Step 1: Maintain Proper Solder Paste Printing
One of the primary causes of solder balls is improper solder paste printing. Ensuring that the solder paste is applied evenly and accurately onto the PCB pads is essential to prevent solder ball formation. To achieve this, consider the following factors:
Stencil Design
- Use a well-designed stencil with the appropriate aperture size and shape for your specific components and PCB layout.
- Ensure that the stencil thickness is suitable for the solder paste type and the required deposit volume.
- Regularly inspect and clean the stencil to prevent clogging and maintain consistent solder paste deposition.
Printer Settings
- Optimize the printer settings, such as print speed, pressure, and separation speed, to achieve a clean and precise solder paste print.
- Conduct regular maintenance and calibration of the printer to ensure consistent performance.
Solder Paste Properties
- Select a high-quality solder paste with the appropriate particle size, flux type, and rheological properties for your application.
- Store the solder paste under the recommended conditions (temperature and humidity) to maintain its integrity and prevent degradation.
Step 2: Control Reflow Oven Parameters
The reflow soldering process plays a critical role in the formation of solder balls. To minimize their occurrence, it is essential to control the reflow oven parameters accurately:
Temperature Profile
- Develop and implement an optimal reflow temperature profile that suits your specific PCB assembly and components.
- Ensure that the peak temperature, time above liquidus (TAL), and cooling rate are within the recommended range for the solder paste and components used.
Oven Maintenance
- Regularly clean and maintain the reflow oven to ensure consistent heat distribution and minimize contamination.
- Monitor the oven’s performance using profiling tools and make necessary adjustments to maintain the desired temperature profile.
Nitrogen Environment
- Consider using a nitrogen-based reflow environment to reduce oxidation and improve solder joint quality.
- Adjust the nitrogen flow rate and purity to optimize its effectiveness in preventing solder ball formation.
Step 3: Ensure Proper Component Placement
Accurate component placement is crucial to avoid solder balls caused by misalignment or shifting during the reflow process:
Pick-and-Place Machine Accuracy
- Invest in a high-precision pick-and-place machine that can consistently place components with minimal deviation from their intended positions.
- Regularly calibrate and maintain the machine to ensure its accuracy and reliability.
Component Packaging
- Use high-quality component packaging, such as tape-and-reel or matrix trays, to minimize component damage and ensure consistent feeding into the pick-and-place machine.
- Properly store and handle components to prevent contamination, moisture absorption, or mechanical damage that can lead to placement issues.
Placement Verification
- Implement automated optical inspection (AOI) or visual inspection systems to verify component placement accuracy before the reflow process.
- Identify and correct any placement errors or component shifts to prevent solder ball formation during reflow.
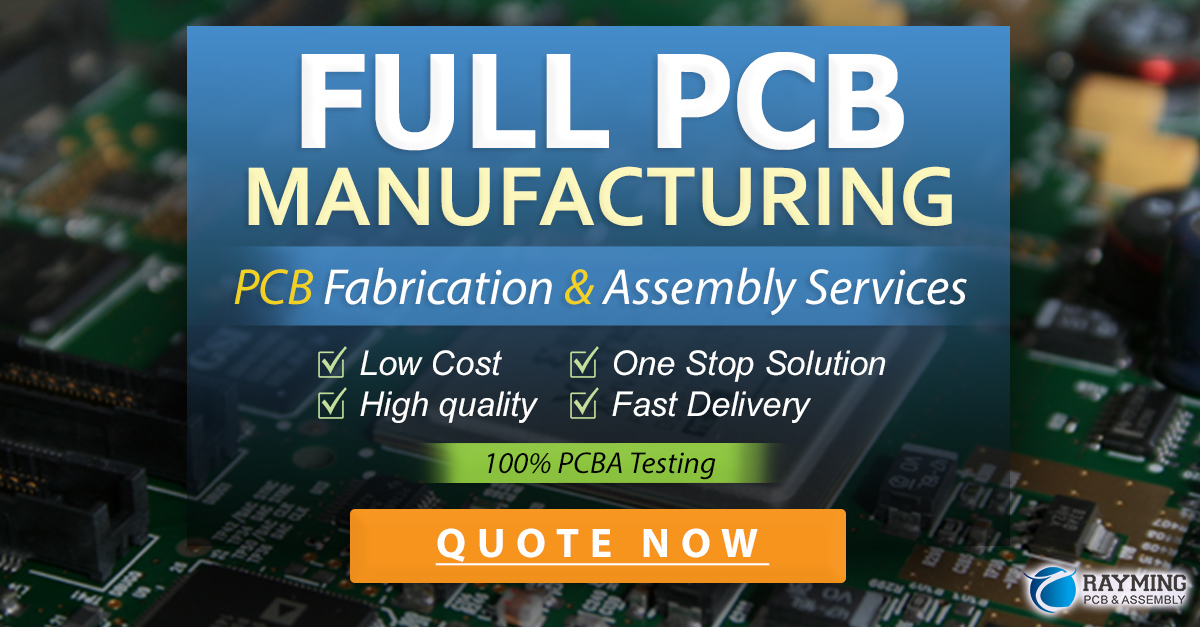
Step 4: Optimize PCB Design
A well-designed PCB layout can significantly reduce the risk of solder ball formation:
Pad Design
- Ensure that the PCB pads are designed with the appropriate size, shape, and spacing for the specific components used.
- Follow the component manufacturer’s recommendations for pad dimensions and solder mask openings to ensure proper solder joint formation.
Solder Mask
- Use a high-quality solder mask with good registration accuracy and adequate coverage to prevent solder bridging and solder ball formation.
- Ensure that the solder mask openings are slightly larger than the PCB pads to accommodate solder wetting and prevent solder ball spillover.
Copper Balancing
- Implement copper balancing techniques, such as thieving pads or copper fills, to ensure even heat distribution during the reflow process and minimize localized hot spots that can cause solder balling.
Step 5: Manage Moisture Sensitivity
Moisture absorption by PCBs and components can lead to solder ball formation during reflow:
Moisture Sensitivity Level (MSL)
- Understand and adhere to the moisture sensitivity level (MSL) ratings of the components used in your assembly.
- Follow the recommended storage, handling, and baking procedures for each MSL rating to prevent moisture-induced defects.
Dry Storage
- Store moisture-sensitive components and PCBs in a dry, controlled environment (such as a nitrogen cabinet or desiccant cabinet) to minimize moisture absorption.
- Use moisture barrier bags (MBBs) with desiccants to package and protect moisture-sensitive items during storage and transportation.
Pre-Bake
- Perform pre-baking of moisture-sensitive components and PCBs according to their MSL ratings and the manufacturer’s recommendations before assembly.
- Ensure that the pre-baking process is carried out at the appropriate temperature and duration to effectively remove absorbed moisture.
Step 6: Control Contamination
Contamination on PCBs or components can interfere with solder wetting and lead to solder ball formation:
Cleanliness
- Maintain a clean manufacturing environment to minimize the presence of dust, dirt, and other contaminants that can affect solder joint quality.
- Regularly clean and inspect the production equipment, tools, and surfaces to prevent the buildup of contaminants.
Handling Procedures
- Implement proper handling procedures, such as using gloves, tweezers, or vacuum pens, to minimize direct contact with PCBs and components.
- Train production staff on the importance of cleanliness and proper handling techniques to prevent contamination.
Flux Selection
- Choose a compatible and effective flux for your solder paste that can adequately remove oxides and promote solder wetting.
- Ensure that the flux residues are non-corrosive and do not contribute to solder ball formation or other defects.
Step 7: Optimize Stencil Cleaning
Proper stencil cleaning is essential to maintain consistent solder paste printing and prevent solder ball formation:
Cleaning Frequency
- Determine the optimal cleaning frequency based on the solder paste type, printing volume, and stencil design.
- Regularly clean the stencil, both underside and topside, to remove solder paste residue and prevent aperture clogging.
Cleaning Methods
- Use appropriate cleaning methods, such as manual wiping, automated under-stencil cleaning, or ultrasonic cleaning, depending on the severity of the residue and the stencil design.
- Select cleaning solvents that are compatible with the solder paste and the stencil material to ensure effective cleaning without damaging the stencil.
Stencil Inspection
- Visually inspect the stencil after cleaning to verify that all apertures are clear and free from residue.
- Use a microscope or automated stencil inspection system to detect any remaining contamination or damage that may affect printing quality.
Step 8: Implement Process Controls
Implementing robust process controls can help identify and prevent solder ball formation in real-time:
Statistical Process Control (SPC)
- Use statistical process control (SPC) techniques to monitor and analyze key process parameters, such as solder paste print volume, reflow temperature, and component placement accuracy.
- Set up control charts and define appropriate control limits to detect process variations and take corrective actions promptly.
Traceability
- Implement a traceability system that links raw materials, process parameters, and inspection data to individual PCB assemblies.
- Use this data to identify trends, root causes, and corrective actions for solder ball issues, enabling continuous process improvement.
Operator Training
- Provide comprehensive training to production staff on SMT manufacturing best practices, solder ball prevention techniques, and process control procedures.
- Regularly update and reinforce this training to ensure that operators are equipped with the knowledge and skills to maintain high-quality production.
Step 9: Conduct Regular Inspections
Regular inspections at various stages of the SMT manufacturing process can help detect and prevent solder ball formation:
Solder Paste Inspection (SPI)
- Implement solder paste inspection (SPI) systems to verify the quality of solder paste printing, including deposit volume, shape, and alignment.
- Use SPI data to identify any print-related issues that may lead to solder ball formation and take corrective actions.
Automated Optical Inspection (AOI)
- Utilize automated optical inspection (AOI) systems to detect component placement errors, solder bridges, and solder balls after the reflow process.
- Set up appropriate inspection parameters and train the AOI system to accurately identify solder ball defects.
X-Ray Inspection
- Use X-ray inspection for hidden or obscured solder joints, such as those in ball grid array (BGA) or quad-flat no-lead (QFN) packages.
- Identify solder ball formation, voiding, or other defects that may not be visible through optical inspection methods.
Step 10: Perform Root Cause Analysis
When solder ball issues occur, it is crucial to perform a thorough root cause analysis to identify and address the underlying problems:
Failure Analysis
- Conduct a detailed failure analysis of the affected PCB assemblies, including visual inspection, cross-sectioning, and scanning electron microscopy (SEM) analysis.
- Identify the specific location, size, and distribution of solder balls to help narrow down the potential causes.
Process Data Review
- Review the process data collected through SPC, traceability, and inspection systems to identify any correlations or trends related to solder ball formation.
- Analyze the data to determine if the issue is related to a specific material, machine, operator, or process parameter.
Corrective Action Implementation
- Based on the root cause analysis findings, develop and implement targeted corrective actions to address the identified issues.
- Monitor the effectiveness of these actions through ongoing process controls and inspections to ensure that the solder ball problem is resolved.
Step 11: Foster Continuous Improvement
Continuously improving your SMT manufacturing process is essential to minimize solder ball formation and enhance overall product quality:
Best Practice Sharing
- Encourage the sharing of best practices and lessons learned among production staff, engineering teams, and quality personnel.
- Facilitate regular meetings or forums to discuss solder ball prevention techniques, process improvements, and new technologies.
Benchmarking
- Benchmark your SMT manufacturing process against industry standards and leading competitors to identify areas for improvement.
- Attend industry conferences, workshops, and exhibitions to stay updated on the latest trends, technologies, and best practices in solder ball prevention.
Continuous Training
- Invest in continuous training and education for your SMT manufacturing staff to keep them informed about the latest techniques, materials, and equipment related to solder ball prevention.
- Foster a culture of learning and improvement that encourages employees to actively participate in problem-solving and process optimization.
By implementing these 11 easy steps, you can significantly reduce the occurrence of solder balls in your SMT manufacturing process, resulting in higher-quality products, increased productivity, and improved customer satisfaction. Remember that solder ball prevention is an ongoing effort that requires continuous monitoring, analysis, and improvement to ensure the long-term success of your SMT manufacturing operation.
FAQ
-
What are solder balls, and why are they a concern in SMT manufacturing?
Solder balls are small, spherical particles of solder that form on the surface of PCBs or components during the reflow soldering process. They can cause short circuits, bridging, and other issues that compromise the reliability and functionality of electronic assemblies. -
What are the main causes of solder ball formation?
The main causes of solder ball formation include improper solder paste printing, incorrect reflow oven parameters, component placement issues, PCB design deficiencies, moisture absorption, contamination, and inadequate stencil cleaning. -
How can I ensure proper solder paste printing to prevent solder balls?
To ensure proper solder paste printing, use a well-designed stencil, optimize printer settings, select a high-quality solder paste, and maintain consistent solder paste deposition through regular stencil inspection and cleaning. -
What role does the reflow soldering process play in solder ball formation?
The reflow soldering process is critical in solder ball formation. Incorrect temperature profiles, inadequate oven maintenance, and improper cooling rates can all contribute to solder balling. Implementing an optimal reflow profile and using a nitrogen environment can help minimize solder ball occurrence. -
How can I identify and address solder ball issues in my SMT manufacturing process?
To identify and address solder ball issues, conduct regular inspections using SPI, AOI, and X-ray systems. Perform thorough root cause analysis, including failure analysis and process data review, to identify the underlying problems. Implement targeted corrective actions and continuously monitor and improve your process to prevent future solder ball formation.
Inspection Method | Purpose | Benefits |
---|---|---|
Solder Paste Inspection (SPI) | Verify solder paste print quality | Identifies print-related issues that may lead to solder balls |
Automated Optical Inspection (AOI) | Detect component placement errors, solder bridges, and solder balls | Identifies solder ball defects after the reflow process |
X-Ray Inspection | Inspect hidden or obscured solder joints | Identifies solder ball formation, voiding, or other defects not visible through optical inspection |
By following these 11 easy steps and continuously monitoring and improving your SMT manufacturing process, you can effectively avoid solder ball formation and ensure the production of high-quality, reliable electronic assemblies.
Leave a Reply