Introduction
Printed circuit boards (PCBs) are an essential component in most modern electronic devices and equipment. They provide the mechanical support and electrical connections between electronic components. While rigid PCBs are still commonly used, flexible PCBs (flex PCBs) offer many advantages in certain applications and continue to grow in popularity. One type of flex PCB in particular has been gaining traction – the all-flex PCB.
All-flex PCBs provide the ultimate in flexibility and durability for demanding applications. In this article, we’ll explore what sets all-flex PCBs apart and the benefits they can provide for reliability and performance. We’ll cover topics including:
What Are All-Flex PCBs?
- Definition and construction
- How they differ from rigid-flex PCBs
- Ideal applications
Key Benefits of All-Flex PCBs
- Increased reliability
- Dynamic flexing and shape changing abilities
- Lightweight and thinner profiles
- Enhanced heat dissipation
- Improved impedance control
Design Considerations for All-Flex PCBs
- Materials selection
- Trace routing
- Component mounting
- Providing proper support
Real-World Applications of All-Flex PCBs
- Wearable technology
- Internet of Things (IoT) devices
- Robotics and drones
- Automotive electronics
By the end, you’ll understand what sets all-flex PCBs apart and how they can enhance reliability and performance in your next design. Let’s get started!
What Are All-Flex PCBs?
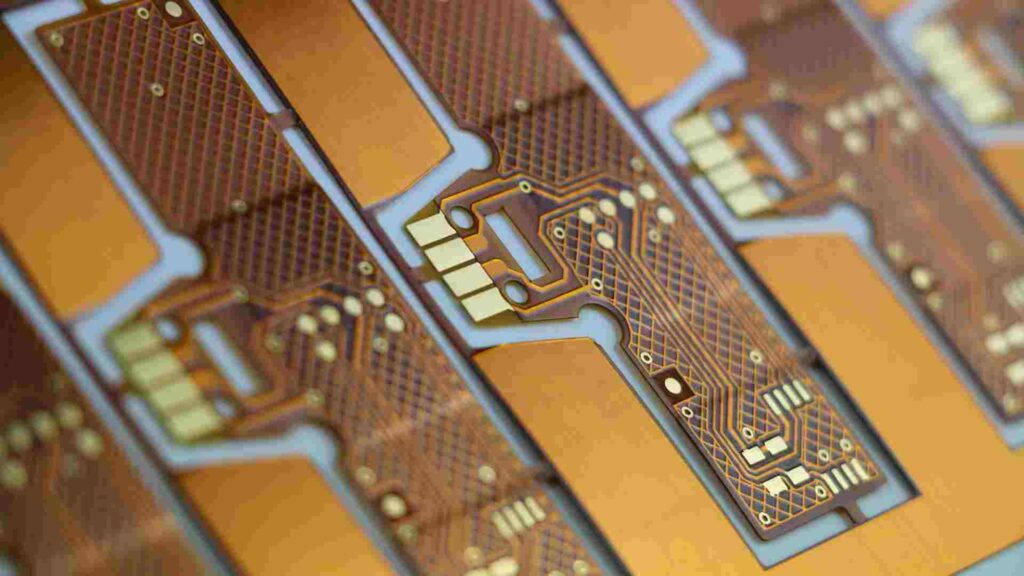
All-flex PCBs, as the name implies, use flexible substrates for the entire board with no sections of rigid fiberglass. This sets them apart from rigid PCBs that use only rigid fiberglass substrates, and rigid-flex PCBs that combine rigid and flexible substrates on the same board.
Construction of All-Flex PCBs
While the substrates used in all-flex PCBs can vary, polyimide films like Kapton are most common. Polyimide offers an excellent balance of flexibility, heat resistance, and chemical resistance. The conductive traces are typically made from rolled annealed copper bonded to the polyimide core. The traces can be designed on one or both sides of the substrate.
Other substrate materials sometimes used in all-flex PCBs include polyester films like PET, flexible FR-4, and PEN. The choice comes down to the required application specifications. Materials like adhesive layers and coverlays are also used to bond and protect the layers.
Vias and component holes/pads are created using processes like laser drilling, punching, or etching. Components are attached on the surface rather than with plated through-holes like on rigid PCBs.
Key Differences from Rigid-Flex PCBs
While rigid-flex PCBs also contain flexible PCB materials, they retain sections of rigid FR-4 PCB substrates to provide structure, mount components, or aid processing. In contrast, all-flex PCBs do away with the rigid sections entirely.
This makes all-flex PCBs thinner, lighter, and able to conform to more complex, dynamic shapes. Without rigid sections, all-flex PCBs can also flex continuously throughout the entire board. The lack of transitions between rigid and flexible materials reduces points of stress/failure.
Ideal Applications for All-Flex PCBs
The flexible and dynamic nature of all-flex PCBs make them well suited for:
- Wearable devices – Can contour safely and comfortably to the human body.
- Internet of things (IoT) – Excellent for small connected devices in a variety of environments.
- Robotics – Allows movement and articulation within joints/appendages.
- Automotive – Can mount safely in tight spaces and withstand vibration.
- Medical – Conforms safely to internal/external body shapes.
- Industrial – Rugged enough for harsh field environments.
- Aerospace – Durable enough to withstand G-forces and space travel.
In short, anywhere that demands maximum flexibility, repeated dynamic flexing, tight space constraints, or rugged use conditions can benefit from the advantages of all-flex PCBs.
Key Benefits of All-Flex PCBs
Now that we’ve explored what sets all-flex PCBs apart, let’s dig into some of the key benefits they offer for reliability, performance, and design.
Increased Reliability
All-flex PCBs intrinsically provide enhanced reliability and longevity compared to rigid or rigid-flex designs. A few factors contribute to this:
- No solder joints – Components are attached directly to the flexible substrate rather than soldered. This eliminates fatigue and cracks from thermal cycling.
- Withstands flexing – The flexible material and traces are designed to dynamically flex without damage. Rigid PCBs often crack.
- Redundant traces – Traces can be duplicated to provide redundancy in case any are damaged.
- No delamination risk – No bonding between rigid and flex sections means no interfacial separation.
- Resists shock/vibration – The flexible board can dampen shocks and vibrations that would crack a rigid PCB.
By removing failure points like solder joints and transition areas, all-flex PCBs avoid common sources of field failures. Their resilient design makes them capable of surviving punishing environments.
Dynamic Flexing and Shape Changing
A key advantage of all-flex PCBs is their ability to repeatedly change shape and bend. The flexible substrates and traces enable:
- Tight bending radii – Can bend to very tight radii of 3-5x the board thickness.
- Dynamic flexing – Can continuously cycle high frequency bending motions without fatigue.
- Multi-axis flexibility – Can bend in X, Y, and Z axis directions.
- 3D shaping – Can conform to complex 3D shapes rather than just 2D curves.
This makes all-flex PCBs ideal for applications involving articulated joints, robots, wearables, and intricately packaged electronics needing to fit tight spaces.
Lightweight and Thinner Profiles
Lacking rigid sections of fiberglass or FR-4, all-flex PCBs tend to have a streamlined weight and size:
- Lower weight – Polyimide and other flex materials have a much lower density than rigid fiberglass.
- Thinner vertical size – No bulky rigid sections results in a thinner cross-section.
- Compact design – Components mount directly on the flexible substrate.
- Easier to package – Easily fits into tight spaces.
The lower weight and profile lend themselves well to wearable and mobile applications where size and weight constraints are critical. It also allows for more compact product enclosures.
Enhanced Heat Dissipation
While rigid PCB substrates like FR-4 are thermal insulators, the polyimide and other flexible materials used in all-flex PCBs are relatively good thermal conductors.
This means all-flex PCBs offer a few thermal advantages:
- Cooling ability – The flex substrates can dissipate heat efficiently.
- Lower operating temperature – This allows electronic components to run cooler.
- No hot spots – Heat does not build up in localized areas as easily.
The thermal design of all-flex PCBs makes them well suited for applications where cooling and temperature management are challenges, such as high power densities or confined spaces.
Improved Impedance Control
Maintaining tight control over trace impedances is critical for many circuits to function properly, especially high frequency, radio frequency (RF), and analog traces.
All-flex PCBs lend themselves to excellent impedance control:
- Consistent dielectrics – No changes between different substrates.
- Precise trace geometry – Etched traces have excellent control over shape and size.
- Stable dimensions – Flexible materials expand/contract minimally with temperature.
- Lower signal loss – Flexible substrates have lower dielectric loss tangents.
This aids in designing reliable, consistent performance for frequency-dependent circuitry and controlled-impedance traces.
Design Considerations for All-Flex PCBs
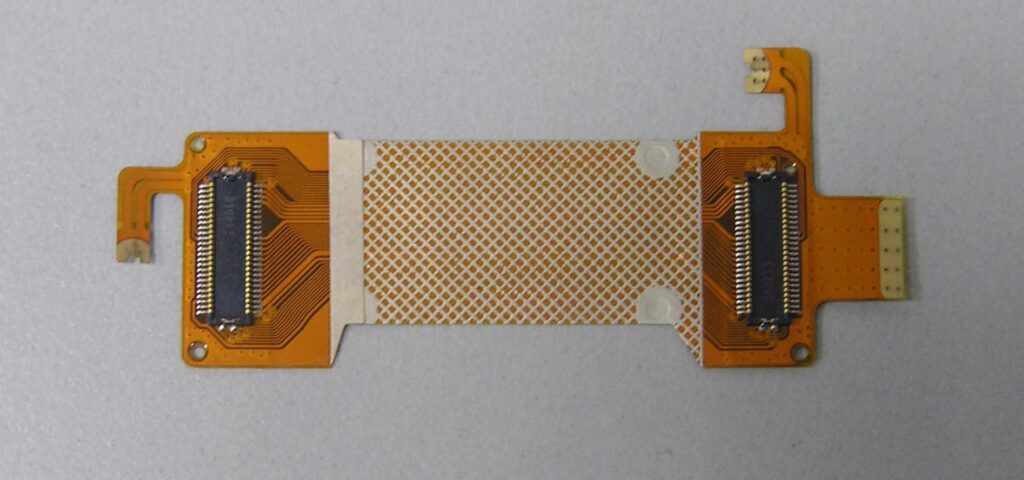
While all-flex PCBs provide many advantages, designing on the flexible substrates does require paying attention to some unique considerations:
Materials Selection
- Choose flexible materials rated for the operating temperature range and conditions expected. Polyimide offers the broadest usefulness.
- Match coefficients of thermal expansion (CTE) of layers and substrates to avoid delamination or warping.
- Consider bonding layers like acrylic adhesives to join layers as needed.
- Use protective coverlay materials over traces in areas exposed to abrasion.
Trace Routing
- Minimize lengths of unsupported traces to avoid excessive flexing motion which can cause metal fatigue.
- Use narrower trace widths to encourage flexibility and durability.
- Route critical traces near the neutral bending axis where stresses are lowest.
- Build in redundant traces in case any are damaged.
Component Mounting
- Use surface mount components rather than through-hole parts.
- Anchor larger components near board anchors/supports to avoid stresses from flexing.
- Reinforce component lead attachments using adhesives or mechanical means.
- Avoid placing connectors or I/O in high-flex zones.
Providing Proper Support
- Avoid forcing sharp, tight bends. Design with appropriate radii for the board thickness.
- Use stiffeners, frames, or retainers in areas where supports are needed for mounting or stability.
- Allow room for displacements from flexing to avoid undue mechanical stresses.
Real-World Applications of All-Flex PCBs
All-flex PCBs are making an impact across a diverse array of fields and applications where their unique properties provide advantages. Here are some examples:
Wearable Technology
Wearable devices like smart watches, health trackers, and head-mounted displays all benefit from the tight spaces, lightweight nature, flexibility, and reliability of all-flex PCBs:
- Conforms to wrists, arms, heads, torsos comfortably and safely.
- Slim, streamlined profile aids aesthetics and ergonomics.
- Withstands bending and motion without fatigue or failure.
- Reliable performance despite sweat, body temperature, impacts.
This makes all-flex PCBs the natural choice for creating performant yet unobtrusive wearable devices.
Internet of Things (IoT) Devices
The flexibility and small size of all-flex PCBs are also highly attractive qualities for Internet of Things edge nodes and sensors:
- Can be deeply embedded into products.
- Enables novel sensing form factors.
- Rugged enough for harsh environments.
- Lightweight facilitates mobility and portability.
These traits support innovative industrial, medical, infrastructure, and consumer IoT device designs.
Robotics and Drones
Robotic joints involve repeated flexing motions which require durable PCBs. Drones experience vibrations and impacts. For both:
- Withstands millions of high frequency flex cycles without issues.
- More compact profile enhances articulated robotic limb mobility.
- Vibration resistance prevents rigid PCB failures.
- Flexibility aids installation in tight spaces of robots.
This enables more robust controllers for drone flight systems and more flexible manipulators and limbs for robots.
Automotive Electronics
The vibration resistance and tight space advantages of all-flex PCBs also suit them for automotive applications:
- Handles under-hood temperatures and temperature cycling.
- Low profile aids installation in tight dashboard compartments.
- Provides vibration dampening for onboard electronics.
- Flexibility allows conforming to curved dashboard shapes.
All-flex PCBs support reliable automotive electronic modules even in exposed, demanding environments.
Medical Electronics
Medical devices like patient-worn health monitors, implants, and surgical equipment operate in sensitive environments close to the human body. For these uses, all-flex PCBs offer key advantages:
- Bio-compatible materials prevent adverse tissue reactions.
- Can safely contour and conform to skin or internal anatomy.
- Extreme reliability requirements are met.
- Sterilization resistance maintains cleanliness.
This facilitates the creation of comfortable, dependable medical electronics even for life-critical applications.
Conclusion
All-flex PCBs provide a compelling option for pushing the boundaries of electronic device capability, reliability, and miniaturization. By relying solely on robust flexible substrates, they maximize dynamic bending ability and ruggedness. Their streamlined size and thermal design also enhance performance possibilities.
While all-flex PCBs require special design considerations, when used appropriately, they enable use cases demanding resilience against demanding operating environments. From medical implants to automotive electronics to cutting-edge robotics, all-flex PCBs deliver capabilities beyond the limits of rigid PCBs.
As electronic applications continue proliferating into all areas of life, all-flex PCB technology ensures those applications meet the most stringent reliability and flexibility needs.
Frequently Asked Questions
What is an all-flex PCB?
An all-flex PCB is a printed circuit board constructed using only flexible substrate materials, such as polyimide films. This differs from rigid PCBs made from fiberglass and rigid-flex PCBs which combine rigid and flexible substrates together.
Why are all-flex PCBs attracting more interest lately?
All-flex PCBs are growing in popularity thanks to their inherent ruggedness and reliability. They withstand dynamic bending and repeated flex cycles extremely well. Their flexible construction also enables innovative applications in wearable devices, medical electronics, robotics, and other fields.
What are some key advantages of all-flex PCBs?
Key advantages include:
- Enhanced reliability from fewer failure points
- Ability to conform to complex, dynamic 3D shapes
- Lighter weight and thinner vertical profile
- Improved thermal dissipation properties
- Excellent impedance control for high frequency traces
What are important design considerations for all-flex PCBs?
Careful material selection, trace routing, component mounting, and providing proper mechanical support are some of the most important considerations when designing all-flex PCBs. Supporting expected dynamic flexing and preventing metal trace fatigue are critical.
What are some examples of real-world applications using all-flex PCBs?
All-flex PCBs are being used in wearable devices, Internet of Things (IoT) nodes, robotics, drones, automotive electronics, and medical devices. Their resilience makes them suitable for demanding flexing, vibration, temperature cycling, and tight space constraints.
Leave a Reply