1. Delamination
Delamination is a common problem in Multilayer PCB Fabrication where the layers of the PCB separate from each other. This can happen due to a variety of reasons, such as:
- Poor adhesion between layers
- Thermal stress during the fabrication process
- Mechanical stress during the assembly process
To prevent delamination, it is important to ensure that the materials used in the fabrication process are compatible with each other and that the process parameters are optimized. This includes:
- Using the right adhesive material between layers
- Controlling the temperature and pressure during the lamination process
- Using a controlled cooling process to minimize thermal stress
Cause of Delamination | Prevention Measure |
---|---|
Poor adhesion between layers | Use the right adhesive material |
Thermal stress during fabrication | Control temperature and pressure during lamination |
Mechanical stress during assembly | Use a controlled cooling process |
How to Identify Delamination
Delamination can be identified through visual inspection or by using specialized equipment such as X-ray or ultrasonic testing. Some common signs of delamination include:
- Blistering or bubbling on the surface of the PCB
- Separation of layers at the edges of the PCB
- Cracking or warping of the PCB
If delamination is identified, the affected PCBs should be scrapped and the fabrication process should be reviewed to identify and address the root cause of the problem.
2. Copper Foil Wrinkles
Copper foil wrinkles are another common problem in multilayer PCB fabrication. This happens when the copper foil is not properly laminated to the substrate, resulting in wrinkles or folds in the copper layer. This can cause issues with signal integrity and reliability of the PCB.
To prevent copper foil wrinkles, it is important to ensure that the copper foil is properly handled and stored prior to lamination. This includes:
- Storing the copper foil in a cool, dry place
- Handling the copper foil with care to avoid creases or folds
- Using a wrinkle-free lamination process
Cause of Copper Foil Wrinkles | Prevention Measure |
---|---|
Improper handling of copper foil | Store copper foil in a cool, dry place and handle with care |
Improper lamination process | Use a wrinkle-free lamination process |
How to Identify Copper Foil Wrinkles
Copper foil wrinkles can be identified through visual inspection of the PCB. Some common signs of copper foil wrinkles include:
- Visible wrinkles or folds in the copper layer
- Inconsistent copper thickness across the PCB
- Poor adhesion between the copper layer and the substrate
If copper foil wrinkles are identified, the affected PCBs should be scrapped and the fabrication process should be reviewed to identify and address the root cause of the problem.
3. Drill Registration Issues
Drill registration issues occur when the drilled holes in the PCB do not align properly with the copper pads or other features on the board. This can cause issues with signal integrity and reliability of the PCB.
To prevent drill registration issues, it is important to ensure that the drilling process is properly calibrated and that the drill bits are in good condition. This includes:
- Using high-quality drill bits that are properly maintained
- Calibrating the drilling equipment regularly
- Using a controlled drilling process with proper feed rates and speeds
Cause of Drill Registration Issues | Prevention Measure |
---|---|
Poor quality drill bits | Use high-quality drill bits that are properly maintained |
Improperly calibrated drilling equipment | Calibrate drilling equipment regularly |
Improper drilling process | Use a controlled drilling process with proper feed rates and speeds |
How to Identify Drill Registration Issues
Drill registration issues can be identified through visual inspection of the PCB or by using specialized equipment such as X-ray or optical inspection. Some common signs of drill registration issues include:
- Misaligned holes and pads
- Oversized or undersized holes
- Incomplete or missing holes
If drill registration issues are identified, the affected PCBs should be scrapped and the fabrication process should be reviewed to identify and address the root cause of the problem.
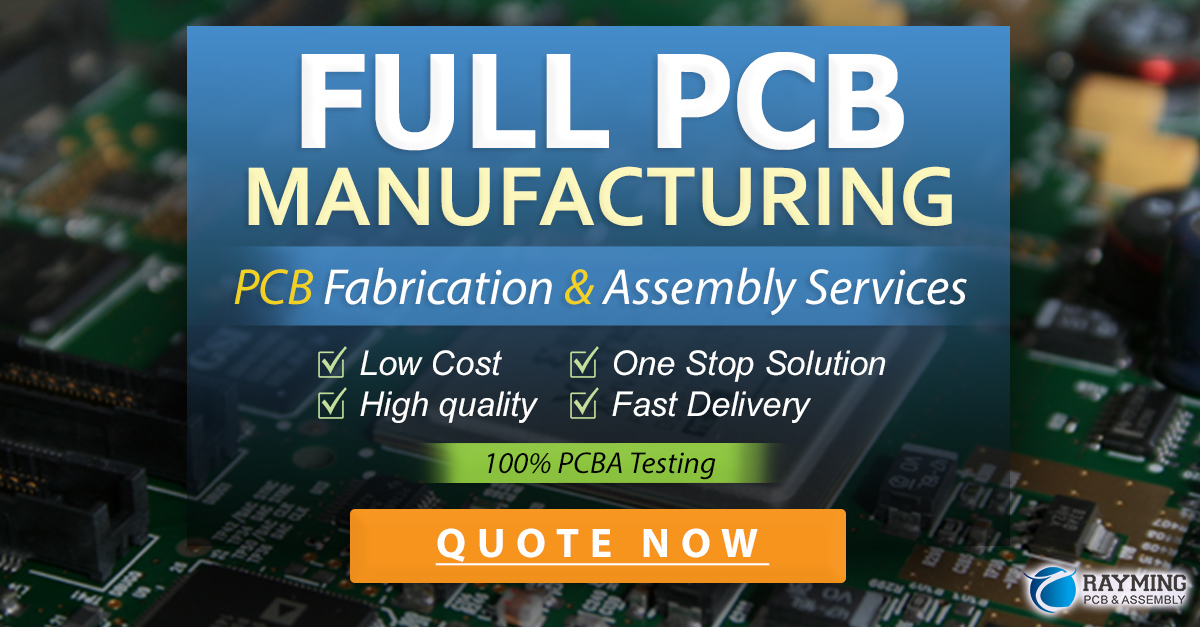
4. Solder Mask Issues
Solder mask issues can occur when the solder mask layer is not properly applied or cured during the fabrication process. This can cause issues with solderability and reliability of the PCB.
To prevent solder mask issues, it is important to ensure that the solder mask application process is properly controlled and that the solder mask material is compatible with the PCB substrate and other materials used in the fabrication process. This includes:
- Using a high-quality solder mask material that is properly stored and handled
- Applying the solder mask using a controlled process with proper thickness and coverage
- Curing the solder mask using the appropriate temperature and time settings
Cause of Solder Mask Issues | Prevention Measure |
---|---|
Poor quality solder mask material | Use high-quality solder mask material that is properly stored and handled |
Improper solder mask application process | Apply solder mask using a controlled process with proper thickness and coverage |
Improper solder mask curing process | Cure solder mask using appropriate temperature and time settings |
How to Identify Solder Mask Issues
Solder mask issues can be identified through visual inspection of the PCB. Some common signs of solder mask issues include:
- Inconsistent solder mask thickness or coverage
- Solder mask peeling or flaking
- Exposed copper or other conductive materials
If solder mask issues are identified, the affected PCBs should be scrapped and the fabrication process should be reviewed to identify and address the root cause of the problem.
5. Copper Thickness Variation
Copper thickness variation can occur when the copper plating process is not properly controlled during the fabrication process. This can cause issues with signal integrity and reliability of the PCB.
To prevent copper thickness variation, it is important to ensure that the copper plating process is properly controlled and that the plating bath is properly maintained. This includes:
- Using a high-quality copper sulfate solution that is properly filtered and maintained
- Controlling the current density and plating time to achieve the desired copper thickness
- Using a controlled rinsing and drying process to prevent contamination
Cause of Copper Thickness Variation | Prevention Measure |
---|---|
Poor quality copper sulfate solution | Use high-quality copper sulfate solution that is properly filtered and maintained |
Improper plating process | Control current density and plating time to achieve desired copper thickness |
Contamination during rinsing and drying | Use a controlled rinsing and drying process to prevent contamination |
How to Identify Copper Thickness Variation
Copper thickness variation can be identified through visual inspection of the PCB or by using specialized equipment such as X-ray fluorescence (XRF) or cross-sectional analysis. Some common signs of copper thickness variation include:
- Inconsistent copper color or appearance
- Uneven or incomplete copper coverage
- Measurable differences in copper thickness across the PCB
If copper thickness variation is identified, the affected PCBs should be scrapped and the fabrication process should be reviewed to identify and address the root cause of the problem.
6. Inadequate Etching
Inadequate etching can occur when the etching process is not properly controlled during the fabrication process. This can cause issues with signal integrity and reliability of the PCB.
To prevent inadequate etching, it is important to ensure that the etching process is properly controlled and that the etching solution is properly maintained. This includes:
- Using a high-quality etching solution that is properly filtered and maintained
- Controlling the etching time and temperature to achieve the desired etch depth and profile
- Using a controlled rinsing and drying process to prevent contamination
Cause of Inadequate Etching | Prevention Measure |
---|---|
Poor quality etching solution | Use high-quality etching solution that is properly filtered and maintained |
Improper etching process | Control etching time and temperature to achieve desired etch depth and profile |
Contamination during rinsing and drying | Use a controlled rinsing and drying process to prevent contamination |
How to Identify Inadequate Etching
Inadequate etching can be identified through visual inspection of the PCB or by using specialized equipment such as optical or scanning electron microscopy (SEM). Some common signs of inadequate etching include:
- Incomplete or inconsistent removal of copper
- Rough or irregular copper traces
- Measurable differences in etch depth or profile across the PCB
If inadequate etching is identified, the affected PCBs should be scrapped and the fabrication process should be reviewed to identify and address the root cause of the problem.
7. Contamination
Contamination can occur at various stages of the multilayer PCB fabrication process and can cause issues with signal integrity, reliability, and aesthetics of the PCB.
To prevent contamination, it is important to ensure that the fabrication environment is properly controlled and that all materials and equipment are properly cleaned and maintained. This includes:
- Using high-quality materials that are properly stored and handled to prevent contamination
- Maintaining a clean and controlled fabrication environment with proper air filtration and humidity control
- Regularly cleaning and maintaining all equipment and tools used in the fabrication process
Cause of Contamination | Prevention Measure |
---|---|
Poor quality materials | Use high-quality materials that are properly stored and handled |
Uncontrolled fabrication environment | Maintain a clean and controlled fabrication environment with proper air filtration and humidity control |
Dirty or poorly maintained equipment | Regularly clean and maintain all equipment and tools used in the fabrication process |
How to Identify Contamination
Contamination can be identified through visual inspection of the PCB or by using specialized equipment such as energy-dispersive X-ray spectroscopy (EDS) or Fourier-transform infrared spectroscopy (FTIR). Some common signs of contamination include:
- Discoloration or staining of the PCB surface
- Presence of foreign particles or debris on the PCB
- Measurable differences in chemical composition across the PCB
If contamination is identified, the affected PCBs should be scrapped and the fabrication process should be reviewed to identify and address the root cause of the problem.
FAQ
1. What is the most common problem in multilayer PCB fabrication?
The most common problem in multilayer PCB fabrication is delamination, which occurs when the layers of the PCB separate from each other due to poor adhesion, thermal stress, or mechanical stress.
2. How can I prevent copper foil wrinkles in my PCBs?
To prevent copper foil wrinkles, it is important to store the copper foil in a cool, dry place, handle it with care to avoid creases or folds, and use a wrinkle-free lamination process during fabrication.
3. What causes drill registration issues in PCBs?
Drill registration issues can be caused by poor quality drill bits, improperly calibrated drilling equipment, or an improper drilling process with incorrect feed rates and speeds.
4. How can I identify solder mask issues in my PCBs?
Solder mask issues can be identified through visual inspection of the PCB. Some common signs include inconsistent solder mask thickness or coverage, solder mask peeling or flaking, and exposed copper or other conductive materials.
5. What should I do if I identify contamination in my PCBs?
If contamination is identified, the affected PCBs should be scrapped and the fabrication process should be reviewed to identify and address the root cause of the problem. This may involve using higher quality materials, maintaining a cleaner fabrication environment, or improving equipment maintenance and cleaning procedures.
Conclusion
Multilayer PCB fabrication is a complex process that involves multiple steps and materials, and there are several common problems that can arise during the process. These problems include delamination, copper foil wrinkles, drill registration issues, solder mask issues, copper thickness variation, inadequate etching, and contamination.
To prevent these problems and ensure high-quality PCBs, it is important to use high-quality materials, maintain a controlled fabrication environment, and follow best practices for each step of the fabrication process. This includes properly storing and handling materials, using appropriate equipment and process parameters, and regularly cleaning and maintaining all equipment and tools.
By understanding these common problems and taking steps to prevent them, PCB manufacturers can improve the reliability, performance, and aesthetics of their multilayer PCBs and reduce scrap and rework costs. As technology continues to advance and PCBs become more complex, it will be increasingly important for manufacturers to stay up-to-date with best practices and continuously improve their processes to meet the evolving needs of their customers.
Leave a Reply