Introduction
Flexible printed circuit boards (PCBs) have become increasingly popular in recent years due to their ability to bend and flex to fit within tight spaces. 10 layer flexible PCBs take this technology even further, providing more layers for increased circuit complexity while still maintaining flexibility.
In this comprehensive guide, we’ll explore what 10 layer flexible PCBs are, their benefits and applications, design considerations, manufacturing processes, and frequently asked questions. Whether you’re new to flex PCBs or looking to utilize them in your next project, this article covers everything you need to know about these advanced circuit boards.
What are 10 Layer Flexible PCBs?
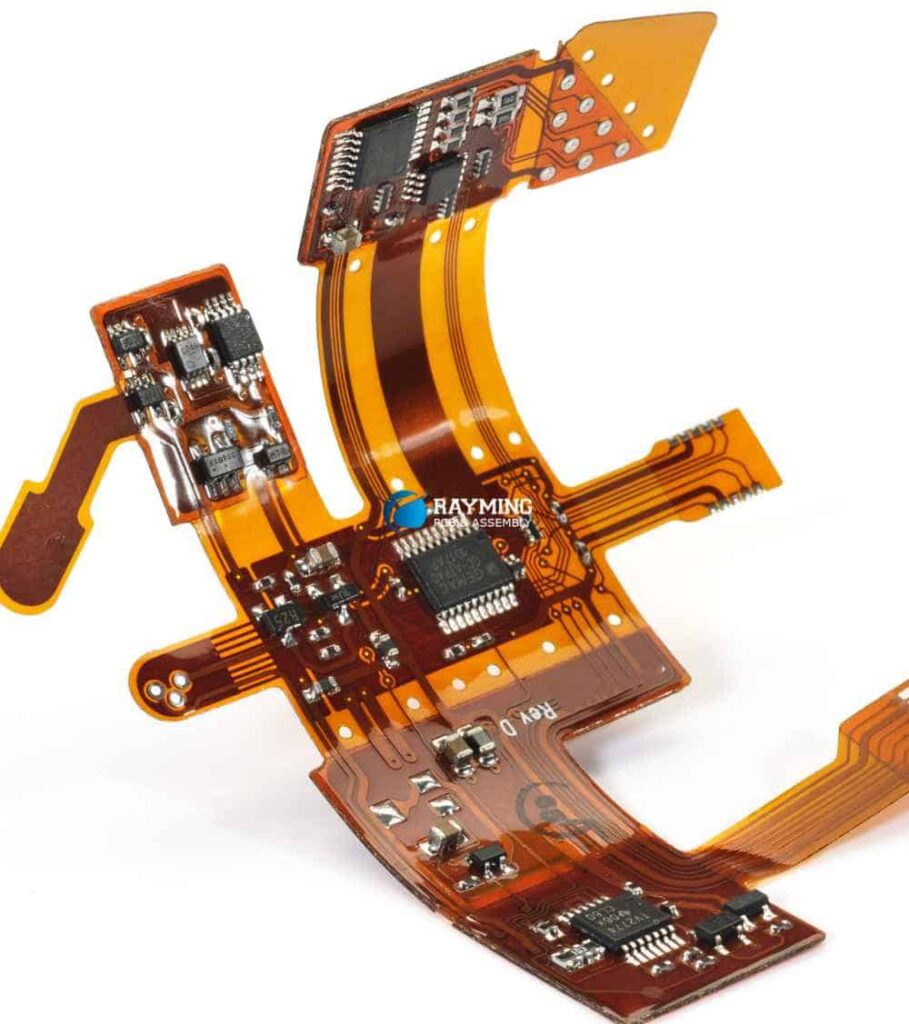
A flexible PCB is a type of printed circuit board that utilizes flexible substrate materials such as polyimide or polyester rather than traditional rigid FR-4 laminates. This allows the board to bend and flex without damage to the copper traces.
10 layer flex PCBs have 10 conductive copper layers interleaved with 11 layers of flexible dielectric material. The increased number of layers provides more space for complex circuit routing while maintaining a thin vertical profile. Components can be mounted on the outer layers, and vias can connect between layers.
Some key benefits of 10 layer flex PCBs:
- Extremely compact and thin – 10 layers in a 0.30mm profile
- High component density with small features and spacing
- Complex routing capabilities with 10 routing layers
- Flexibility allows bending, folding, and embedding
- Lightweight and durable with flex materials
- Well suited for space-constrained applications
10 layer flex PCBs strike an optimal balance of complexity, density, and flexibility for advanced circuits. Let’s look at some of the most common applications that utilize them.
Applications of 10 Layer Flex PCBs
Wearable Electronics
Wearable devices like smart watches, fitness trackers, and head mounted displays require dense, lightweight PCBs that can conform to the human body. 10 layer flexible PCBs allow these devices to package more functionality into a small flexible form factor. The flex PCB can curve around the wrist or bend to fit into glasses or headbands.
Medical Devices
Many medical devices such as hearing aids and implantable devices need to meet strict space and flexibility requirements. A 10 layer flex PCB can integrate advanced healthcare circuits while fitting into tiny spaces and bending to accommodate dynamic human movement and tissues.
Consumer Electronics
Foldable smartphones, laptops, and other devices leverage flexible PCBs like 10 layer flex to interconnect components while allowing repeated bending and folding. The flex PCB folds neatly to enable the compact folded state.
Automotive Electronics
Automotive camera modules, sensors, interior electronics, and lighting applications can benefit from flexible PCBs. 10 layer flex allows high density circuits to be integrated into areas with limited space that require dynamic movement and vibration resistance.
Robotics
Robots and drones that move and flex require interconnections that can withstand repeated bending. 10 layer flex PCBs provide reliable connectivity and dense circuit integration suitable for complex robotic systems.
Leave a Reply