Challenge 1: Component Obsolescence and Shortages
One of the biggest challenges in electronics manufacturing is component obsolescence and shortages. As technology evolves rapidly, electronic components can quickly become outdated or discontinued by suppliers. This leaves manufacturers scrambling to find suitable replacements or redesign products. Component shortages due to supply chain disruptions or high demand can also cause production delays and increased costs.
Solutions:
- Proactively monitor component lifecycles and anticipate obsolescence
- Establish strong relationships with multiple suppliers to ensure alternative sourcing options
- Consider redesigning products to use more readily available components
- Implement supply chain risk management strategies to mitigate the impact of shortages
Challenge 2: Miniaturization and High Density Packaging
The trend towards miniaturization in electronic devices has led to challenges in high-density packaging. As components become smaller and more tightly packed, it becomes increasingly difficult to manufacture and assemble products reliably. Issues such as heat dissipation, signal integrity, and manufacturing tolerances become more critical.
Solutions:
- Invest in advanced manufacturing technologies such as 3D printing and micro-molding
- Use simulation and modeling tools to optimize product designs for manufacturability
- Implement stringent quality control processes to ensure consistent manufacturing results
- Collaborate closely with suppliers to ensure components meet required specifications
Challenge 3: Rapid Technological Advancements
The electronics industry is characterized by rapid technological advancements, with new products and features being introduced at an unprecedented pace. This poses challenges for manufacturers who must continuously adapt their processes and capabilities to keep up with changing customer demands and market trends.
Solutions:
- Foster a culture of innovation and continuous improvement within the organization
- Invest in research and development to stay ahead of technological curves
- Partner with technology leaders and research institutions to access cutting-edge knowledge and resources
- Implement flexible and agile manufacturing systems that can quickly adapt to new product requirements
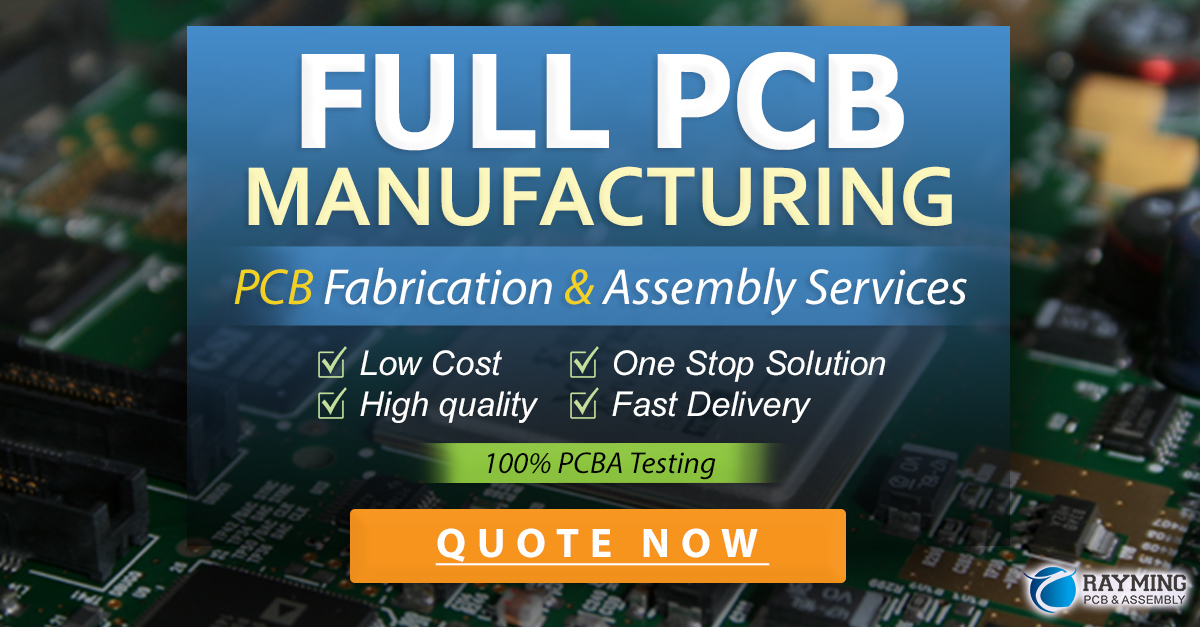
Challenge 4: Cost Pressures and Margin Erosion
Electronics manufacturers face constant cost pressures and margin erosion due to intense global competition and commoditization of products. Customers demand lower prices while expecting higher quality and functionality, putting a squeeze on manufacturer profit margins.
Solutions:
- Implement lean manufacturing principles to eliminate waste and optimize processes
- Automate processes where possible to reduce labor costs and improve efficiency
- Outsource non-core activities to lower-cost regions or specialists
- Implement value engineering and design for manufacturability to reduce product costs
Challenge 5: Quality and Reliability
Ensuring consistent quality and reliability is critical in electronics manufacturing, as even minor defects can result in product failures or safety hazards. Manufacturers must implement rigorous quality control processes throughout the entire production lifecycle.
Solutions:
- Implement Six Sigma or other quality management methodologies to reduce defects
- Use automated inspection systems to detect quality issues early in the process
- Establish strict supplier qualification and auditing processes to ensure incoming material quality
- Conduct thorough testing and burn-in to identify potential reliability issues before products are shipped
Challenge 6: Regulatory Compliance
Electronics manufacturers must navigate a complex web of regulatory compliance requirements related to product safety, environmental impact, and materials usage. Non-compliance can result in costly penalties, product recalls, and damage to brand reputation.
Solutions:
- Stay up-to-date on relevant regulations and industry standards
- Implement robust compliance management systems to track and document compliance activities
- Work closely with suppliers to ensure materials and components are compliant
- Conduct regular audits and assessments to identify and address compliance gaps
Challenge 7: Intellectual Property Protection
Intellectual property (IP) protection is a critical concern for electronics manufacturers, as product designs and technologies are easily copied or reverse-engineered by competitors. Safeguarding IP is essential to maintain competitive advantage and profitability.
Solutions:
- Implement strict access controls and confidentiality agreements for sensitive information
- Use legal protections such as patents, trademarks, and copyrights to defend IP rights
- Conduct regular IP audits to identify potential infringement or leakage
- Work with trusted partners and suppliers who have strong IP protection practices
Challenge 8: Supply Chain Complexity
Electronics manufacturing often involves complex global supply chains with numerous suppliers, contract manufacturers, and logistics providers. Managing this complexity can be challenging, particularly when dealing with issues such as lead times, quality control, and inventory management.
Solutions:
- Implement supply chain visibility and collaboration platforms to improve transparency and coordination
- Use data analytics and predictive modeling to optimize inventory levels and reduce stockouts
- Establish long-term partnerships with key suppliers to ensure reliability and flexibility
- Diversify supply base to reduce risk of disruptions or bottlenecks
Challenge 9: Skilled Labor Shortages
The electronics industry faces ongoing shortages of skilled labor, particularly in areas such as engineering, programming, and advanced manufacturing. Attracting and retaining top talent can be difficult, especially in highly competitive job markets.
Solutions:
- Partner with educational institutions to develop talent pipelines and internship programs
- Offer competitive compensation and benefits packages to attract and retain employees
- Invest in training and development programs to upskill existing workforce
- Explore automation and robotics to reduce reliance on manual labor
Challenge 10: Product Lifecycle Management
Managing product lifecycles from concept to end-of-life is a complex challenge for electronics manufacturers. Decisions around design, sourcing, manufacturing, and support must be carefully coordinated to optimize costs, quality, and time-to-market.
Solutions:
- Implement product lifecycle management (PLM) software to streamline processes and data management
- Use modular product architectures to enable faster design iterations and upgrades
- Establish cross-functional teams to coordinate activities across the product lifecycle
- Plan for product obsolescence and end-of-life support early in the design phase
Challenge 11: Counterfeit Components
The proliferation of counterfeit electronic components poses significant risks to manufacturers, including quality and reliability issues, legal liabilities, and damage to brand reputation. Detecting and preventing the use of counterfeit parts can be difficult, particularly in complex supply chains.
Solutions:
- Source components only from authorized distributors or directly from manufacturers
- Implement strict incoming inspection and testing processes to detect counterfeit parts
- Use traceability technologies such as RFID or blockchain to verify component authenticity
- Participate in industry initiatives and standards to combat counterfeiting
Challenge 12: Environmental Sustainability
Electronics manufacturers face increasing pressure to improve environmental sustainability and reduce the environmental impact of their products and processes. This includes issues such as energy efficiency, materials usage, and e-waste management.
Solutions:
- Implement eco-design principles to reduce material usage and improve recyclability
- Use renewable energy sources and energy-efficient manufacturing processes
- Establish take-back and recycling programs for end-of-life products
- Collaborate with suppliers and customers to promote sustainable practices throughout the value chain
Challenge 13: Customization and Personalization
Customers increasingly demand customized and personalized electronic products, which can be challenging for manufacturers to accommodate cost-effectively. Mass customization requires flexible manufacturing processes and supply chains that can handle high levels of variability.
Solutions:
- Implement modular product architectures that allow for easy customization
- Use 3D printing and other additive manufacturing technologies for low-volume custom parts
- Establish configure-to-order processes that allow customers to specify product options
- Partner with specialized suppliers or contract manufacturers for custom components
Challenge 14: Cybersecurity Risks
As electronic products become increasingly connected and software-driven, cybersecurity risks have become a major concern for manufacturers. Protecting products and manufacturing systems from cyber threats requires robust security measures and ongoing vigilance.
Solutions:
- Implement secure-by-design principles in product development to minimize vulnerabilities
- Use encryption, authentication, and access controls to protect sensitive data and systems
- Conduct regular cybersecurity risk assessments and penetration testing
- Establish incident response and recovery plans to minimize impact of potential breaches
Challenge 15: Global Trade Uncertainties
Electronics manufacturers often operate in a global trade environment that can be unpredictable and subject to various tariffs, regulations, and geopolitical risks. Navigating these uncertainties requires careful planning and risk management.
Solutions:
- Monitor global trade developments and assess potential impacts on operations
- Diversify manufacturing and sourcing locations to reduce reliance on any single country or region
- Use scenario planning and risk modeling to prepare for potential disruptions
- Collaborate with industry associations and policymakers to advocate for stable trade policies
Frequently Asked Questions (FAQ)
What is the biggest challenge facing electronics manufacturers today?
Component obsolescence and shortages are often cited as the biggest challenge for electronics manufacturers, as they can significantly disrupt production and increase costs. However, the specific challenges faced by manufacturers can vary depending on their products, markets, and business models.
How can electronics manufacturers ensure consistent product quality?
Ensuring consistent product quality requires a multi-faceted approach that includes:
– Implementing strict quality control processes throughout the manufacturing lifecycle
– Using automated inspection and testing systems to detect defects early
– Establishing supplier qualification and auditing processes to ensure incoming material quality
– Conducting thorough product testing and validation before release
What are some strategies for managing supply chain risks in electronics manufacturing?
Strategies for managing supply chain risks in electronics manufacturing include:
– Diversifying the supplier base to reduce reliance on any single source
– Implementing supply chain visibility and collaboration platforms to improve transparency and coordination
– Using data analytics and predictive modeling to optimize inventory levels and reduce stockouts
– Establishing long-term partnerships with key suppliers to ensure reliability and flexibility
How can electronics manufacturers attract and retain skilled talent?
To attract and retain skilled talent, electronics manufacturers can:
– Partner with educational institutions to develop talent pipelines and internship programs
– Offer competitive compensation and benefits packages to attract and retain employees
– Invest in training and development programs to upskill existing workforce
– Foster a culture of innovation and continuous learning to engage and motivate employees
What role does automation play in addressing Electronics manufacturing challenges?
Automation can play a significant role in addressing various electronics manufacturing challenges, such as:
– Reducing labor costs and improving efficiency through the use of robotics and other automated systems
– Enhancing quality control by using automated inspection and testing systems
– Enabling faster product changeovers and customization through flexible automation
– Reducing reliance on manual labor and mitigating the impact of skilled labor shortages
While the electronics manufacturing process presents numerous challenges, manufacturers can overcome these obstacles by implementing a range of strategies and solutions. By staying proactive, agile, and innovative, electronics manufacturers can navigate the dynamic and competitive landscape of the industry and deliver high-quality products to their customers.
Leave a Reply