with lead.
2. What is the advantage of using a eutectic solder?
Eutectic solders melt and solidify at a single temperature, resulting in more consistent and uniform solder joints. This makes them easier to work with and reduces the risk of defects caused by uneven solidification.
3. How does the melting temperature of solder affect the soldering process?
The melting temperature of the solder determines the processing temperature required for your soldering equipment. It is important to choose a solder with a melting temperature that is compatible with your components and PCB materials to avoid damage during the soldering process.
4. What factors contribute to the mechanical strength of a solder joint?
The mechanical strength of a solder joint is influenced by the alloy composition, joint design, and soldering process. Solders with higher tensile strength and shear strength can withstand greater mechanical stresses and vibrations, reducing the risk of joint failure.
5. Why is flux compatibility important when selecting solder?
Flux helps remove oxides and improve wetting during the soldering process. Choosing a solder that is compatible with the flux you intend to use ensures optimal performance and reduces the risk of defects caused by poor wetting or residue buildup.
Conclusion
Selecting the best solder for your circuit board is a critical decision that impacts the quality, reliability, and performance of your electronic devices. By considering factors such as alloy composition, melting temperature, wetting ability, mechanical strength, electrical and thermal conductivity, flux compatibility, environmental impact, cost, and application-specific requirements, you can make an informed choice that meets the unique needs of your project. Remember to strike a balance between performance, cost, and accessibility while prioritizing the long-term reliability and functionality of your circuit board.
Leave a Reply