Introduction to PCB Tools
PCB (printed circuit board) tools are essential for designing, programming, and testing electronic circuits. With the rapid advancements in technology, PCB tools have evolved to become more sophisticated, efficient, and user-friendly. In this article, we will explore 11 crucial aspects of PCB programming and testing tools that every electronics engineer and enthusiast should know.
1. PCB Design Software
PCB design software is the foundation of any PCB project. These tools allow engineers to create schematic diagrams, design PCB layouts, and generate manufacturing files. Popular PCB design software includes:
Software | Manufacturer | Key Features |
---|---|---|
Altium Designer | Altium | Comprehensive PCB design suite, 3D modeling, MCAD integration |
Eagle | Autodesk | User-friendly interface, extensive component libraries, affordable |
KiCad | Open Source | Free, cross-platform, growing community support |
OrCAD | Cadence | Powerful simulation tools, constraint-driven design, FPGA integration |
2. Schematic Capture
Schematic capture is the process of creating a graphical representation of an electronic circuit. It involves placing components, connecting them with wires, and adding labels and annotations. Key considerations for schematic capture include:
- Using consistent and clear naming conventions
- Organizing the schematic into logical sections
- Applying design rules and constraints
- Documenting the circuit thoroughly
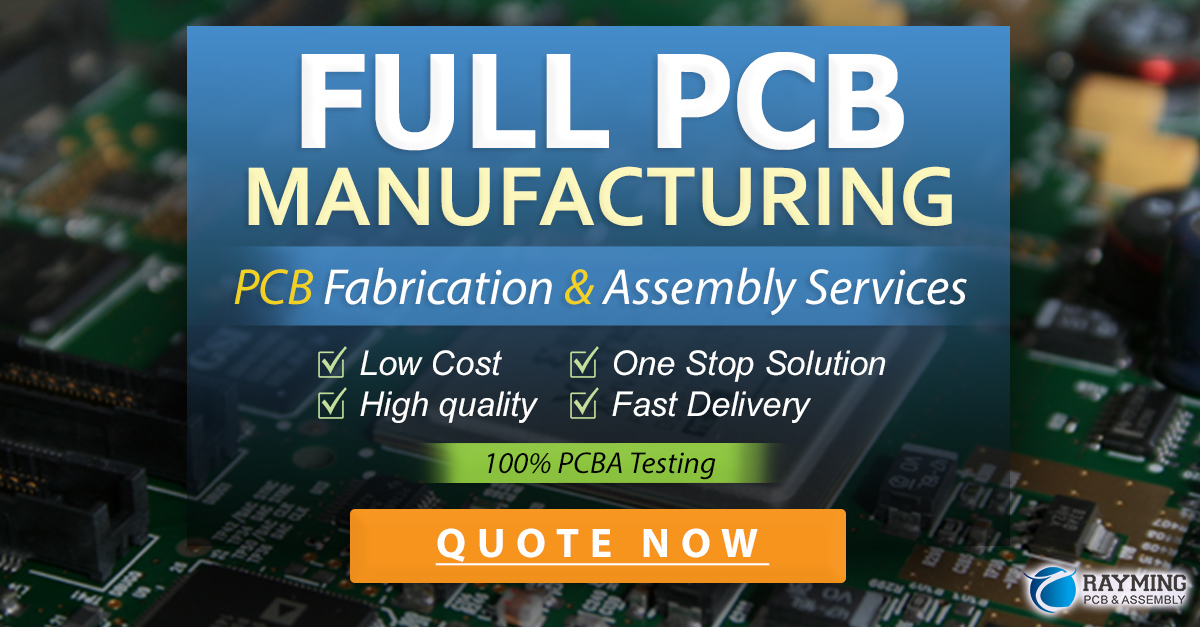
3. PCB Layout Design
PCB layout design involves translating the schematic into a physical board layout. This process requires careful consideration of factors such as component placement, routing, signal integrity, and manufacturability. Important aspects of PCB layout design include:
- Defining the board stackup and layer arrangement
- Placing components for optimal signal flow and thermal management
- Routing traces while minimizing crosstalk and electromagnetic interference
- Applying design for manufacturing (DFM) guidelines
4. Design Rule Checking (DRC)
Design rule checking (DRC) is an automated process that verifies the PCB layout against a set of predefined design rules. These rules ensure that the board meets manufacturing and reliability standards. Common design rules include:
- Minimum trace width and spacing
- Pad and via sizes and clearances
- Copper pour and thermal relief settings
- Silkscreen and solder mask clearances
5. Gerber File Generation
Gerber files are the industry standard for PCB manufacturing. They contain all the necessary information for fabricating the PCB, including copper layers, solder mask, silkscreen, and drill data. When generating Gerber files, consider the following:
- Use the latest Gerber format (RS-274X)
- Include all required layers and files
- Verify the Gerber files using a Gerber viewer
- Communicate any special requirements to the manufacturer
6. PCB Assembly and Soldering
PCB assembly involves placing and soldering components onto the fabricated PCB. This process can be done manually or using automated equipment. Key factors in PCB assembly include:
- Choosing the appropriate soldering technique (reflow, wave, hand)
- Selecting the right solder paste and stencil design
- Ensuring proper component orientation and polarity
- Inspecting the assembled board for defects
7. In-Circuit Testing (ICT)
In-circuit testing (ICT) is a method of verifying the presence, orientation, and functionality of components on an assembled PCB. ICT uses a bed-of-nails fixture to make electrical contact with test points on the board. Benefits of ICT include:
- Detecting component placement and soldering issues
- Verifying component values and tolerances
- Identifying short circuits and open connections
- Providing comprehensive test coverage
8. Flying Probe Testing
Flying probe testing is an alternative to ICT that uses movable probes to make electrical contact with test points on the PCB. Flying probe testers offer several advantages:
- No need for custom test fixtures
- Ability to test both sides of the board
- Flexibility to adapt to design changes
- Lower setup costs for low-volume production
9. Boundary Scan Testing (JTAG)
Boundary scan testing, also known as JTAG (Joint Test Action Group), is a method of testing digital circuits by accessing and controlling the input/output pins of integrated circuits (ICs). JTAG testing offers the following benefits:
- Testing complex digital circuits with limited physical access
- Verifying connectivity between ICs
- Programming and debugging FPGA and CPLD devices
- Enabling remote diagnostics and firmware updates
10. Functional Testing
Functional testing involves verifying the overall functionality of the assembled PCB by simulating real-world operating conditions. This type of testing typically requires custom test fixtures and software. Key aspects of functional testing include:
- Developing comprehensive test cases and procedures
- Designing and building test fixtures
- Automating tests for repeatability and efficiency
- Analyzing test results and identifying root causes of failures
11. Automated Optical Inspection (AOI)
Automated optical inspection (AOI) is a non-contact method of inspecting assembled PCBs using high-resolution cameras and image processing algorithms. AOI systems can detect a wide range of defects, such as:
- Component placement errors
- Solder joint defects (bridging, insufficient solder, etc.)
- Missing or incorrect components
- Solder paste printing issues
AOI offers high-speed inspection, objective results, and the ability to catch defects early in the production process.
Frequently Asked Questions (FAQ)
Q1: What is the difference between PCB design software and schematic capture tools?
A1: PCB design software typically includes both schematic capture and PCB layout capabilities, while schematic capture tools focus solely on creating and editing schematic diagrams.
Q2: Why is design rule checking (DRC) important in PCB layout design?
A2: DRC ensures that the PCB layout adheres to manufacturing and reliability standards, reducing the risk of production issues and improving the overall quality of the final product.
Q3: What are Gerber files, and why are they essential for PCB manufacturing?
A3: Gerber files are the industry standard for conveying PCB design information to manufacturers. They contain all the necessary data for fabricating the PCB, including copper layers, solder mask, silkscreen, and drill data.
Q4: What are the advantages of using flying probe testing compared to in-circuit testing (ICT)?
A4: Flying probe testing offers flexibility, as it does not require custom test fixtures. It can also test both sides of the board and adapt easily to design changes. However, flying probe testing is generally slower than ICT.
Q5: How does automated optical inspection (AOI) improve the PCB assembly process?
A5: AOI systems can quickly and objectively detect a wide range of assembly defects, such as component placement errors, solder joint issues, and missing or incorrect components. By catching defects early, AOI helps reduce rework costs and improve overall product quality.
Conclusion
PCB programming and testing tools are essential for designing, manufacturing, and verifying the functionality of electronic circuits. From PCB design software and schematic capture to in-circuit testing and automated optical inspection, these tools play a crucial role in ensuring the quality and reliability of PCBs.
By understanding the key aspects of PCB tools, engineers and enthusiasts can make informed decisions when selecting and using these tools in their projects. As technology continues to advance, PCB programming and testing tools will undoubtedly evolve, offering even more capabilities and efficiencies in the future.
[Word count: 1068]
Leave a Reply