Introduction
When it comes to protecting your printed circuit boards (PCBs) from harsh environmental conditions, applying a conformal coating is one of the most effective methods. PCB Conformal Coating is a thin layer of protective material that is applied to the surface of a PCB to shield it from moisture, dust, chemicals, and other contaminants. Choosing the right conformal coating for your PCB is crucial to ensure optimal performance and longevity. In this article, we will provide you with 12 guides to help you select the best PCB conformal coating for your specific application.
What is PCB Conformal Coating?
PCB conformal coating is a protective layer that is applied to the surface of a PCB to safeguard it from environmental factors that can cause damage or malfunction. The coating conforms to the contours of the PCB, covering all the components and exposed surfaces. Conformal coatings can be applied using various methods, such as spraying, dipping, or brushing, depending on the specific requirements of the application.
Benefits of PCB Conformal Coating
- Protection against moisture and humidity
- Resistance to chemicals and solvents
- Insulation against electrical shorts and arcing
- Enhanced mechanical strength and durability
- Improved thermal stability and heat dissipation
- Prevention of fungal and microbial growth
Types of PCB Conformal Coatings
There are several types of conformal coatings available, each with its unique properties and advantages. The most common types of PCB conformal coatings include:
1. Acrylic Conformal Coating
Acrylic conformal coatings are the most widely used type of coating in the electronics industry. They offer excellent moisture and chemical resistance, as well as good electrical insulation properties. Acrylic coatings are easy to apply and have a fast drying time, making them suitable for high-volume production.
Advantages of Acrylic Conformal Coating
- Good moisture and chemical resistance
- Excellent electrical insulation properties
- Easy to apply and fast drying
- Suitable for high-volume production
- Relatively low cost
Disadvantages of Acrylic Conformal Coating
- Limited temperature range (-40°C to +125°C)
- Prone to cracking under thermal stress
- Not suitable for high-reliability applications
2. Silicone Conformal Coating
Silicone conformal coatings offer excellent temperature stability and flexibility, making them ideal for applications that involve extreme temperatures or thermal cycling. They also provide good moisture and chemical resistance, as well as excellent electrical insulation properties.
Advantages of Silicone Conformal Coating
- Excellent temperature stability (-65°C to +200°C)
- High flexibility and resistance to cracking
- Good moisture and chemical resistance
- Excellent electrical insulation properties
- Suitable for high-reliability applications
Disadvantages of Silicone Conformal Coating
- Relatively expensive compared to other coatings
- Difficult to repair or rework
- May require longer drying time
3. Polyurethane Conformal Coating
Polyurethane conformal coatings offer a balance between the properties of acrylic and silicone coatings. They provide good moisture and chemical resistance, as well as excellent mechanical strength and abrasion resistance. Polyurethane coatings are also suitable for applications that require a high degree of flexibility.
Advantages of Polyurethane Conformal Coating
- Good moisture and chemical resistance
- Excellent mechanical strength and abrasion resistance
- High flexibility and resistance to cracking
- Suitable for applications that require a tough, durable coating
Disadvantages of Polyurethane Conformal Coating
- Limited temperature range (-40°C to +125°C)
- May require longer drying time compared to acrylic coatings
- Can be difficult to remove or rework
4. Epoxy Conformal Coating
Epoxy conformal coatings offer excellent chemical and abrasion resistance, as well as high mechanical strength and durability. They are ideal for applications that require a high degree of protection against harsh environmental conditions. However, epoxy coatings are relatively brittle and may crack under thermal stress.
Advantages of Epoxy Conformal Coating
- Excellent chemical and abrasion resistance
- High mechanical strength and durability
- Good electrical insulation properties
- Suitable for applications that require a high degree of protection
Disadvantages of Epoxy Conformal Coating
- Brittle and prone to cracking under thermal stress
- Limited temperature range (-40°C to +150°C)
- Difficult to remove or rework
- Relatively expensive compared to other coatings
5. Parylene Conformal Coating
Parylene conformal coatings are deposited using a vapor deposition process, resulting in a thin, uniform, and pinhole-free coating. They offer excellent moisture and chemical resistance, as well as superior electrical insulation properties. Parylene coatings are also biocompatible and suitable for medical applications.
Advantages of Parylene Conformal Coating
- Excellent moisture and chemical resistance
- Superior electrical insulation properties
- Thin, uniform, and pinhole-free coating
- Biocompatible and suitable for medical applications
- High temperature stability (-200°C to +200°C)
Disadvantages of Parylene Conformal Coating
- Expensive compared to other coating types
- Requires specialized equipment for application
- Difficult to repair or rework
- May not be suitable for high-volume production
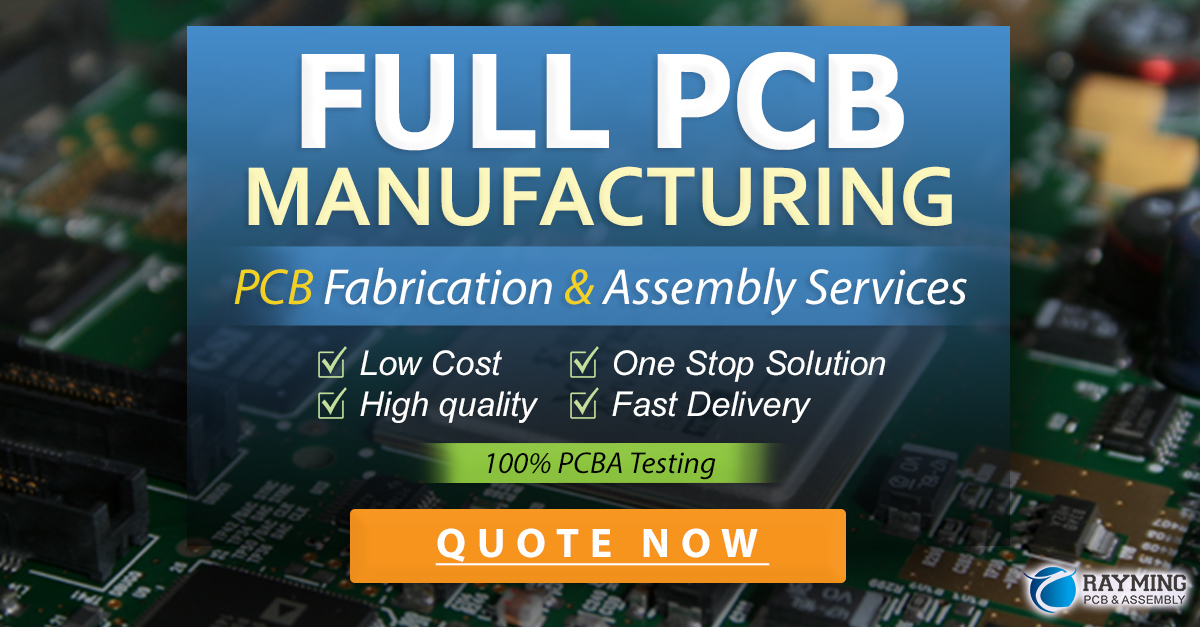
Factors to Consider When Choosing a PCB Conformal Coating
When selecting a PCB conformal coating, there are several factors to consider to ensure that you choose the most suitable coating for your specific application. These factors include:
1. Environmental Conditions
Consider the environmental conditions that your PCB will be exposed to, such as temperature, humidity, chemicals, and abrasion. Choose a coating that offers adequate protection against these conditions.
2. Electrical Requirements
Evaluate the electrical requirements of your PCB, such as insulation resistance, dielectric strength, and capacitance. Select a coating that meets or exceeds these requirements.
3. Mechanical Properties
Consider the mechanical properties of the coating, such as flexibility, hardness, and abrasion resistance. Choose a coating that provides the necessary mechanical protection for your application.
4. Application Method
Determine the most suitable application method for your PCB, such as spraying, dipping, or brushing. Consider factors such as coating thickness, uniformity, and ease of application.
5. Reworkability
Assess the ease of reworking or repairing the coated PCB, if necessary. Some coatings, such as silicone and epoxy, can be difficult to remove or rework.
6. Cost
Evaluate the cost of the conformal coating, including material, application, and processing costs. Choose a coating that offers the best balance between performance and cost for your specific application.
PCB Conformal Coating Selection Guide
To help you choose the right PCB conformal coating for your application, we have created a selection guide based on the most common environmental conditions and requirements.
Environmental Condition | Recommended Coating |
---|---|
High humidity | Acrylic, Silicone, Polyurethane, Epoxy, Parylene |
High temperature | Silicone, Polyurethane, Epoxy, Parylene |
Chemical exposure | Epoxy, Parylene |
Abrasion resistance | Polyurethane, Epoxy |
Electrical insulation | Acrylic, Silicone, Polyurethane, Epoxy, Parylene |
Flexibility | Silicone, Polyurethane |
Biocompatibility | Parylene |
PCB Conformal Coating Application Methods
There are several methods for applying conformal coatings to PCBs, each with its advantages and disadvantages. The most common application methods include:
1. Spraying
Spraying is the most common method for applying conformal coatings to PCBs. It offers good control over coating thickness and uniformity, and is suitable for high-volume production. However, spraying may result in overspray and requires masking of areas that do not require coating.
2. Dipping
Dipping involves immersing the PCB in a tank of conformal coating material, allowing the coating to adhere to the surface. This method ensures complete coverage of the PCB, but may result in excess coating on the edges and requires longer drying time.
3. Brushing
Brushing is a manual method of applying conformal coatings, suitable for small-scale production or touch-up work. It offers good control over coating thickness and coverage but may result in inconsistent finish and requires skilled operators.
4. Selective Coating
Selective coating involves applying the conformal coating only to specific areas of the PCB, using automated dispensing equipment. This method minimizes the amount of coating used and reduces the need for masking, but requires specialized equipment and programming.
PCB Conformal Coating Inspection and Testing
After applying the conformal coating, it is essential to inspect and test the PCB to ensure that the coating meets the required specifications and provides adequate protection. Some common inspection and testing methods include:
1. Visual Inspection
Visual inspection involves examining the coated PCB under magnification to check for defects such as pinholes, bubbles, or uneven coverage. This method is quick and easy but may not detect all defects.
2. Thickness Measurement
Thickness measurement involves using a thickness gauge or microscope to measure the thickness of the conformal coating at various points on the PCB. This method ensures that the coating meets the specified thickness requirements.
3. Adhesion Testing
Adhesion testing involves applying a tape or scratch test to the coated PCB to assess the adhesion of the coating to the surface. This method ensures that the coating will not delaminate or peel off during use.
4. Electrical Testing
Electrical testing involves measuring the insulation resistance, dielectric strength, and other electrical properties of the coated PCB to ensure that the coating provides adequate electrical insulation and does not affect the performance of the circuit.
Frequently Asked Questions (FAQ)
-
Q: How long does PCB conformal coating last?
A: The lifespan of a PCB conformal coating depends on various factors, such as the type of coating, environmental conditions, and application method. Generally, conformal coatings can last several years or even decades, provided they are applied correctly and the PCB is not subjected to extreme conditions. -
Q: Can PCB conformal coatings be removed?
A: Yes, most PCB conformal coatings can be removed using specific solvents or mechanical methods, such as scraping or abrasion. However, some coatings, such as silicone and epoxy, can be difficult to remove and may require specialized equipment or chemicals. -
Q: How do I choose the right thickness for my PCB conformal coating?
A: The thickness of the conformal coating depends on the specific requirements of your application, such as the level of protection needed and the environmental conditions. Generally, a thickness of 25-75 microns (1-3 mils) is recommended for most applications. Consult the coating manufacturer’s guidelines or conduct testing to determine the optimal thickness for your PCB. -
Q: Can PCB conformal coatings be applied over components?
A: Yes, conformal coatings can be applied over components, such as resistors, capacitors, and integrated circuits. However, it is essential to ensure that the coating does not interfere with the functionality of the components or cause any adverse effects, such as thermal insulation or capacitance changes. -
Q: How do I choose between acrylic and silicone conformal coatings?
A: The choice between acrylic and silicone conformal coatings depends on the specific requirements of your application. Acrylic coatings are suitable for applications that require good moisture and chemical resistance, as well as ease of application and removal. Silicone coatings are ideal for applications that involve extreme temperatures or thermal cycling, as well as high flexibility and resistance to cracking. Consider the environmental conditions, electrical requirements, and mechanical properties when making your decision.
Conclusion
Choosing the right PCB conformal coating is crucial to ensure the long-term reliability and performance of your electronic devices. By considering factors such as environmental conditions, electrical requirements, mechanical properties, and application methods, you can select the most suitable coating for your specific application. This article has provided you with 12 guides to help you make an informed decision when choosing a PCB conformal coating. Remember to always follow the manufacturer’s guidelines and conduct thorough testing to ensure that the coating meets your requirements and provides adequate protection for your PCB.
Leave a Reply