Motor Controller Essentials
Motor controllers are essential components in various applications, from industrial automation to robotics and electric vehicles. They play a crucial role in regulating the speed, torque, and direction of electric motors, ensuring precise control and efficient operation. In this comprehensive article, we will delve into eight key aspects of motor controllers, providing you with a solid understanding of their functionality and importance.
1. Understanding the Basics of Motor Controllers
A motor controller is an electronic device that acts as an intermediary between a power source and an electric motor. Its primary function is to control the motor’s performance by regulating the electrical energy supplied to it. Motor controllers come in different types and sizes, each designed to cater to specific motor types and application requirements.
The basic components of a motor controller include:
– Power electronics: These include devices like transistors, IGBTs, or MOSFETs that switch the power supply to the motor.
– Microcontroller or DSP: This is the “brain” of the controller, responsible for executing control algorithms and managing the overall system.
– Sensors: Sensors such as encoders, hall-effect sensors, or current sensors provide feedback on the motor’s position, speed, and current draw.
– Communication interfaces: These allow the motor controller to communicate with other devices or systems, such as a PLC or a higher-level controller.
2. Types of Motor Controllers
There are several types of motor controllers, each suitable for different motor types and applications. The most common types include:
- DC Motor Controllers:
- Used for controlling DC motors
- Suitable for applications requiring variable speed and torque control
-
Examples: PWM controllers, H-bridge controllers
-
AC Motor Controllers:
- Used for controlling AC motors, such as induction motors or synchronous motors
- Suitable for high-power applications and precise speed control
-
Examples: Variable Frequency Drives (VFDs), Soft Starters
-
Stepper Motor Controllers:
- Used for controlling stepper motors
- Provide precise position control and high torque at low speeds
-
Examples: Microstepping controllers, Chopper controllers
-
Servo Motor Controllers:
- Used for controlling servo motors
- Offer precise position, speed, and torque control
- Examples: PID controllers, FOC controllers
Motor Type | Controller Type | Key Features |
---|---|---|
DC Motors | PWM, H-bridge | Variable speed and torque control |
AC Motors | VFD, Soft Starter | High-power, precise speed control |
Stepper Motors | Microstepping, Chopper | Precise position control, high torque |
Servo Motors | PID, FOC | Precise position, speed, torque control |
3. Motor Control Techniques
Motor controllers employ various control techniques to achieve the desired motor performance. The most common techniques include:
- Pulse Width Modulation (PWM):
- Used in DC motor control
- Varies the average voltage supplied to the motor by modulating the duty cycle of the power pulses
-
Allows for smooth speed control and efficient power delivery
-
Variable Frequency Drive (VFD):
- Used in AC motor control
- Adjusts the frequency and voltage of the AC power supplied to the motor
-
Enables precise speed control and energy efficiency
-
Field-Oriented Control (FOC):
- Used in high-performance AC and servo motor control
- Provides independent control of torque and flux
-
Offers superior dynamic response and efficiency compared to traditional control methods
-
Proportional-Integral-Derivative (PID) Control:
- Used in various motor control applications
- Continuously calculates the error between the desired and actual motor performance
- Adjusts the control output based on proportional, integral, and derivative terms
4. Selecting the Right Motor Controller
Choosing the appropriate motor controller is crucial for optimal system performance and reliability. When selecting a motor controller, consider the following factors:
-
Motor Type: Ensure that the controller is compatible with the specific type of motor you are using (DC, AC, stepper, servo).
-
Power Requirements: Consider the voltage and current ratings of your motor and choose a controller that can handle those requirements.
-
Control Features: Determine the required control features, such as speed control, position control, or torque control, and select a controller that offers those capabilities.
-
Environment: Consider the operating environment of your system, including temperature, humidity, and vibration, and choose a controller with appropriate ratings and protection.
-
Communication: If your system requires communication with other devices or networks, ensure that the controller supports the necessary communication protocols (e.g., RS-485, Ethernet, CAN).
-
Scalability: Consider future expansion or changes in your system and choose a controller that offers flexibility and scalability.
5. Motor Controller Programming and Configuration
Programming and configuring a motor controller is essential for achieving the desired motor performance. The specific programming and configuration steps may vary depending on the controller type and manufacturer, but the general process involves:
- Setting Motor Parameters:
- Configure the controller with the motor’s specifications, such as rated current, voltage, speed, and number of poles.
-
Set the motor’s operating limits, such as maximum speed, acceleration, and deceleration.
-
Tuning Control Loops:
- Adjust the control loop parameters (e.g., PID gains) to achieve optimal motor response and stability.
-
Perform tuning procedures specific to the control technique being used (e.g., auto-tuning for VFDs).
-
Configuring I/O and Communication:
- Set up the controller’s input and output interfaces, such as digital and analog I/O, to interact with external devices or sensors.
-
Configure the communication settings if the controller needs to communicate with other devices or systems.
-
Programming Control Logic:
- Develop the control logic or program that governs the motor’s behavior based on the application requirements.
- Use the controller’s programming environment or software tools to write and deploy the control code.
6. Motor Controller Safety and Protection
Ensuring the safety and protection of the motor and the controller is crucial for reliable operation and longevity. Motor controllers incorporate various safety and protection features, including:
- Overcurrent Protection:
- Prevents damage to the motor and controller by limiting the current drawn by the motor.
-
Uses techniques like current limiting, fuses, or circuit breakers.
-
Overvoltage Protection:
- Protects the controller and motor from voltage spikes or surges.
-
Employs techniques like transient voltage suppressors (TVS) or metal oxide varistors (MOV).
-
Thermal Protection:
- Monitors the temperature of the controller and motor to prevent overheating.
-
Uses temperature sensors and thermal shutdown mechanisms to protect the system.
-
Short Circuit Protection:
- Detects and isolates short circuit conditions to prevent damage to the controller and motor.
-
Utilizes fast-acting fuses or electronic short circuit protection.
-
Safe Torque Off (STO):
- Provides a reliable means to prevent unexpected motor startup or movement.
- Adheres to functional safety standards like IEC 61800-5-2.
7. Motor Controller Maintenance and Troubleshooting
Regular maintenance and troubleshooting are essential for ensuring the optimal performance and longevity of motor controllers. Some key maintenance and troubleshooting practices include:
- Regular Inspection:
- Visually inspect the controller for any signs of damage, wear, or contamination.
-
Check for loose connections, frayed wires, or damaged components.
-
Cleaning and Housekeeping:
- Keep the controller and its surroundings clean and free from dust, dirt, or debris.
-
Ensure proper ventilation to prevent overheating.
-
Firmware Updates:
- Keep the controller’s firmware up to date to ensure optimal performance and compatibility.
-
Follow the manufacturer’s guidelines for firmware updates.
-
Parameter Backup:
- Regularly backup the controller’s configuration and parameter settings.
-
Store the backup in a safe location for easy restoration in case of controller failure or replacement.
-
Troubleshooting:
- Refer to the controller’s documentation or manufacturer’s support for troubleshooting guidelines.
- Use diagnostic tools or software provided by the manufacturer to identify and resolve issues.
- Monitor the controller’s performance and log any errors or abnormalities for further analysis.
8. Advancements and Future Trends in Motor Controllers
The field of motor controllers is constantly evolving, driven by advancements in technology and the increasing demands of modern applications. Some notable advancements and future trends include:
- Intelligent Motor Controllers:
- Integration of advanced control algorithms and artificial intelligence (AI) techniques.
-
Adaptive and self-learning controllers that optimize performance based on real-time data.
-
Wireless Communication:
- Increasing adoption of wireless communication protocols like Wi-Fi, Bluetooth, or ZigBee.
-
Enables remote monitoring, diagnostics, and control of motor controllers.
-
Edge Computing:
- Decentralization of control and data processing to the motor controller level.
-
Enables faster response times, reduced latency, and improved scalability.
-
Energy Efficiency:
- Development of more energy-efficient motor control techniques and hardware.
-
Focus on reducing power losses and optimizing motor performance.
-
Integration with IoT and Industry 4.0:
- Seamless integration of motor controllers with IoT platforms and industrial automation systems.
- Enables real-time monitoring, predictive maintenance, and data-driven decision making.
Frequently Asked Questions (FAQ)
- What is the difference between a motor controller and a drive?
-
A motor controller is a broader term that encompasses various devices used to control the performance of electric motors, while a drive specifically refers to a type of controller that regulates the speed, torque, and direction of a motor. Drives are a subset of motor controllers.
-
Can a motor controller be used with any type of motor?
-
No, motor controllers are designed to work with specific types of motors. It is essential to choose a controller that is compatible with the motor type being used (e.g., DC, AC, stepper, or servo motor). Using the wrong type of controller can result in poor performance or damage to the motor or controller.
-
How do I determine the power rating of a motor controller?
-
The power rating of a motor controller is determined by the voltage and current requirements of the motor it will be controlling. You need to consider the motor’s rated voltage, maximum current draw, and any additional loads or safety factors. The controller’s power rating should exceed the motor’s requirements to ensure reliable operation.
-
What is the role of feedback in motor control?
-
Feedback plays a crucial role in motor control by providing information about the motor’s actual performance, such as its position, speed, or torque. Feedback devices like encoders or sensors send signals back to the motor controller, allowing it to compare the actual performance with the desired setpoints and make necessary adjustments to maintain accurate control.
-
How often should I perform maintenance on a motor controller?
- The frequency of maintenance depends on factors such as the operating environment, duty cycle, and manufacturer’s recommendations. In general, it is advisable to perform visual inspections and cleaning at regular intervals (e.g., monthly or quarterly) and conduct more thorough maintenance, such as firmware updates or parameter backups, on an annual basis or as specified by the manufacturer.
Conclusion
Motor controllers are vital components in various applications, enabling precise control and efficient operation of electric motors. Understanding the basics of motor controllers, their types, control techniques, and selection criteria is essential for designing and implementing effective motor control systems.
Programming and configuring motor controllers, ensuring safety and protection, and performing regular maintenance and troubleshooting are crucial for optimal performance and longevity. As technology advances, motor controllers continue to evolve, incorporating intelligent control algorithms, wireless communication, and integration with IoT and Industry 4.0 paradigms.
By staying informed about the latest advancements and best practices in motor control, engineers and technicians can design and maintain robust, efficient, and future-proof motor control systems that drive innovation across industries.
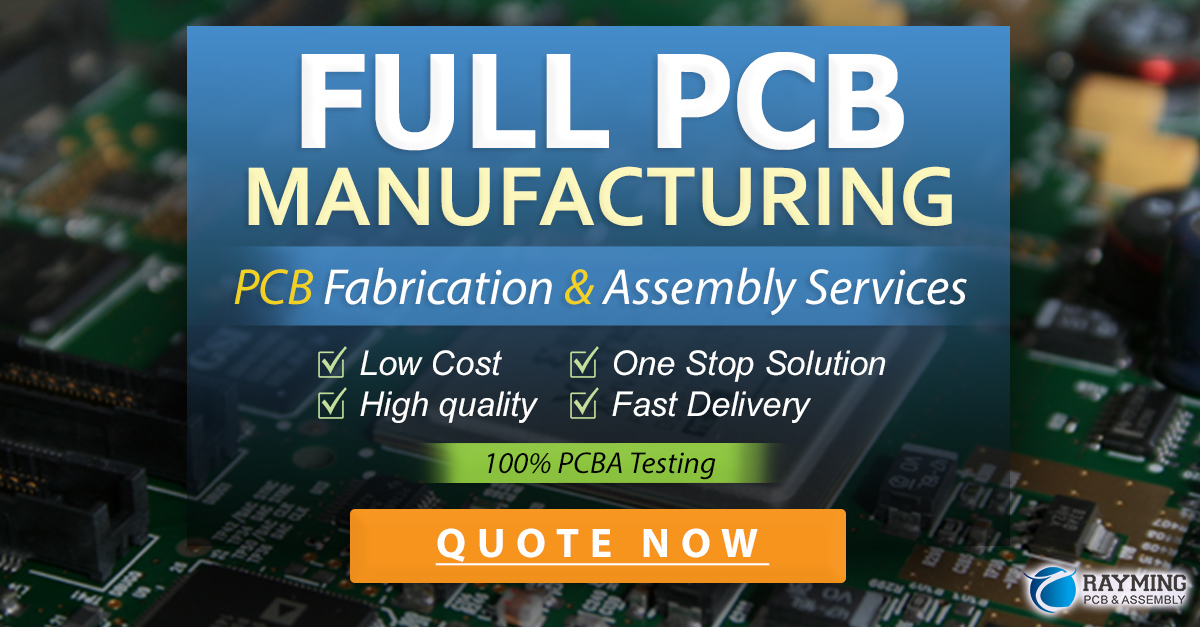
Leave a Reply